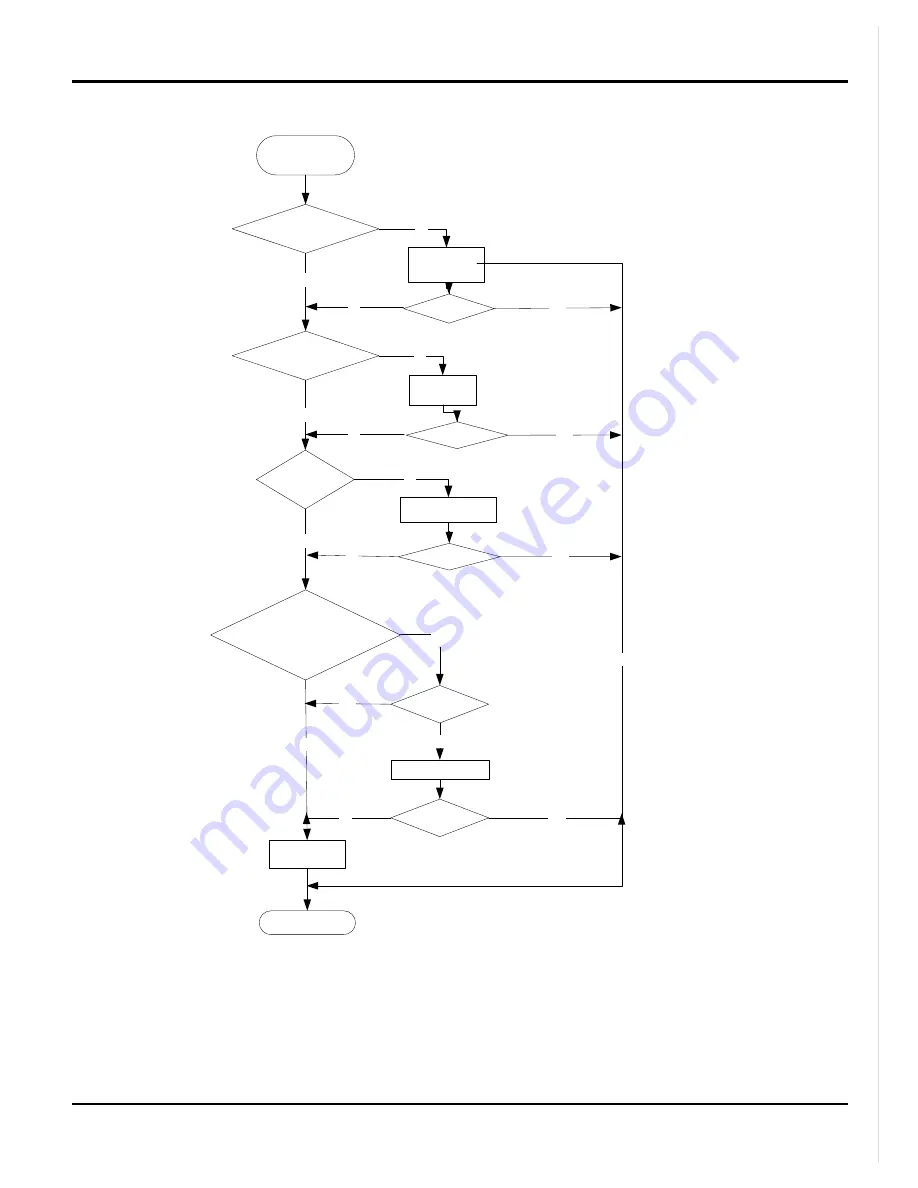
63
Troubleshooting
Start
Check whether the
feedback terminal of PG motor
is connected tightly
Check whether the
control end of PG motor
is connected tightly
Replace PG motor
End
yes
Replace the
control panel
Insert the feedback
terminal of PG
motor tightly
no
Eliminate the
malfunction
yes
no
Insert the control
end of PG motor
tightly
no
Eliminate the
malfunction
no
Pull the blade by
hand to see whether
the blade can rotate
smoothly
Re-assemble the blade
and motor correctly
Eliminate the
malfunction
no
no
yes
yes
Turn on the unit
after re-energization, measure whether
the output voltage on control end for PG
motor is more than 50V
no
yes
yes
Whether the motor
is started up
no
Eliminate the
malfunction
yes
yes
yes
no
yes
(2) PG motor (indoor fan) does not operate (H6)