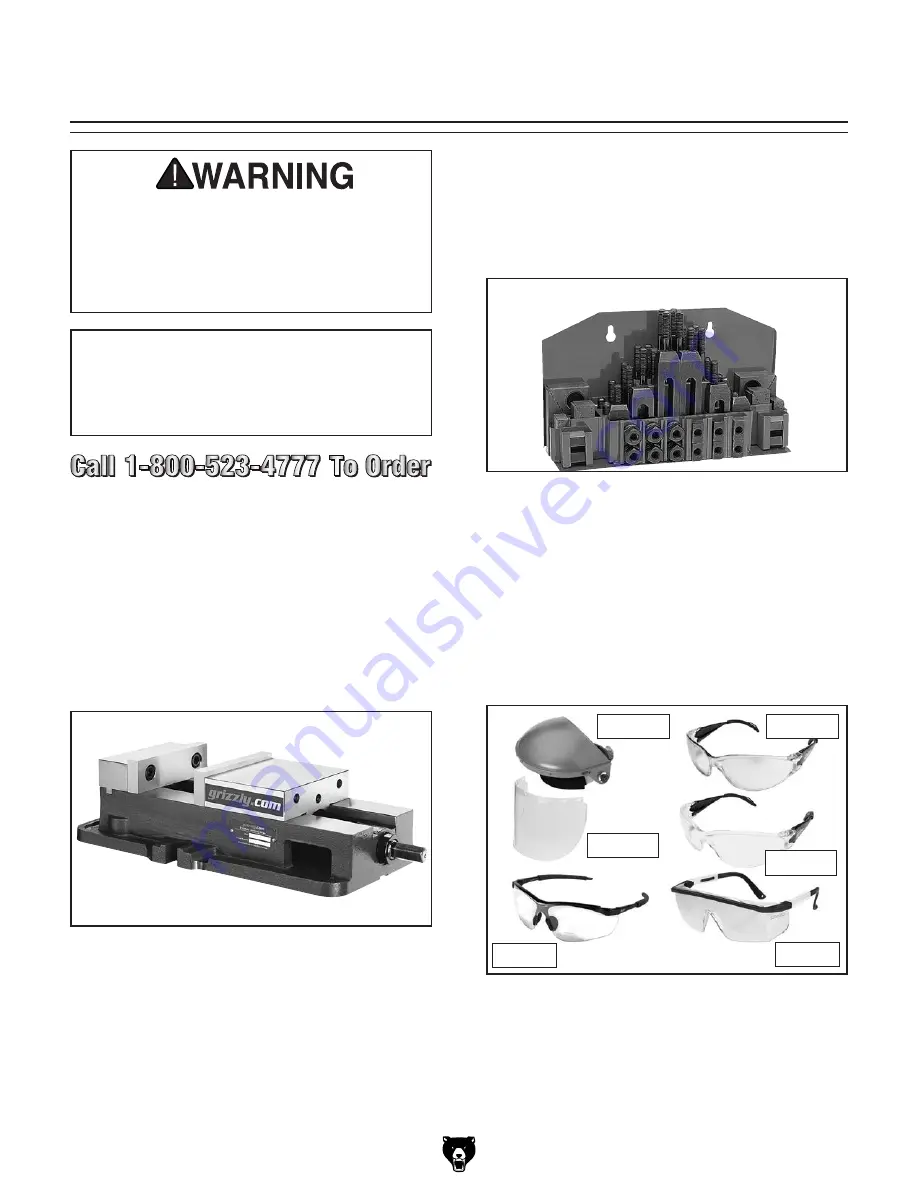
-30-
Models G0728–31 (Mfg. Since 11/11)
SECTION 5: ACCESSORIES
aCCEssoriEs
G1075—52-pC. Clamping Kit
this clamping kit includes 24 studs, 6 step block
pairs, 6 t-nuts, 6 flange nuts, 4 coupling nuts, and
6 end hold-downs. the rack is slotted so it can be
mounted close to the machine for easy access.
Made for
1
⁄
2
" t-slots.
figure 39. g1075 52-pC. Clamping Kit.
T10063—Milling Vise 12
5
⁄
16
" x 6
9
⁄
16
"
T10064—Milling Vise 17
1
⁄
8
" x 8
3
⁄
4
"
•
ultra precise in flatness, parallelism and ver-
ticality.
•
anti-lift mechanism ensures the workpiece
does not lift when jaws are tightened.
•
Ductile iron body.
•
Flame hardened vise bed and jaws.
•
sealed bearing system.
•
8200 lbs. of clamping pressure.
figure 38. t10064 Milling vise (handle included,
but not shown.
Some aftermarket accessories can be
installed on this machine that could cause
it to function improperly, increasing the risk
of serious personal injury. To minimize this
risk, only install accessories recommended
for this machine by Grizzly.
NOTICE
Refer to the newest copy of the Grizzly
Catalog for other accessories available for
this machine.
T20501—face Shield Crown protector 4"
T20502—face Shield Crown protector 7"
T20503—face Shield Window
T20452—"Kirova" Anti-Reflective S. Glasses
T20451—"Kirova" Clear Safety Glasses
H0736—Shop fox
®
Safety Glasses
H7194—bifocal Safety Glasses 1.5
H7195—bifocal Safety Glasses 2.0
H7196—bifocal Safety Glasses 2.5
figure 40. Eye protection assortment.
T20451
H0736
T20452
T20502
T20503
H7194