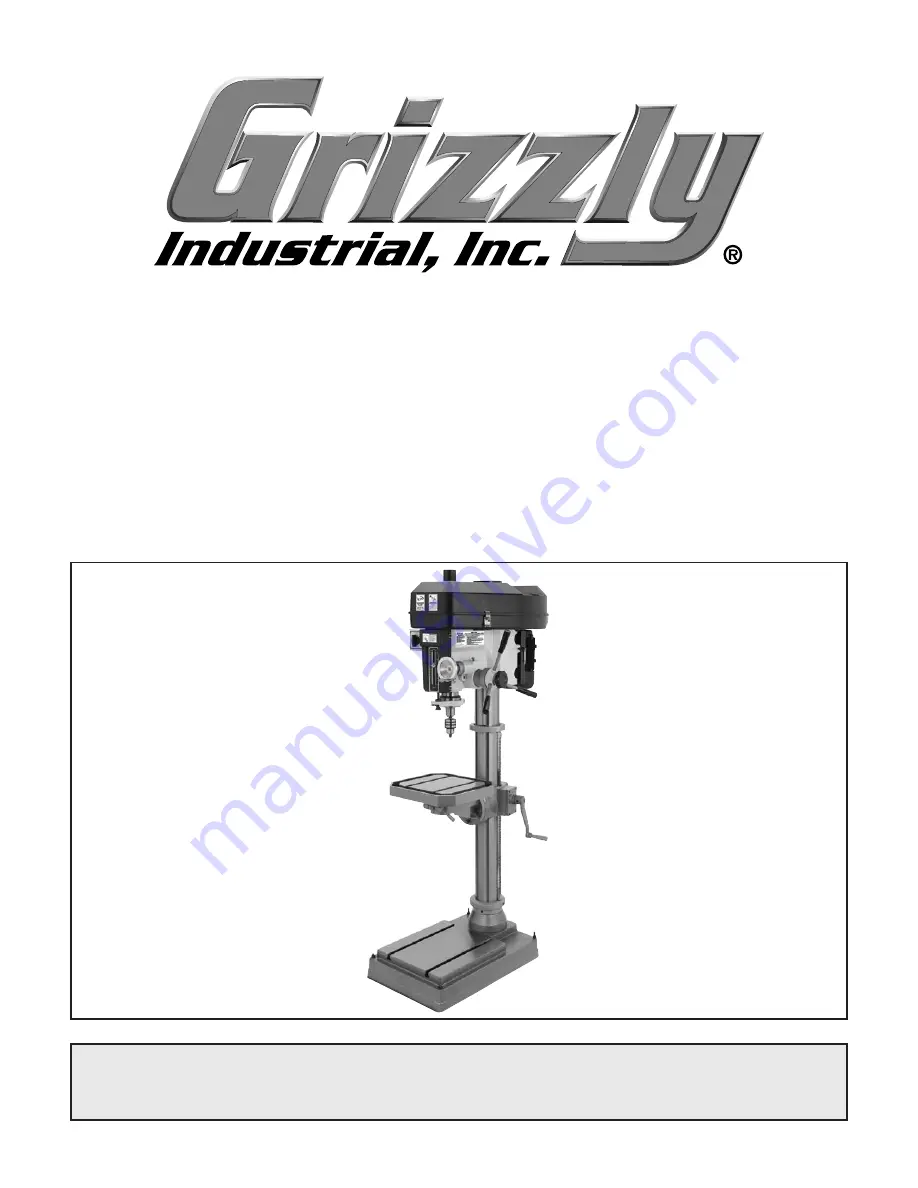
MODEL G0784
15" HEAVY-DUTY
FLOOR DRILL PRESS
OWNER'S MANUAL
(For models manufactured since 03/15)
COPYRIGHT © APRIL, 2015 BY GRIZZLY INDUSTRIAL, INC.
WARNING: NO PORTION OF THIS MANUAL MAY BE REPRODUCED IN ANY SHAPE
OR FORM WITHOUT THE WRITTEN APPROVAL OF GRIZZLY INDUSTRIAL, INC.
#WKBLMN17372 PRINTED IN CHINA
V1.04.15
Summary of Contents for G0784
Page 48: ......