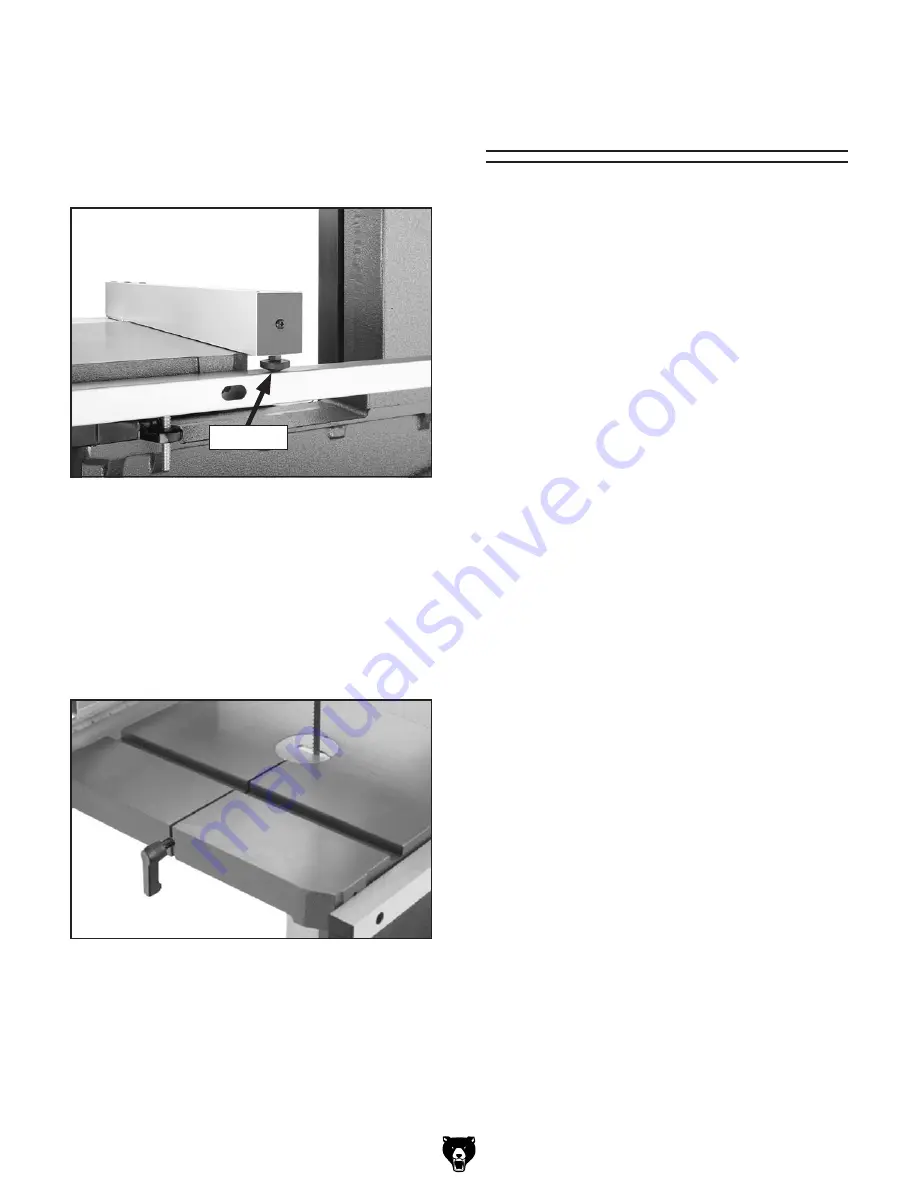
G0555LX
(Mfg. Since 3/13)
-19-
17. install the table insert and table pin, as show
in
figure 20.
important: Make sure you re-install the table
pin. This pin keeps the table surfaces on
either side of the slot even with the chang-
es in operating pressures and temperature
changes.
figure 20. table pin and insert installed.
figure 19. Fence rail pad installed.
rail pad
16. thread the M6-1 hex nut onto the fence rail
pad, then thread it into the rear underside of
the fence (see
figure 19) so that the fence
rests the same height above the table along
its full length. tighten the hex nut against the
fence to secure the setting.
adjustment
overview
the bandsaw is one of the most versatile wood-
working machines. as such it has multiple compo-
nents that must be properly adjusted for the best
cutting results.
For safety reasons some adjustments and test
operations must be performed before performing
other necessary adjustments. below is an over-
view of all the adjustments and the order in which
they should be performed.
adjustment procedures include:
• blade tracking
• dust Collection
• power Connection
• test run
• tension blade
• adjusting blade support bearings
• adjusting blade guide bearings
• table tilt Calibration
• aligning table
• aligning Fence