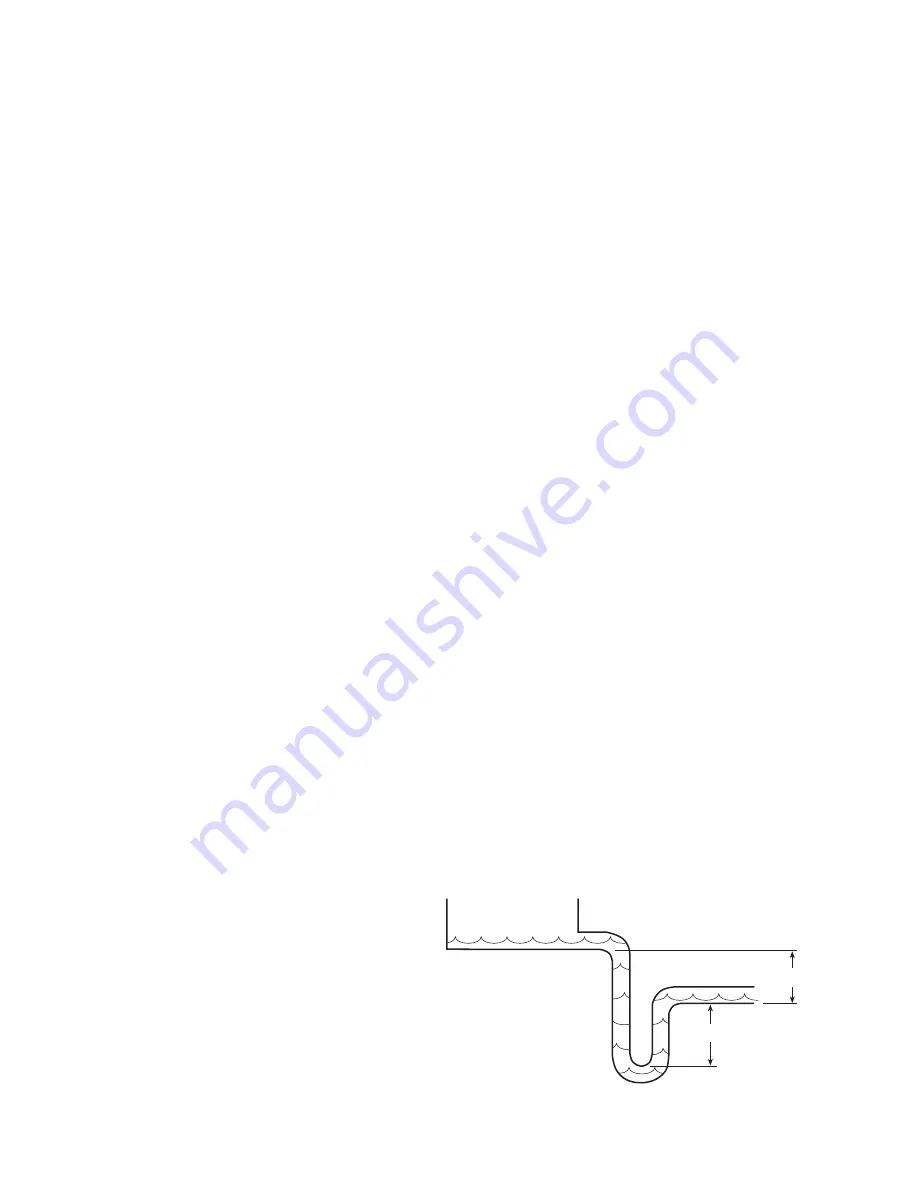
8
Water Coils
1.
Piping should be in accordance with accepted industry standards. Pipework should be supported
independently of the coils. Water pipes are copper with sweet connections. USE WET TOWEL TO AVOID
BURNING COIL CONNECTION GROMMETS. When installing coupling, do not apply undue stress to the
connection extending through the unit. Use a back-up pipe wrench to avoid breaking the weld between
coil connection and header.
2.
Connect the WATER SUPPLY TO THE BOTTOM CONNECTION on the air-leaving side and the WATER
RETURN TO THE TOP CONNECTION on the air-entering side. The extra bottom connection can be used
for an auxiliary manual drain connection, and the extra top connection may be used for an automatic air
vent or the extra connections can be capped. To insure proper venting, an external air vent in the piping
is recommended. Connecting the supply and/or return in any other manner will result in very poor
performance. CAP UNUSED CONNECTIONS.
3.
The air vent at the uppermost point should be temporarily opened during system start-up to release all
of the air from the coil. To maintain heat transfer capacity, periodically vent any air in coil. Vent is
to be located behind connections side access door.
4.
Water coils are not normally recommended for use with entering air temperatures below 40ºF. No control
system can be depended on to be 100% safe against freeze-up with water coils. Glycol solutions or
brines are the only safe media for operation of water coils with low entering air conditions.
CONTINUOUS WATER CIRCULATION THROUGH THE COIL AT ALL TIMES IS HIGHLY RECOMMENDED.
5.
Pipe sizes for the system must be selected on the basis of the head (pressure) available from the
circulation pump. Piping should be in accordance with accepted industry standards.
6.
For chilled water coils, the condensate drain pipe should be sized adequately to ensure the condensate
drains properly. See
DRAIN PAN TRAPS
and Figure 4.
Direct Expansion (DX) Coils
1.
Piping should be in accordance with accepted industry standards. Pipework should be supported
independently of the coils. Undue stress should not be applied at the connection to coil headers.
2.
The condensate drain pipe should be sized adequately to ensure the condensate drains properly. See
DRAIN PAN TRAPS
and Figure 4.
3.
When connecting suction and liquid connections make sure the coil is free from all foreign material. Make
sure all joints are tight and free of leakage.
4.
Dual circuits are recommended to be run by two compressors. One compressor with the appropriate
valves and piping can be used but is not recommended. Greenheck does not supply compressor or
condensing units, for further instruction on DX coil installation and operation contact your compressor
and/or condenser manufacturer.
DXI coils have dual connections and should be used with two compressors.
Drain Pan Traps
Drain lines and traps should be run full size from
the drain pan connection. Drain pans should have
drain lines and traps to permit the condensate
from the coils to drain freely. On all units with drain
pans, the trap depth and the distance between the
trap outlet and the drain pan outlet should be
twice the static pressure in the drain pan section
under normal operation to assure the trap remains
sealed.
Figure 4 - Drain Pan Trap
2P = min.
2P = min.
Hot Water, Chilled Water & DX Coils