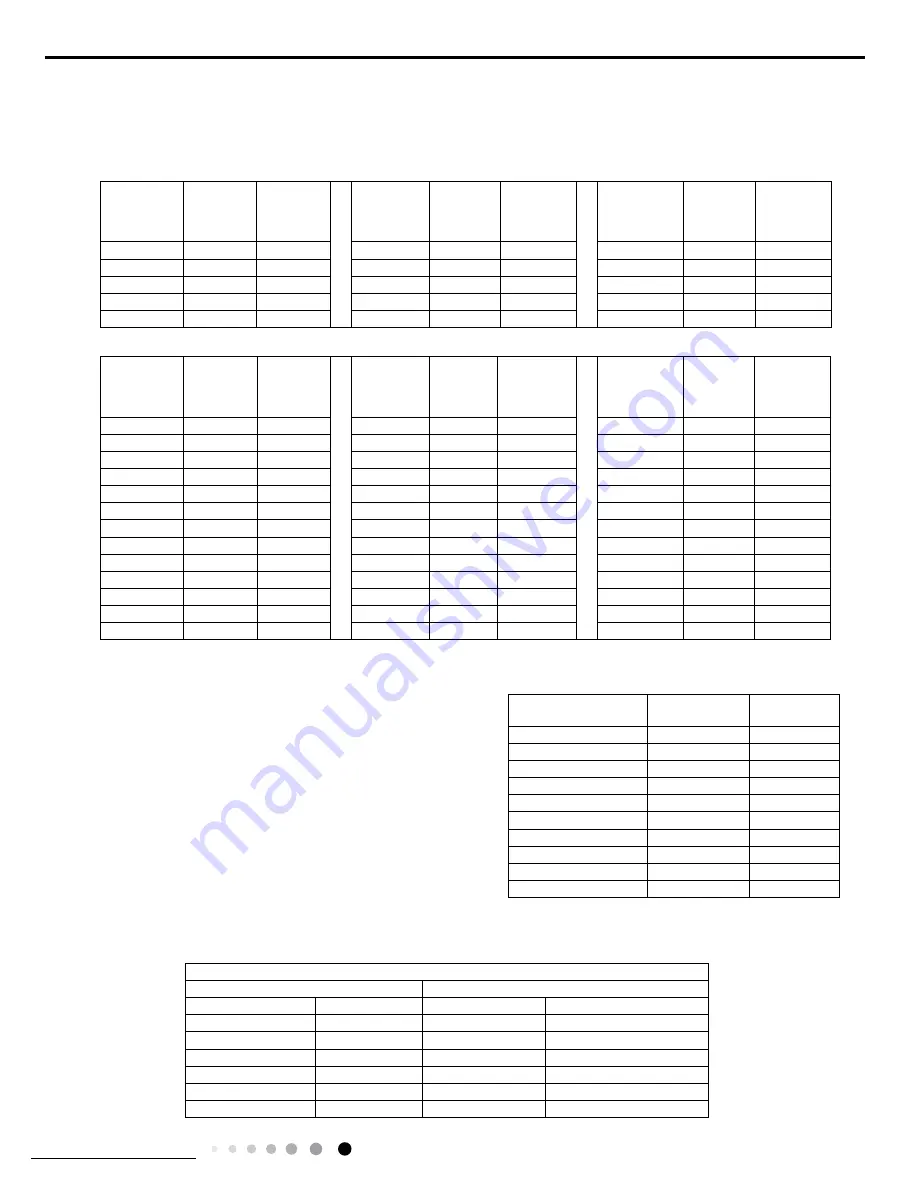
89
Installation and Maintenance
Service Manual
Appendix:
1.Standard length of connection pipe
● 5m, 7.5m, 8m.
2.Min. length of connection pipe is 3m.
3.Max. length of connection pipe and max. high difference.
4.The additional refrigerant oil and refrigerant charging required after
prolonging connection pipe
● After the length of connection pipe is prolonged for 10m at the basis
of standard length, you should add 5ml of refrigerant oil for each
additional 5m of connection pipe.
● The calculation method of additional refrigerant charging amount (on
the basis of liquid pipe):
Appendix 1: Reference Sheet of Celsius and Fahrenheit
Appendix 2: Configuration of Connection Pipe
Cooling capacity
Max length of
connection pipe
Max height
difference
5000 Btu/h(1465 W)
15 m
5 m
7000 Btu/h(2051 W)
15 m
5 m
9000 Btu/h(2637 W)
15 m
10 m
12000 Btu/h(3516 W)
20 m
10 m
18000 Btu/h(5274 W)
25 m
10 m
24000 Btu/h(7032 W)
25 m
10 m
28000 Btu/h(8204 W)
30 m
10 m
36000 Btu/h(10548 W)
30 m
20 m
42000 Btu/h(12306 W)
30 m
20 m
48000 Btu/h(14064 W)
30 m
20 m
Set temperature
Conversion formula for Fahrenheit degree and Celsius degree: Tf=Tcx1
.
8+32
Ambient temperature
Fahrenheit
display
temperature
(
o
F)
Fahrenheit
(
o
F)
Celsius
(
o
C)
Fahrenheit
display
temperature
(
o
F)
Fahrenheit
(
o
F)
Celsius
(
o
C)
Fahrenheit
display
temperature
(
o
F)
Fahrenheit
(
o
F)
Celsius
(
o
C)
32/33
32
0
55/56
55.4
13
79/80
78.8
26
34/35
33.8
1
57/58
57.2
14
81
80.6
27
36
35.6
2
59/60
59
15
82/83
82.4
28
37/38
37.4
3
61/62
60.8
16
84/85
84.2
29
39/40
39.2
4
63
62.6
17
86/87
86
30
41/42
41
5
64/65
64.4
18
88/89
87.8
31
43/44
42.8
6
66/67
66.2
19
90
89.6
32
45
44.6
7
68/69
68
20
91/92
91.4
33
46/47
46.4
8
70/71
69.8
21
93/94
93.2
34
48/49
48.2
9
72
71.6
22
95/96
95
35
50/51
50
10
73/74
73.4
23
97/98
96.8
36
52/53
51.8
11
75/76
75.2
24
99
98.6
37
54
53.6
12
77/78
77
25
Fahrenheit
display
temperature
(
o
F)
Fahrenheit
(
o
F)
Celsius
(
o
C)
Fahrenheit
display
temperature
(
o
F)
Fahrenheit
(
o
F)
Celsius
(
o
C)
Fahrenheit
display
temperature
(
o
F)
Fahrenheit
(
o
F)
Celsius
(
o
C)
61
60.8
16
69/70
69.8
21
78/79
78.8
26
62/63
62.6
17
71/72
71.6
22
80/81
80.6
27
64/65
64.4
18
73/74
73.4
23
82/83
82.4
28
66/67
66.2
19
75/76
75.2
24
84/85
84.2
29
68
68
20
77
77
25
86
86
30
Additional refrigerant charging amount for R22, R407C, R410A and R134a
Diameter of connection pipe
Outdoor unit throttle
Liquid pipe(mm)
Gas pipe(mm)
Cooling only(g/m)
Cooling and heating(g/m)
Ф6
Ф9.5 or Ф12
15
20
Ф6 or Ф9.5
Ф16 or Ф19
15
20
Ф12
Ф19 or Ф22.2
30
120
Ф16
Ф25.4 or Ф31.8
60
120
Ф19
/
250
250
Ф22.2
/
350
350
● When the length of connection pipe is above 5m, add refrigerant according to the prolonged length of liquid pipe. The additional
refrigerant charging amount per meter is different according to the diameter of liquid pipe. See the following sheet.
● Additional refrigerant charging amount = prolonged length of liquid pipe X additional refrigerant charging amount per meter