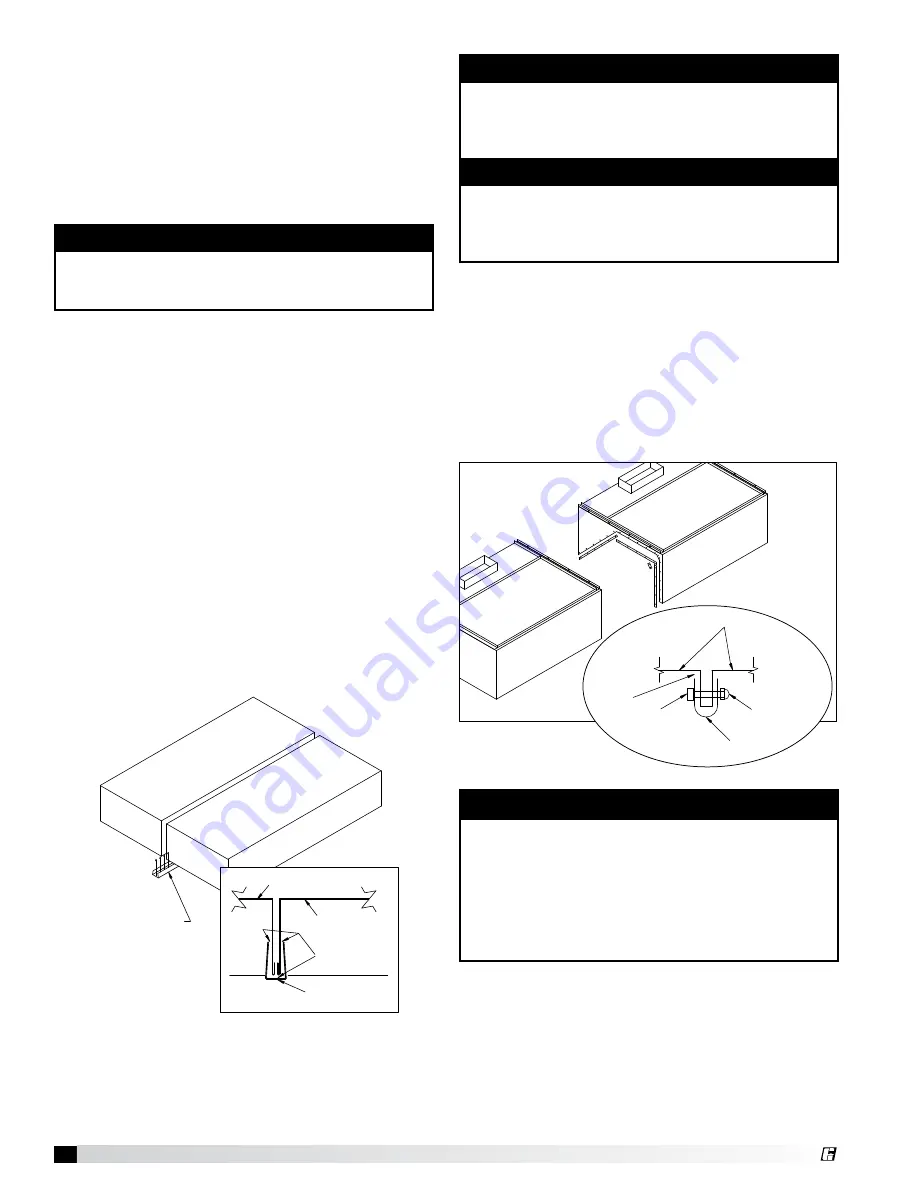
8
Model GGH2O
®
NOTE
•
For multiple hood systems that have more than
14 lights total (incandescent or fluorescent), the
hood lights must be wired to multiple circuits.
Each circuit must have less than 14 lights total.
• Light bulbs are not provided. Standard light bulbs
up to 100 watts may be used.
Double Island Style Hoods
A double island hood is created by installing two
wall style hoods back to back. Use the installation
procedure for single island hoods; install and level
both hoods. After leveling, secure the hoods together
by tack-welding and/or bolting the rear mounting
brackets. Caulk this joint with NSF Approved silicone
caulk (GE SCS1000 or its equivalent). The caulk is not
provided.
Hood
Bolt
Caulk
U-Clip
Acorn Nut
Ho
od
Fr
ont
Ho
od
Fr
ont
1. Remove support angle on open end panel.
2. Raise all hoods into appropriate location and support per construction plans.
3. Fasten top angles together using 1/4 in. bolts and nuts (by others).
4. Fasten hoods together using u-clips, 1/4 inch bolts and cap nuts as indicated.
5. Caulk all seams as necessary.
Hood
Bolt
Caulk
U-Clip
Acorn Nut
Ho
od
Fr
ont
Ho
od
Fr
ont
1. Remove support angle on open end panel.
2. Raise all hoods into appropriate location and support per construction plans.
3. Fasten top angles together using 1/4 in. bolts and nuts (by others).
4. Fasten hoods together using u-clips, 1/4 inch bolts and cap nuts as indicated.
5. Caulk all seams as necessary.
Continuous Capture Plenum Hoods
Remove the support angles on the open end panels.
Use the installation procedure described for single
island hoods; install and level both hoods. After
leveling, secure the hoods together by tack-welding
and/or bolting the top angles. Fasten the hoods
together using u-clips and bolts. Caulk this joint with
NSF Approved silicone caulk (GE SCS1000 or its
equivalent). The caulk is not provided.
NOTE
Before hanging the hoods, please verify the hood
marks to make sure the correct hood is hung on the
correct side.
Installing U-Channel Strip
1. After the hood is hung in position and leveled,
apply caulk to the inside edge of the double island
clip.
2. Position and install the clip by tapping into
position along clip (friction fit).
3. Caulk edges to seal out grease and allow for ease
of cleaning. Caulk with NSF Approved silicone
caulk, GE SCS1000, or its equivalent. The caulk is
not provided.
Hood Hanging Height
The hood hanging height is critical. Hanging the hood
at the incorrect height may significantly reduce the
ability for the hood to function properly and may be in
violation of codes. The hood hanging height (typically,
78 in. (198.12 cm) above the finished floor) is given on
the UL label located on the inside of the hood on the
end panel. The hood must be hung level to operate
properly.
NOTE
The installation of the canopy hoods shall be
in accordance with NFPA 96 (latest edition),
Standard for Ventilation Control & Fire Protection of
Commercial Cooking Operations.
NOTE
Greenheck does not recommend walking or
standing on the hood top as damage can result. If
you must walk on the hood top, protect the hood
with additional support or planks for flooring.
DETAIL A
Double Island Clip
Silicone Caulk
Hood-1A
Hood-1B
Installation Instructions.
1. After hood is hung in position and leveled…
2. Apply silicone caulk to inside of double island clip.
3. Position and install clip by tapping into position along clip (friction fit).
4. Caulk edges to seal out grease and allow for ease of cleaning.
Ho
od
-1B
Ho
od
-1A
Ho
od
Fr
on
t
Double Island Clip
DETAIL A
Double Island Clip
Silicone Caulk
Hood-1A
Hood-1B
Installation Instructions.
1. After hood is hung in position and leveled…
2. Apply silicone caulk to inside of double island clip.
3. Position and install clip by tapping into position along clip (friction fit).
4. Caulk edges to seal out grease and allow for ease of cleaning.
Ho
od
-1B
Ho
od
-1A
Ho
od
Fr
on
t
Double Island Clip