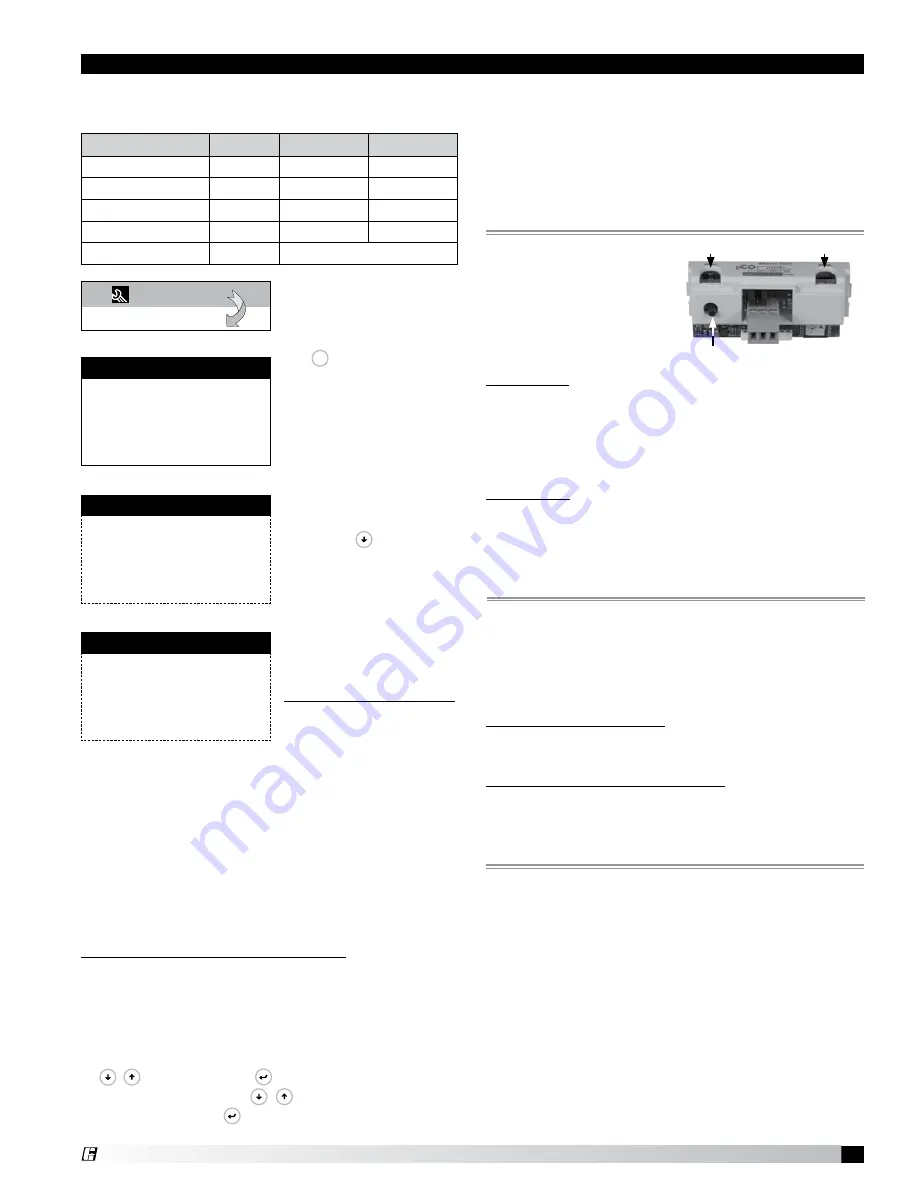
Parameter
Factory
Minimum
Maximum
Device Instance
77000
0
4194303
Station Address
0
0
127
Max Master
127
0
127
Max Info Frames
20
0
255
Baudrate
38400
9600-19200-38400-76800
4. Once desired parameters have been entered, go
to BACnet Read/Write screen. Change
Function
to
Write
and
Update?
to
YES
.
5. Reboot the controller by cycling power to the unit.
Allow several minutes for the controller to initialize.
6. View MSTP parameters. If changed values did not
save, contact the factory.
The communication card
is located in the
Serial
Card
port on the face of
the controller. The card
includes two sets of LED
lights for communication
troubleshooting.
Status LED:
Indicates the status of communication
between the card and controller.
• Quick green-off-green if communication with
controller is ok.
• Slow red-off-red if communication is not
established.
RS485 LED:
Indicates the status of communication
with the BACnet MSTP network. Wait for 40 seconds
to determine status of communication.
• Green with occasional red, communication is OK.
• Green and red both on, communications is not
established.
Communication Troubleshooting
See Carel Data sheet for more info.
If attempting to communicate with the controller over
BACnet MSTP, refer to the card LEDs for system
information.
Status LED slow red blink
• Confirm card is firmly plugged in.
• Confirm BMS Protocol is set to BACnet MSTP.
RS485 LED green and red both on
• Confirm system and card baudrate are the same.
• Confirm card Max Master is equal to or greater
than the Station (MAC) Address of the Master with
the highest address.
Recalling Factory Parameters
Follow this procedure to revert to factory parameters
for one power cycle. When restarted, the card will
resume using the previous user parameters.
1. With controller off, hold the push button located
on the BACnet MSTP card, while powering the
controller back on.
2. Continue to hold the button, while watching the
Status LEDs
. Wait for the Status LEDs to blink red
slowly, and release before the third slow flash.
3. Wait for about one minute for the factory
parameters to be loaded.
To view the current
parameters, go the
BMS
Config
menu within the
controller by pressing
the
Prg
Esc
key.
To access the
BMS
Config
sub-menu, enter
the service-password
(Default=1000).
Protocol
must be
BACnet MSTP
and
BACnet Plugin
must be
YES
.
Press the
Prg
Esc
button
arrow to view next
screen.
Current BACnet MSTP
parameters should be
displayed. If values
appear to be zero, follow
the procedure below.
To read current settings:
1. Power on controller
and allow several
minutes to initialize.
2. Go to
BMS Config
menu and view BACnet Read/
Write screen.
3. Change
Function
to
Read
and
Update
? to
YES
.
Current BACnet MSTP parameters should now be
displayed in the BACnet MSTP SETUP screen. If
all values appear to be zeros, consult the factory.
(Make sure you have allowed several minutes for the
controller to initialize).
*Values may appear to be zero
prior to setting the Function to READ.
To change BACnet MSTP parameters:
1. Power on the controller and allow several minutes
to initialize.
2. Go to
BMS Config
menu and view MSTP SETUP
screen.
3. Move cursor to desired parameter by pressing the
Prg
Esc
Prg
Esc
buttons. Press
Prg
Esc
to select the parameter
to change. Press the
Prg
Esc
Prg
Esc
buttons to adjust the
parameter. Press
Prg
Esc
to save adjusted value.
The card is loaded with the following default BACnet
MSTP parameters.
BACnet MSTP Quick Start
BMS Configuration
Protocol:
BACnet MSTP
BACnet Plugin?
YES
MSTP SETUP
Instance: 77000
Baudrate 38400
MAC Addr:
0
MaxMasters: 127
MaxInfoFrames: 20
BACnet Read/Write
Function: Read
Update? Yes
*Cycle unit power to confirm
write command.
G.
Service
c. BMS Config
Push Button
Status LED
RS485 LED
29
DDC Controller for Tempered Air Products
®