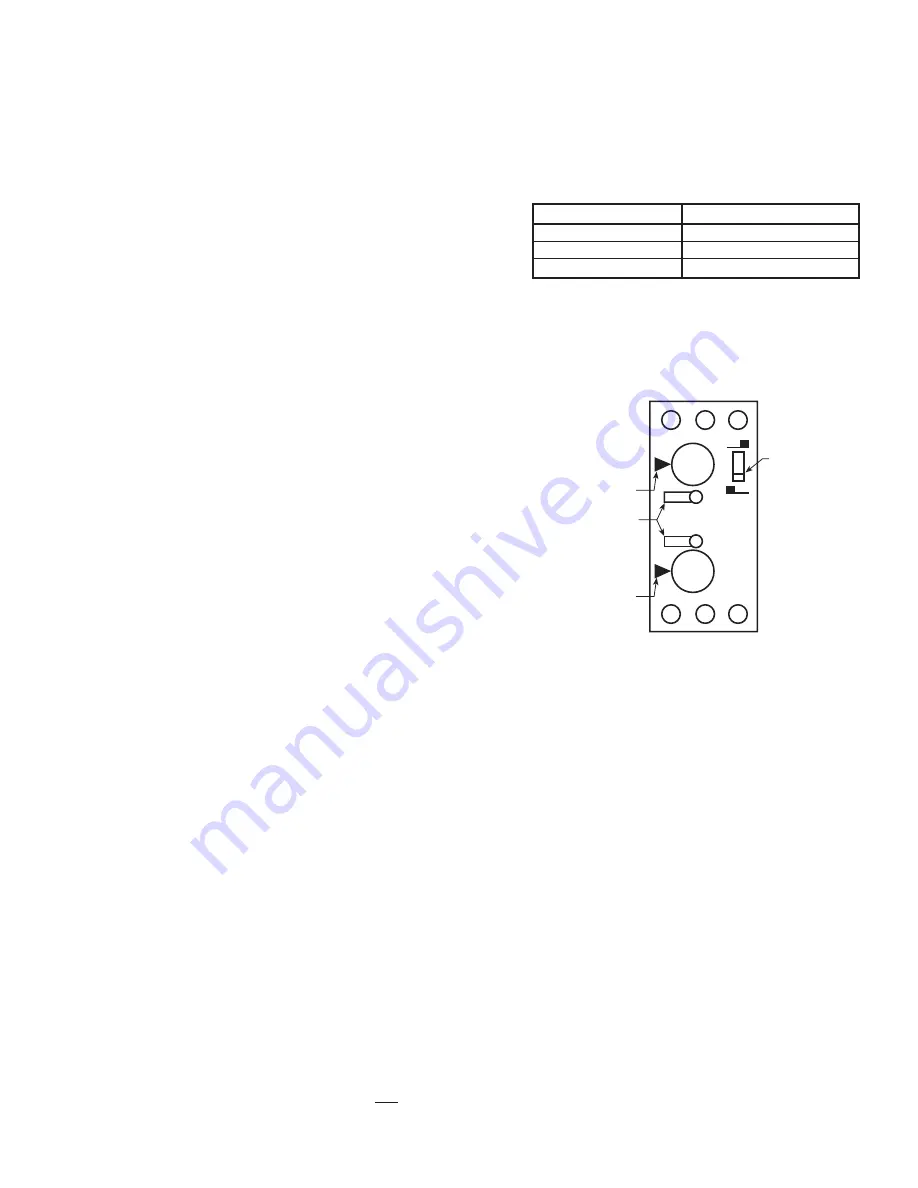
FROST CONTROL APPLICATION/OPERATION
DIRTY FILTER SWITCH SETUP
When outdoor air temperatures are extremely cold, moisture condensation and frosting on the energy recovery
wheel is possible. Frost control is an optional feature that will prevent wheel frosting. Two options are available:
1) Timed Exhaust frost control and
2) Preheat frost control
Timed exhaust frost control
includes a thermostat (with
probe) mounted in the supply air inlet compartment (see
FIGURE 13, page 10) and a timer (Figure 12) mounted in the
ERH control center. The thermostat will turn on the timed
exhaust frost control feature at a predetermined field
adjustable outdoor air temperature (referred to as the Frost
Threshold temperature). The typical temperature setting
corresponds to the indoor air relative humidity as shown in TABLE 6.
Testing
(refer to FIGURE 12)
• Set the
Timer Scale
for T1 and T2 to 1 minute. Set
the
Timer Settings
for T1 and T2 to 1.0. Set the dip
switch to the down position.
• Turn the temperature sensor up as high as possible.
The supply blower should cycle on for one minute,
then turn off for one minute.
• After testing, set the
Timer Scale
as follows: T1 = 10
minutes, T2 = 1 hour
• Set the
Timer Settings
as follows: T1 = 0.5, T2 =
0.5. The timer is now set for 5 minutes off and 30
minutes on.
Preheat frost control
(see FIGURE 11, page 8) includes a
thermostat (with probe) and an electric heater located in the
supply air inlet compartment and an air pressure switch in the
supply air outlet compartment. The thermostat should be set
according to the Frost Threshold temperatures shown in TABLE 6.
When the outdoor air temperature reaches the thermostat setting,
the electric preheater will turn on and warm the air entering the energy
wheel.
Testing
• Turn the thermostat as high as it will go. The heater should turn on.
• If it doesn’t, either put the supply side doors on or temporarily jumper the
air pressure switch to avoid nuisance tripping of the pressure switch.
Remember to remove the jumper.
9
A1
B1
15
16
18
A2
0.2
0
0.4
1.0
0.6
0.8
0.2
0
0.4
1.0
0.6
0.8
T1
T2
T2
1 MIN
T1
1 MIN
Timer
Scale
Dip
Switch
Indoor RH @ 70°F
Frost Threshold Temp
20%
-10°F
30%
-5°F
40%
0°F
TABLE 6
FIGURE 12
This unit may be equipped with a dirty filter switch that functions on differential air pressures to close a relay
when the unit filters are clogged and need cleaning. This switch has not been set at the factory due to external
system losses that will affect the switch. This switch will need
minor field adjustments
after the unit has been
installed with all ductwork complete. The dirty filter switch is mounted in the exhaust inlet compartment next to
the electrical control center.
To adjust the switch the unit must be running with all of the access doors in place, except for the compartment
where the switch is located (exhaust inlet compartment). Remove the switch cover plate. The adjusting screw is
located on the top of the switch. Open the filter compartment and place a sheet of plastic or cardboard over
50% of the filter media. Replace the filter compartment door. Check to see if there is power at the alert signal
leads (refer to electrical diagram). If there is no power, turn the adjustment screw on the dirty filter gage
clockwise until you have power. Open the filter compartment and remove the obstructing material. Replace the
door and check to make sure that you do not have power at the alert signal leads. The unit is now ready for
operation.