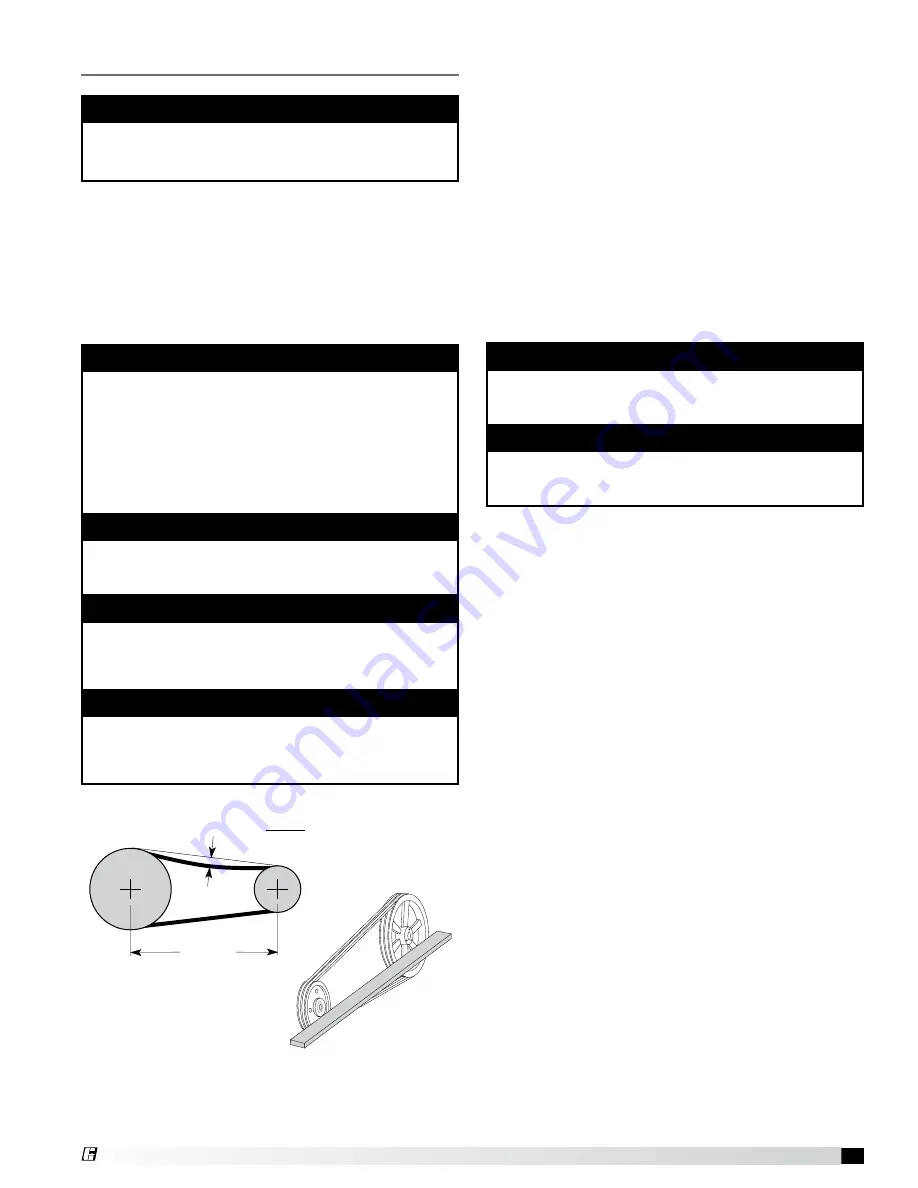
33
®
Model MSX Make-Up Air
Maintenance - Routine
CAUTION
Lock-out the gas and the electrical power to the
unit before performing any maintenance or service
operations to this unit.
V-Belt Drives
V-belt drives must be checked on a regular basis for
wear, tension, alignment, and dirt accumulation.
Check the tension by measuring the deflection in the
belt as shown below.
Check the alignment by using a straight edge across
both sheaves as shown below.
Snow Accumulation
Clear snow away from roof mounted units. Keep the
snow clear of the intake and access doors.
Motors
Motor maintenance is generally limited to cleaning
and lubrication (where applicable).
Cleaning should be limited to exterior surfaces only.
Removing dust and grease build-up on the motor
assures proper motor cooling.
Motors supplied with grease fittings should be
greased in accordance with the manufacturer’s
recommendations.
Wheels
Wheels require little attention when moving clean air.
Occasionally oil and dust may accumulate on the wheel
causing imbalance. When this occurs the wheel and
housing should be cleaned to assure proper operation.
Belt Tension
Belt Span
Deflection = Belt Span
64
FAN
MOTOR
FAN
MOTOR
Drive Alignment
IMPORTANT
Premature or frequent belt failures can be caused by
improper belt tension, or misaligned sheaves.
• Abnormally high belt tension or drive
misalignment will cause excessive bearing loads
and may result in failure of the fan and/or motor
bearings.
• Abnormally low belt tension will cause squealing
on start-up, excessive belt flutter, slippage, and
overheated sheaves.
IMPORTANT
Do not pry belts on or off the sheave. Loosen belt
tension until belts can be removed by simply lifting
the belts off the sheaves.
IMPORTANT
When replacing V-belts on multiple groove drives,
all belts should be changed to provide uniform drive
loading.
IMPORTANT
Do not install new belts on worn sheaves. If the
sheaves have grooves worn in them, they must be
replaced before new belts are installed.
IMPORTANT
Do not allow water or solvents to enter the motor
or bearings. Motors and bearings should never be
sprayed with steam, water or solvents.
IMPORTANT
Greasing motors is only intended when fittings are
provided. Many motors are permanently lubricated,
requiring no additional lubrication.