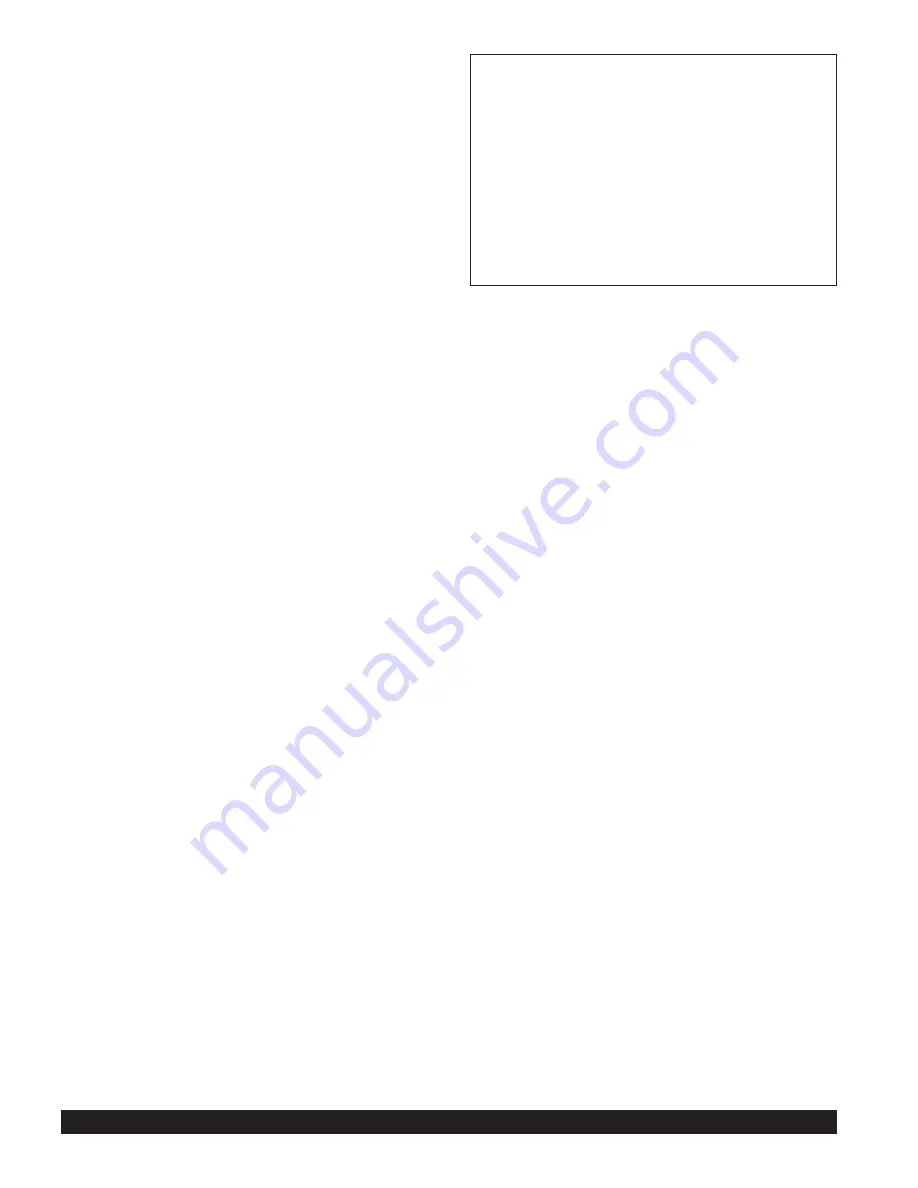
Page 14
G & MG Series Granita Machine
Crathco Granita Preventive
Maintenance (PM)
Checklist for Kit 90566 -
Serial # 11259 and above
(and units with lower serial #’s that have been
converted to stainless steel shafts - units with
black stainless shafts will need to be converted
using PM Kit # 90110B)
A preventive maintenance visit should be performed every 6 months. In addition, air filter should be cleaned weekly,
and every three months the condenser should be cleaned, and the rubber shaped bell shaft seals should be
replaced. Failure to complete PM’s every 6 months is considered abuse of the machine, and therefore voids the
warranty. Proof of PM must be documented with Grindmaster Corporation to maintain warranty coverage. To docu-
ment your PM, complete this form with signatures, place used/worn parts that were replaced during the PM inside
envelope, and mail to Grindmaster Corporation. Parts returned should include 2 evaporator seals, 2 rubber bell
shaped shaft seals, valve o-rings and shafts (if applicable). First PM on serial numbers 11259 to 12202 should also
include kit number 90225 (one per serial number).
The following procedures should be performed during a Preventative Maintenance visit, using PM kit # 90566
or 90110B.
Document model and serial number of equipment and record above.
Check product temperature and consistency for proper setting - adjust if necessary.
Insure product is being mixed properly and is within specification (check and document brix - most products
should be around 13% - refer to product manufacturer’s recommendations for exact recommended brix).
Record Brix reading here: Left Bowl _____ Right Bowl _____
Check for leaks at gaskets, o-rings, front shaft seal, etc.
Empty product from bowls and disassemble unit completely.
Clean and sanitize all disassembled parts.
Clean and sanitize top tray and freezing barrel.
Clean out condensation tube with sanitizer and long brush.
Check condition of all panels, bowls, lids - replace if necessary.
Check mixing rods and augers for wear, check mixing rod bearing for wear - replace if necessary.
Check for bowl knobs (two per bowl to lock down bowl in front) - replace if necessary.
Check operation of lights in lid and rear of unit (if equipped) - replace light bulbs if necessary.
Clean re-usable air filter. Check condition of filter and replace if necessary.
Clean condenser.
Check condition of bowl gaskets and replace if necessary.
Replace all o-rings on dispense valves and lubricate.
Check drive shaft. Replace if necessary, using PM kit #90110B in place of 90566 above.
Replace evaporator seal in front of evaporator. (use brass tool, included, to slide seal onto shaft, and use the
white tool to tap seal into place. Be sure to lubricate seal with food grade grease first)
Replace bell shaped rubber shaft seal on front of freezing barrel (generously lubricate inside seal)
Lubricate parts where appropriate (dispense valve o-rings, inside of shaft seal, inner rim of bowl where it meets
with the bowl seal)
Re-assemble unit and refill with product
Verify and document defrost timer setting and operation and time of day setting and adjust if necessary.
Check thermostat setting on MG models. Thermostat setting should be between 1-1/2 and 2.
Verify compressor operation and freezer controller operation.
Verify ventilation is adequate (8” on both sides and back)
Check electrical connections and wiring.
Check fan operation (1 condenser fan and 2 gear motor fans) and clean fan or blades if necessary.
Review proper periodic care and cleaning instructions (disassembly, cleaning, sanitizing, lubrication and
re-assembly) with store personnel. Review proper product mixing and handling instructions with store personnel
Demonstrate and train store personnel to follow proper procedures (stress importance of store level
maintenance such as lubrication and filter cleaning).
Make sure store personnel have appropriate supplies (lubricant and sanitizer) to care for machine.
Model # ___________________________
Serial # ____________________________
Date: ______________________________
PM by _____________________________
Of Company ________________________
Store Name/# _______________________
Address ___________________________
__________________________________
Store Mgr Name ____________________
Signature __________________________
Summary of Contents for Crathco G23-2B
Page 21: ...G MG Series Granita Machine Page 21 Exploded View G23 2B 115 60 serial number 8195 and higher ...
Page 23: ...G MG Series Granita Machine Page 23 Exploded View G235 2B 220 50 ...
Page 24: ...Page 24 G MG Series Granita Machine Exploded View MG235 2B 220 50 ...
Page 25: ...G MG Series Granita Machine Page 25 Exploded View G236 2B 220 60 ...
Page 26: ...Page 26 G MG Series Granita Machine Exploded View MG236 2B 220 60 ...
Page 34: ......
Page 35: ......