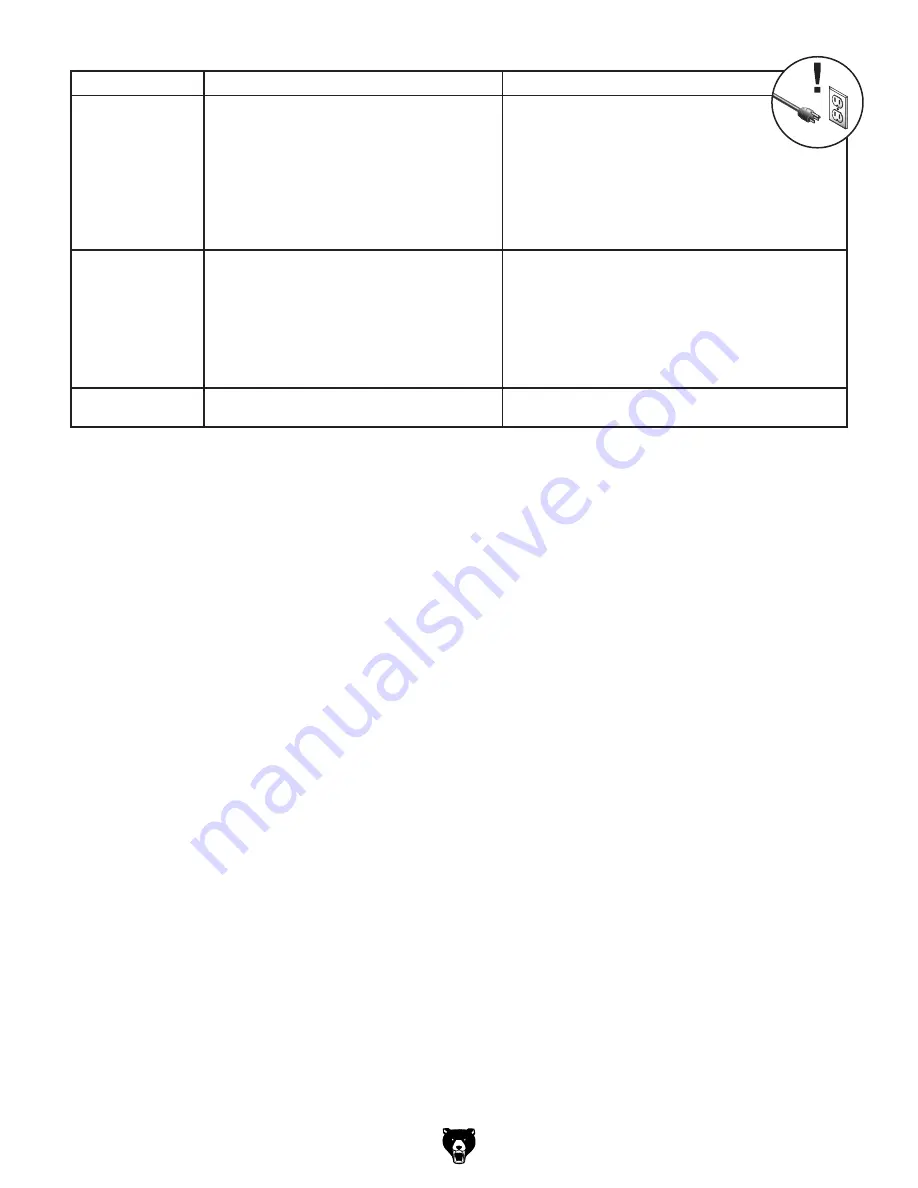
-24-
model g0719 (mfg. since 10/10)
symptom
possible Cause
possible solution
sandpaper clogs
quickly or burns.
1. sandpaper grit is too fine for the job.
2. Workpiece is too moist.
3. sanding depth too aggressive.
4. paint, varnish, pitch, or other coating is
loading up sandpaper.
5. sanding soft workpiece.
1. replace with a coarser grit sandpaper.
2. Allow workpiece to dry out.
3. reduce sanding depth or install coarser
sandpaper.
4. install a coarse grit sandpaper, or strip coating off
before sanding.
5. Use different stock. or, accept the characteristics
of the stock and plan on cleaning/replacing discs
frequently.
glossy spots, burn-
ing, or streaks on
workpiece.
1. sandpaper too fine for the desired finish.
2. Work held still for too long.
3. Workpiece is too moist.
4. sanding stock with high residue.
5. Worn sandpaper.
6. sanding depth too aggressive.
1. Use a coarser grit sandpaper.
2. do not keep workpiece in one place for too long.
3. Allow workpiece to dry out.
4. Use different stock. or, accept the characteristics
of the stock and plan on cleaning/replacing
sandpapers frequently.
5. replace sandpaper.
6. reduce sanding depth or install coarser sandpaper.
Abrasive rubs off
the belt easily.
1. sandpaper has been stored in an incorrect
environment.
1. replace; store sandpaper away from extremely
dry, hot, or damp conditions.