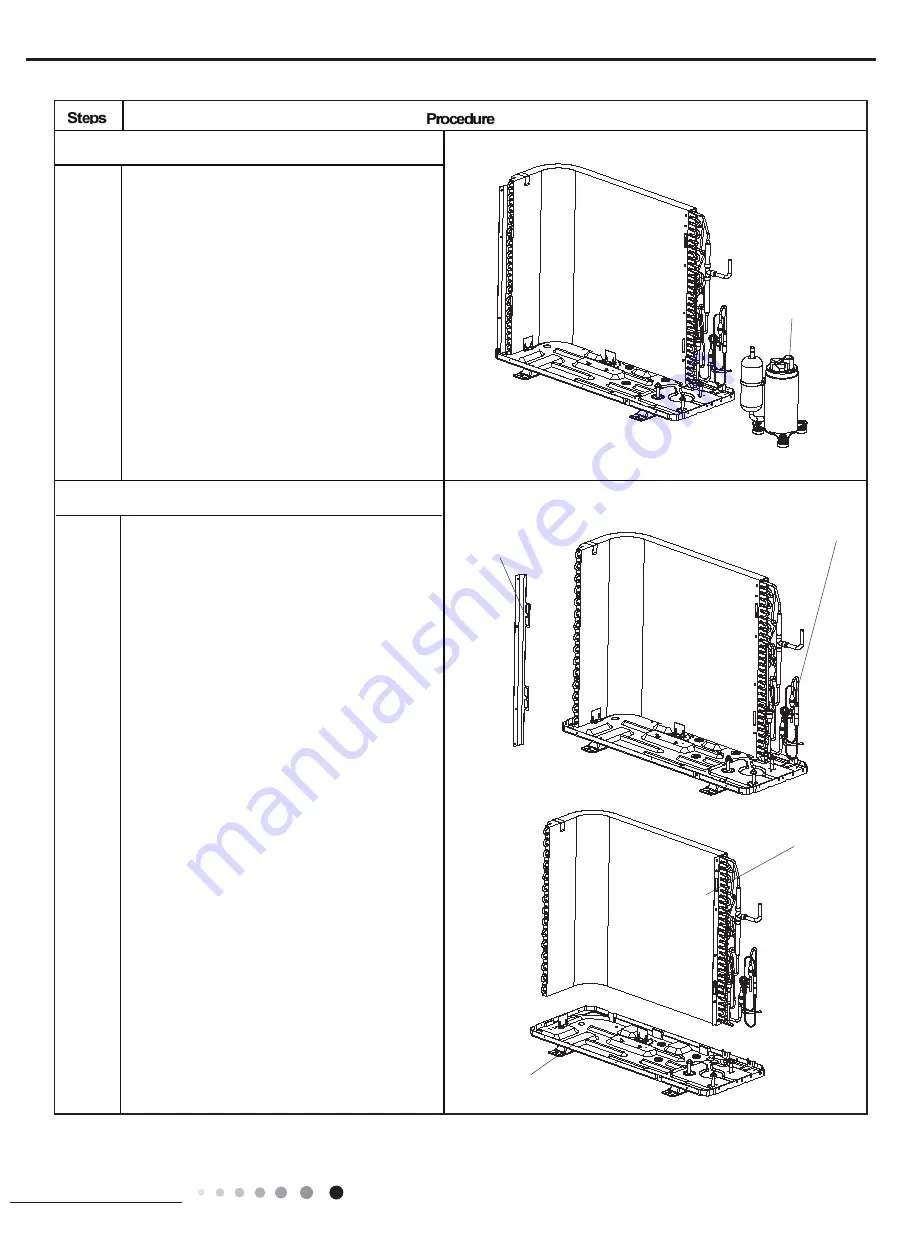
73
Installation and Maintenance
Service Manual
Remove the 3 foot nuts fixing the compressor
and then remove the compressor.
Remove the screws connecting the support
(condenser) and condenser assy,and then
remove the support(condenser).
9. Remov e compressor
compressor
10.Remove condenser sub-assy
a
support
capillary sub-assy
b
Remove the chassis sub-assy and condenser
sub-assy.
condenser sub-assy
chassis sub-assy