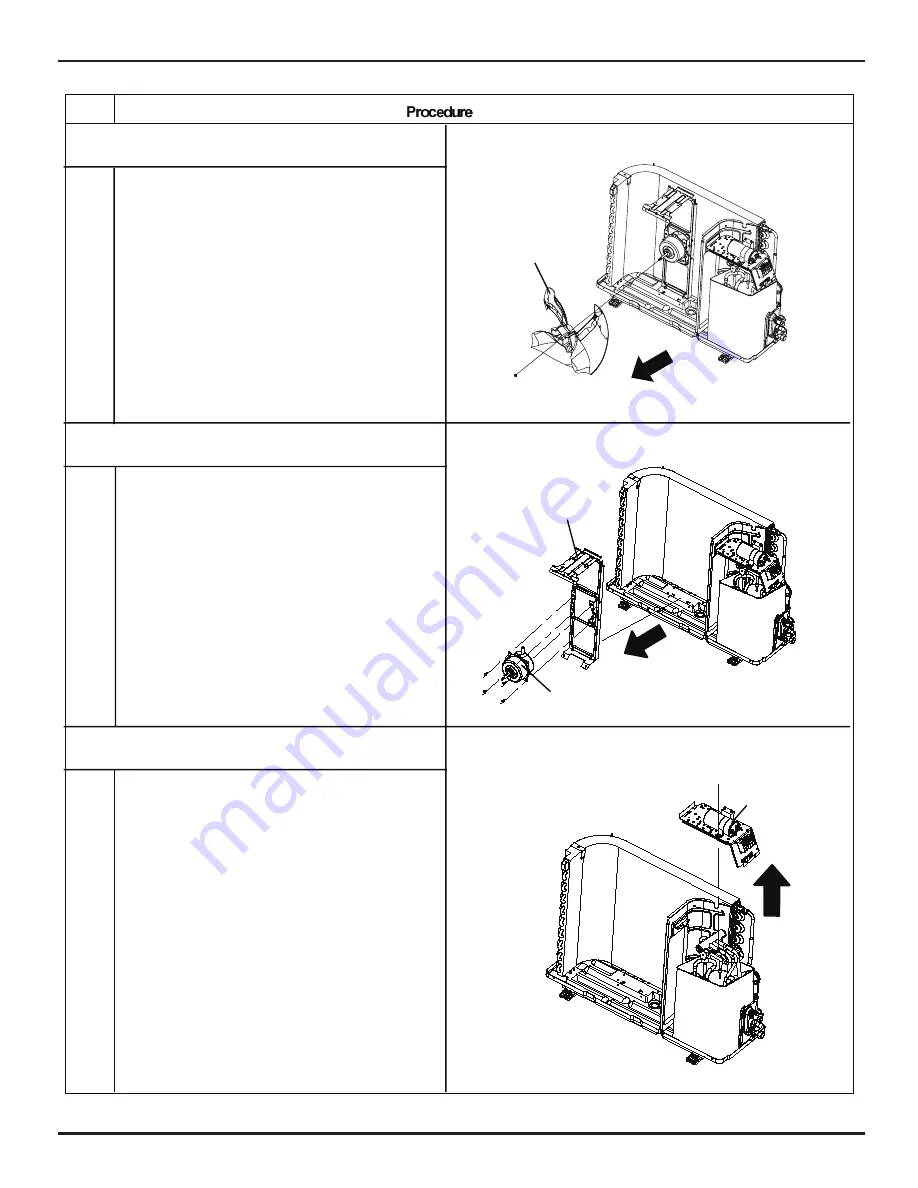
Removal Procedure
57
7. Remove axial flow blade
Remove the nut on the blade and then remove the
axial flow blade.
8. Remove motor and motor support
Remove the 4 tapping screws fixing the motor and
disconnect the leading wire insert of the motor.
Then remove the motor.
Remove the 2 tapping screws fixing the motor
support and lift the motor support to remove it.
9. Remove electric box
Remove screws fixing the electric box subassembly;
loosen the wire bundle and unplug the wiring
terminals. Then lift the electric box to remove it.
motor
motor support
electric box
axial flow blade
Steps