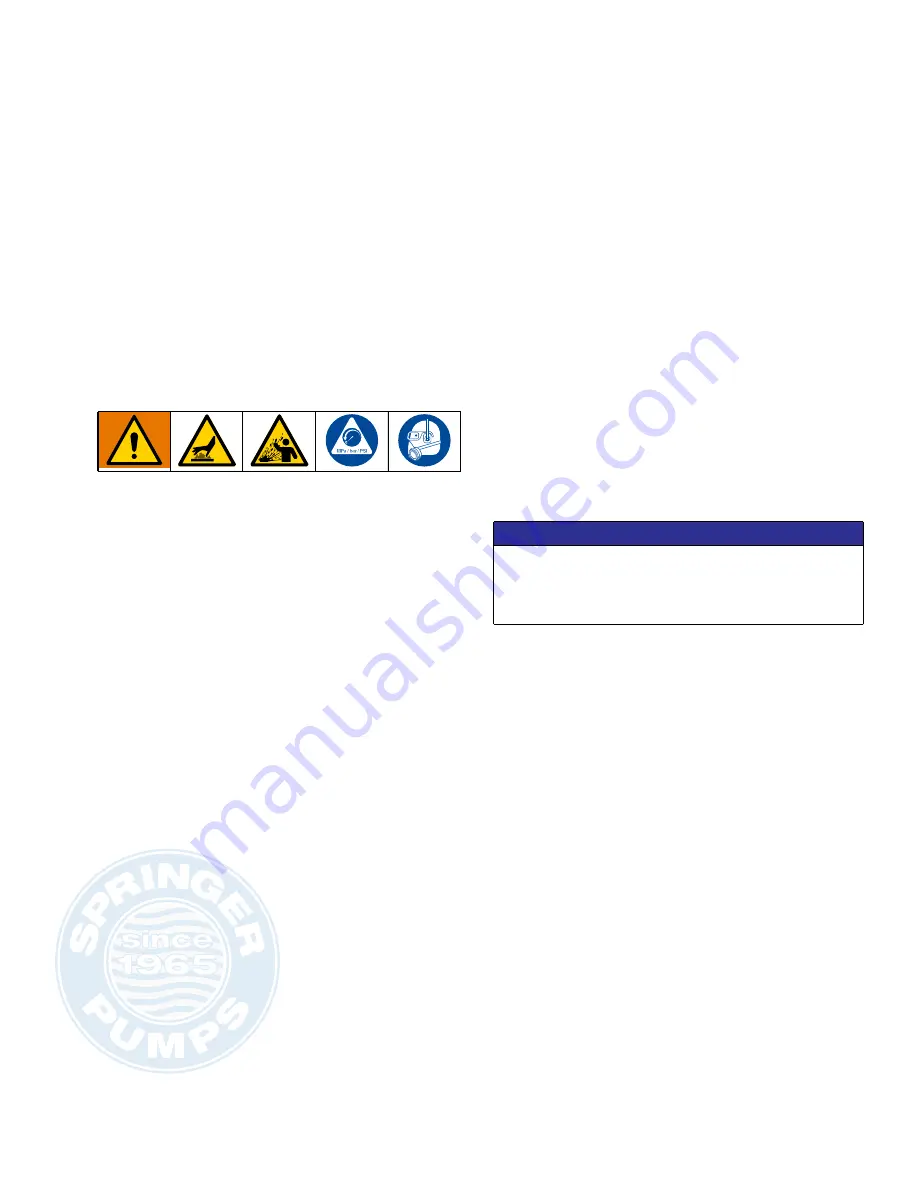
Repair
18
3A8693B
Diaphragm Repair
Tools Required:
•
Torque wrench
•
10 mm socket wrench
•
15 mm socket wrench
•
19 mm open-end wrench
•
O-ring pick
•
Lithium-base grease, part no. 111920 (Lubriplate
630AA or equivalent)
Service the diaphragms as follows.
See
F
IG
Disassemble Diaphragms
1.
Perform the Pressure Relief Procedure, page 12.
2.
Disconnect all air and fluid lines from the equipment.
3.
Perform Disassemble Check Valves, page 16.
4.
Remove screws (106, 120) from fluid covers (101).
Remove fluid covers from air covers (23).
5.
Use an applicable wrench to loosen the diaphragm
shaft bolts (107). Do not remove bolt.
6.
Remove one diaphragm assembly (401). See F
7.
Remove the other diaphragm assembly (401) with
the shaft (24).
8.
Disassemble the diaphragm plates (104, 105),
diaphragms (401), packing o-rings (108), and bolt
(107).
9.
Clean and inspect all parts for wear or damage.
Replace as needed.
Reassemble Diaphragms
1.
Assemble the diaphragm plates (104, 105), packing
o-ring (108), and diaphragm (401) onto the
diaphragm shaft bolt (107). See F
NOTE: Install diaphragms (401) with the side
marked AIR SIDE facing toward the center housing
(1). See F
2.
Screw the diaphragm assembly onto one side of the
shaft (24). Torque to 28–33 in-lb (3.2–3.7 N
m).
3.
Grease the length of the shaft (24) and slide through
the center housing (1).
4.
Repeat steps 1–2 for the other diaphragm
assembly.
5.
Apply medium-strength (blue) thread locker to the
threads of the fluid cover screws (106, 120).
6.
Align fluid covers (101) with center housing (1) and
insert fluid cover screws (106, 120). Torque to 40–
45
ft-lb
(54.2–61 N•m) at 100 rpm maximum. See
7.
Perform Reassemble Check Valves, page 16.
8.
Reconnect air and fluid lines to equipment.
NOTICE
After reassembly, allow the thread locker to cure for
12 hours, or per manufacturer’s instructions, prior to
operating the equipment. Damage to the equipment
will occur if the diaphragm shaft bolt loosens.
Tel: 866-777-6060
Fax: 866-777-6383
Springer Pumps, LLC
Website: www.springerpumps.com
Int'l: +001 267 404 2910