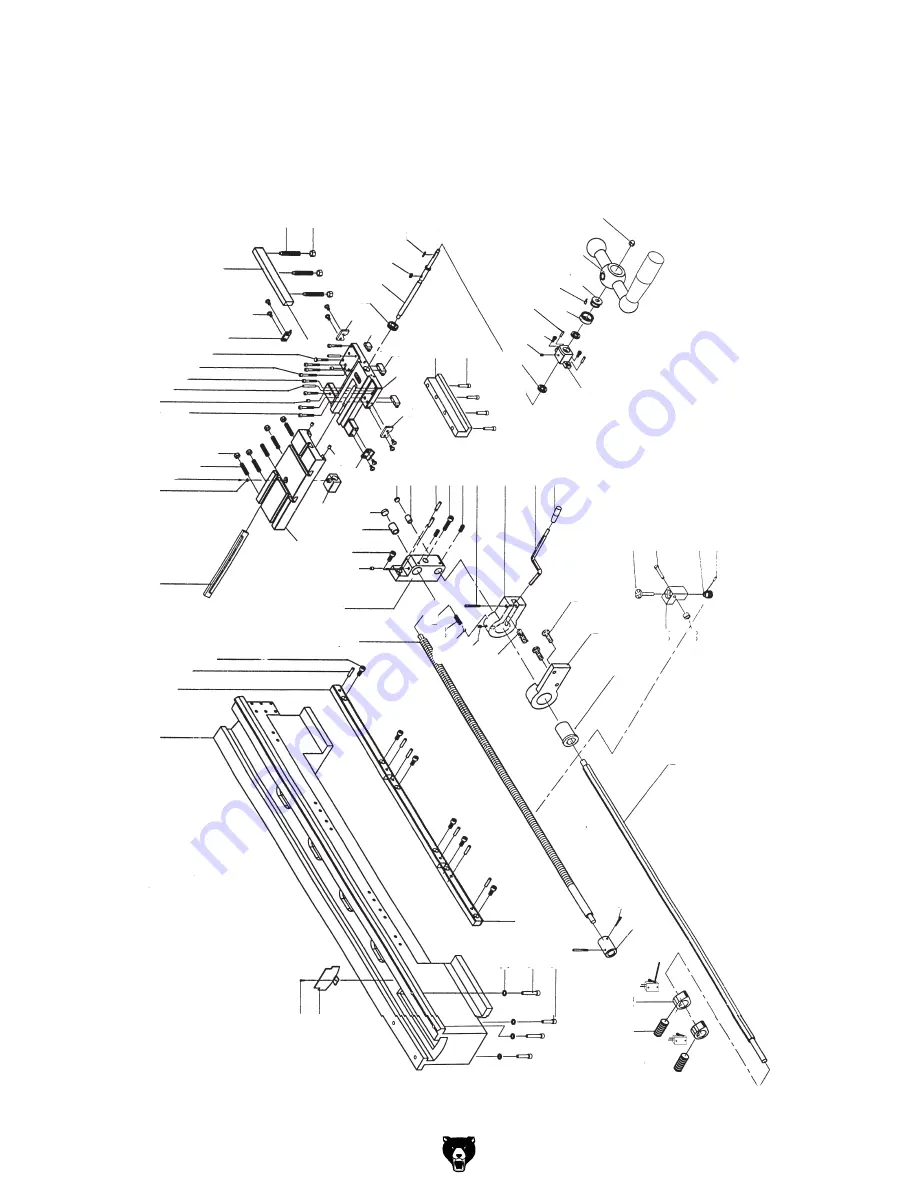
-56-
G0492 12" X 36" Combo Lathe/Mill
Bed Diagram
(4000 Series Parts)
4079
4078
4075
4076
4077
4073
4072
4071
4070
4064
4074
4063
4061
4084
4085
4083
4082
4081
4080
4069
4068
4067
4047
4049
4050
4051
4036
4028
4030
4032
4033
4034
4035
4038
0374
4023
4024
4025
4026
4041
4040
403
9
4022
4021
4044
4045
4042
4043
4019
4020
4001
4005
4006
4007
4008
4009
4013
4014
4015
4016
4017
4018
4072-1
4002
4003
4004
4012
4011
4010
4048
4062
4065
4066
4027
4031
4029
4046
4052 4053
4054 4055 4056 4057
4058
4059
4060
Summary of Contents for G0492
Page 2: ... ...
Page 9: ...G0492 12 X 36 Combo Lathe Mill 7 ...
Page 10: ... 8 G0492 12 X 36 Combo Lathe Mill ...
Page 33: ...G0492 12 X 36 Combo Lathe Mill 31 Change Gear Chart ...
Page 56: ... 54 G0492 12 X 36 Combo Lathe Mill Compound Rest and Tool Post Diagram 3500 Series Parts ...
Page 60: ... 58 G0492 12 X 36 Combo Lathe Mill Steady Rest and Follow Rest Diagram 4500 Series Parts ...
Page 73: ...G0492 12 X 36 Combo Lathe Mill 71 ...
Page 74: ... ...
Page 75: ......
Page 76: ... ...