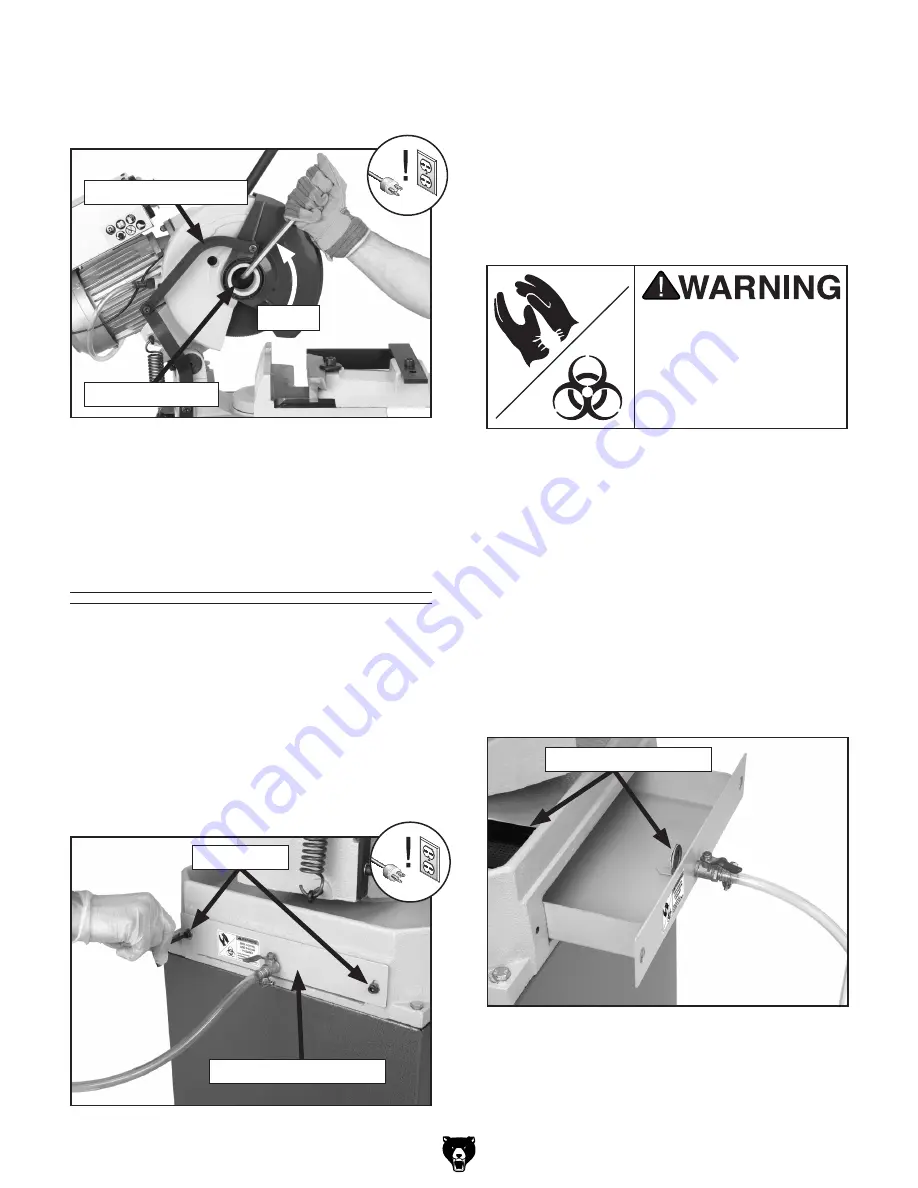
-22-
g0665 slow speed Cold Cut saw
7.
place the blade and flange over the arbor,
then thread and tighten the left-hand thread
arbor cap screw (
figure 32
).
figure 32.
tightening blade.
8.
lower the blade guide and reconnect the
blade guard linkage with the cap screw.
Cutting fluid
Tools Needed:
Qty
hex Wrench 5mm .............................................. 1
filling the cutting fluid reservoir:
1.
disConneCt sAW FroM poWer!
2.
remove the cap screws and washers from
the cutting fluid reservoir (
figure 33
).
Draining/cleaning the cutting fluid
reservoir:
1.
disConneCt sAW FroM poWer!
2.
Wearing protective equipment, drain and dis-
pose the cutting fluid following government-
approved disposal regulations for your area.
3.
use a rag to wipe out residual fluid.
4.
Clean the cutting fluid screens in the machine
base and the tank.
Used cutting fluid pres-
ents a poison hazard.
Use personal protection
when handling this mate-
rial. failure to do so may
result in illness or death.
3.
slide the tray out from the machine base.
4.
Wearing protective equipment, fill the reser-
voir with a suitable, water-based cutting fluid.
refer to the manufacturer's specifications for
the proper water/oil mix.
5.
slide the tray back into the base and replace
the cap screws and washers.
Arbor Cap screw
Blade guard linkage
tighten
figure 33.
opening cutting fluid reservoir.
Cap screws
Cutting Fluid reservoir
figure 33.
opening cutting fluid reservoir.
Cutting Fluid screens