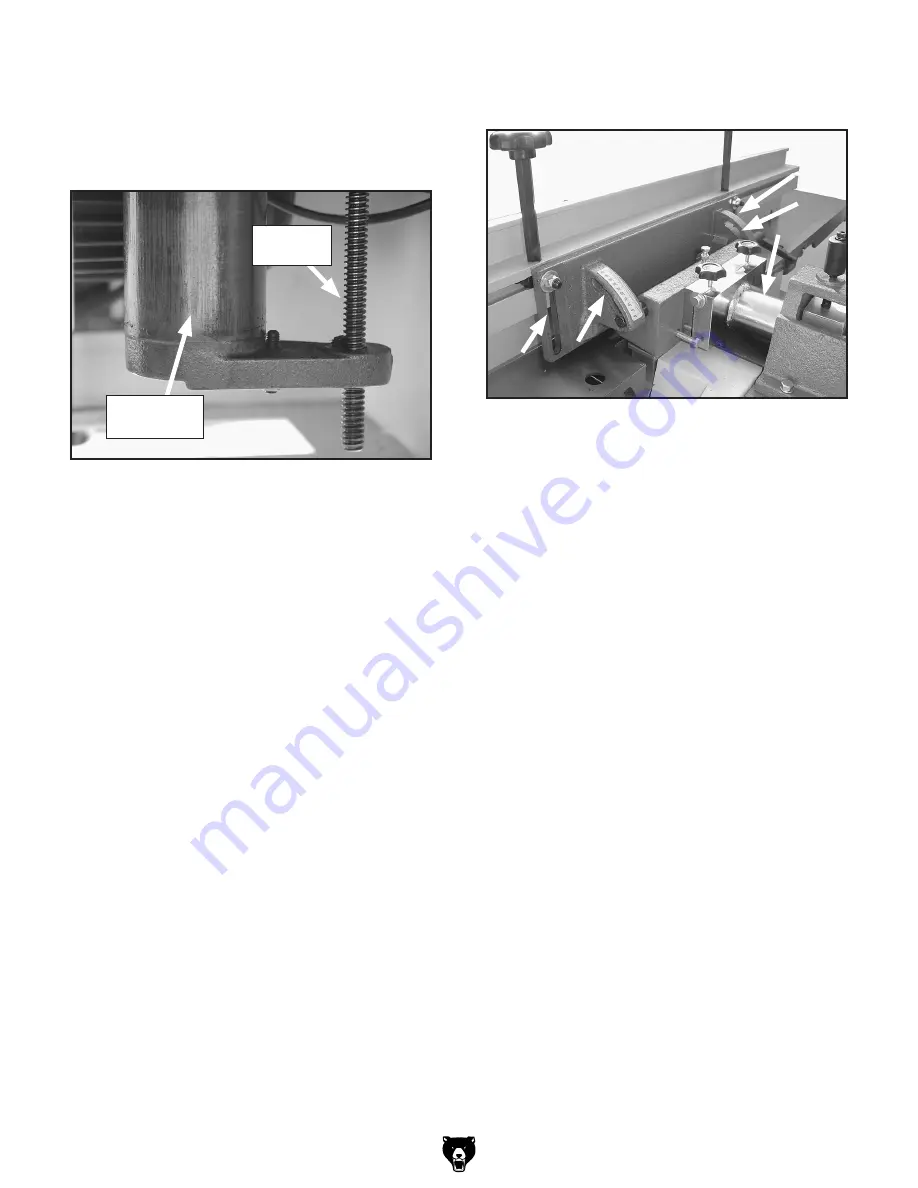
-36-
G0633/G0634 Jointer/Planer Combo Machine
Lead Screw:
The lead screw should be lubri-
cated with multi-purpose grease once a month.
See
Figure 50
and
Parts Beakdown
, P0633411,
Page 61
for location. Remove the left side access
panel for ingress.
Figure 51
. Fence lubrication locations.
Planer Column
: Clean with solvent, wipe dry,
and relubricate with multi-purpose grease when
needed.
Worm Gear:
Inspect every six months and lubri-
cate with multi-purpose grease when needed
(see
Parts Breakdown
, P0633409). Remove
the worm gear box (see P0633407,
Page 61
)
to
inspect.
Figure 50
. Planer column and lead screw.
Planer
Column
Lead
Screw
Fence:
Lubricate with multi-purpose grease when
needed in the locations shown in
Figure 51
.
Summary of Contents for G0633
Page 2: ......
Page 5: ...G0633 G0634 Jointer Planer Combo Machine 3...
Page 6: ...4 G0633 G0634 Jointer Planer Combo Machine...
Page 7: ...G0633 G0634 Jointer Planer Combo Machine 5...
Page 8: ...6 G0633 G0634 Jointer Planer Combo Machine...
Page 10: ...8 G0633 G0634 Jointer Planer Combo Machine...
Page 11: ...G0633 G0634 Jointer Planer Combo Machine 9...
Page 17: ...G0633 G0634 Jointer Planer Combo Machine 15 Hardware Recognition Chart...
Page 56: ...54 G0633 G0634 Jointer Planer Combo Machine Wiring Diagram...
Page 57: ...G0633 G0634 Jointer Planer Combo Machine 55 Stand Assembly Parts Breakdown...
Page 60: ...58 G0633 G0634 Jointer Planer Combo Machine Cutterhead Motor Breakdown...
Page 65: ...G0633 G0634 Jointer Planer Combo Machine 63 Fence Guard Breakdown List...
Page 69: ......
Page 70: ......
Page 71: ......
Page 72: ......