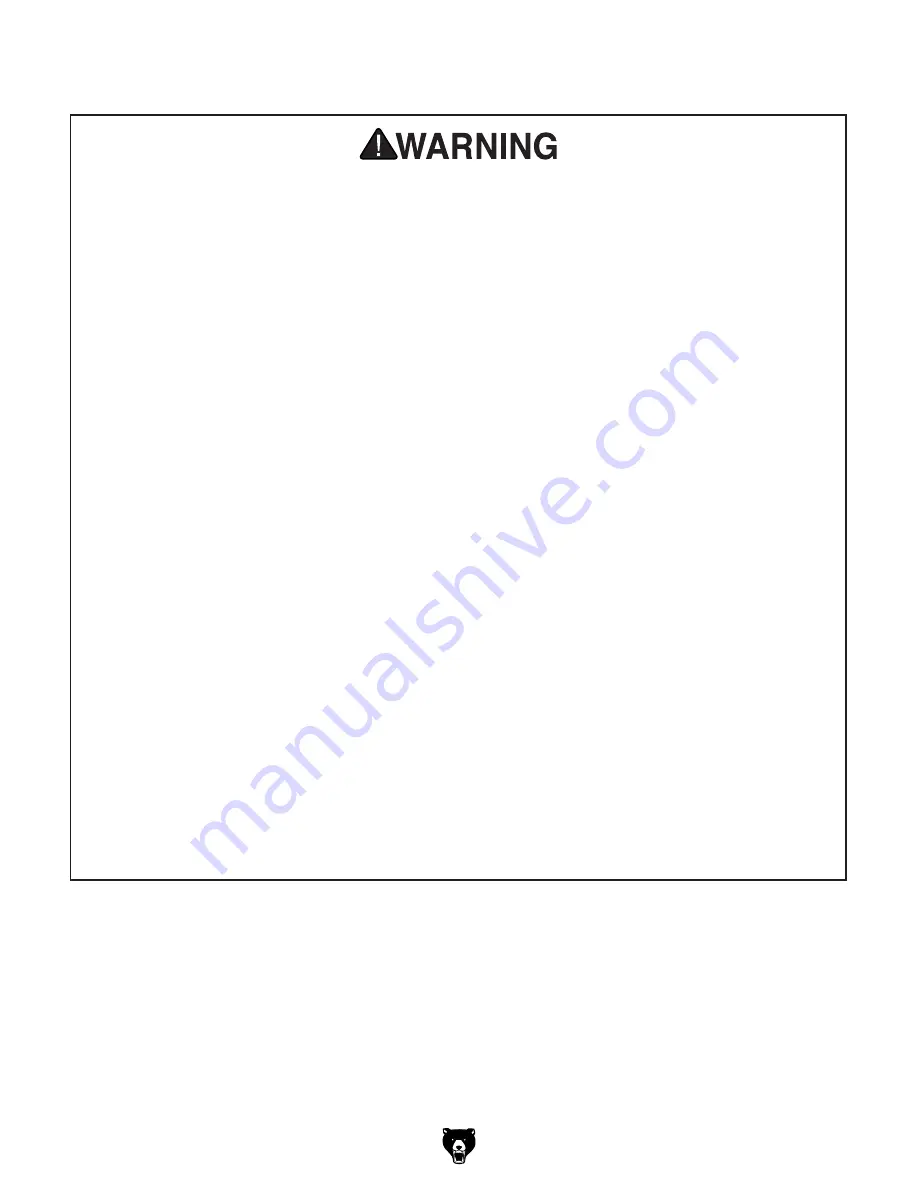
Model G0779 (Mfd. Since 09/14)
-9-
Additional Safety for Drill Presses
Serious injury or death can occur from getting clothing, jewelry, or long hair entangled in
rotating spindle or bit/cutting tool. Contact with rotating bit/cutting tool can result in severe cuts
or amputation of fingers. Flying metal chips can cause blindness or eye injuries. Broken bits/
cutting tools, unsecured workpieces, chuck keys, or other adjustment tools thrown from rotating
spindle can strike nearby operator or bystanders with deadly force. To reduce the risk of these
hazards, operator and bystanders MUST completely heed hazards and warnings below.
DRILLING PREPARATION. To avoid loss of drilling
control or bit breakage, only drill into a flat surface
that is approximately perpendicular to bit. Clear
table of all objects before starting spindle. Never
start spindle with bit pressed against workpiece.
SECURING TABLE AND HEADSTOCK. To avoid
loss of control leading to accidental contact with
tool/bit, tighten all table and headstock locks
before operating drill press.
WORKPIECE CONTROL. An unsecured work-
piece may unexpectedly shift, spin out of con-
trol, or be thrown if bit/cutting tool “grabs” during
operation. Clamp workpiece to table or in table-
mounted vise, or brace against column to prevent
rotation. NEVER hold workpiece by hand during
operation. NEVER start machine with bit/cutting
tool touching workpiece; allow spindle to gain full
speed before drilling.
INSPECTING BIT/CUTTING TOOL. Damaged
bits/cutting tools may break apart during operation
and hit operator or bystanders. Dull bits/cutting
tools increase cutting resistance and are more
likely to grab and spin/throw workpiece. Always
inspect bits/cutting tools for sharpness, chips, or
cracks before each use. Replace dull, chipped, or
cracked bits/cutting tools immediately.
EYE/FACE/HAND PROTECTION. Flying chips
created by drilling can cause eye injuries or blind-
ness. Always wear a face shield in addition to
safety glasses. Always keep hands and fingers
away from drill bit/cutting tool. Avoid awkward
hand positions, where a sudden slip could cause
hand to move into bit/cutting tool.
AVOIDING ENTANGLEMENT. DO NOT wear
loose clothing, gloves, or jewelry. Tie back long
hair. Keep all guards in place and secure. Always
allow spindle to stop on its own. DO NOT stop
spindle using your hand or any other object.
REMOVING ADJUSTMENT TOOLS. Chuck key,
wrenches, and other tools left on machine can
become deadly projectiles when spindle is started.
Remove all loose items or tools used on spindle
immediately after use.
CORRECT SPINDLE SPEED. Using wrong spin-
dle speed can cause bits/cutting tools to break
and strike operator or bystanders. Follow recom-
mended speeds and feeds for each size/type of
bit/cutting tool and workpiece material.
SECURING BIT/CUTTING TOOL. Firmly secure
bit/cutting tool in chuck so it cannot fly out of
spindle during operation or startup.
Summary of Contents for G0779
Page 52: ......