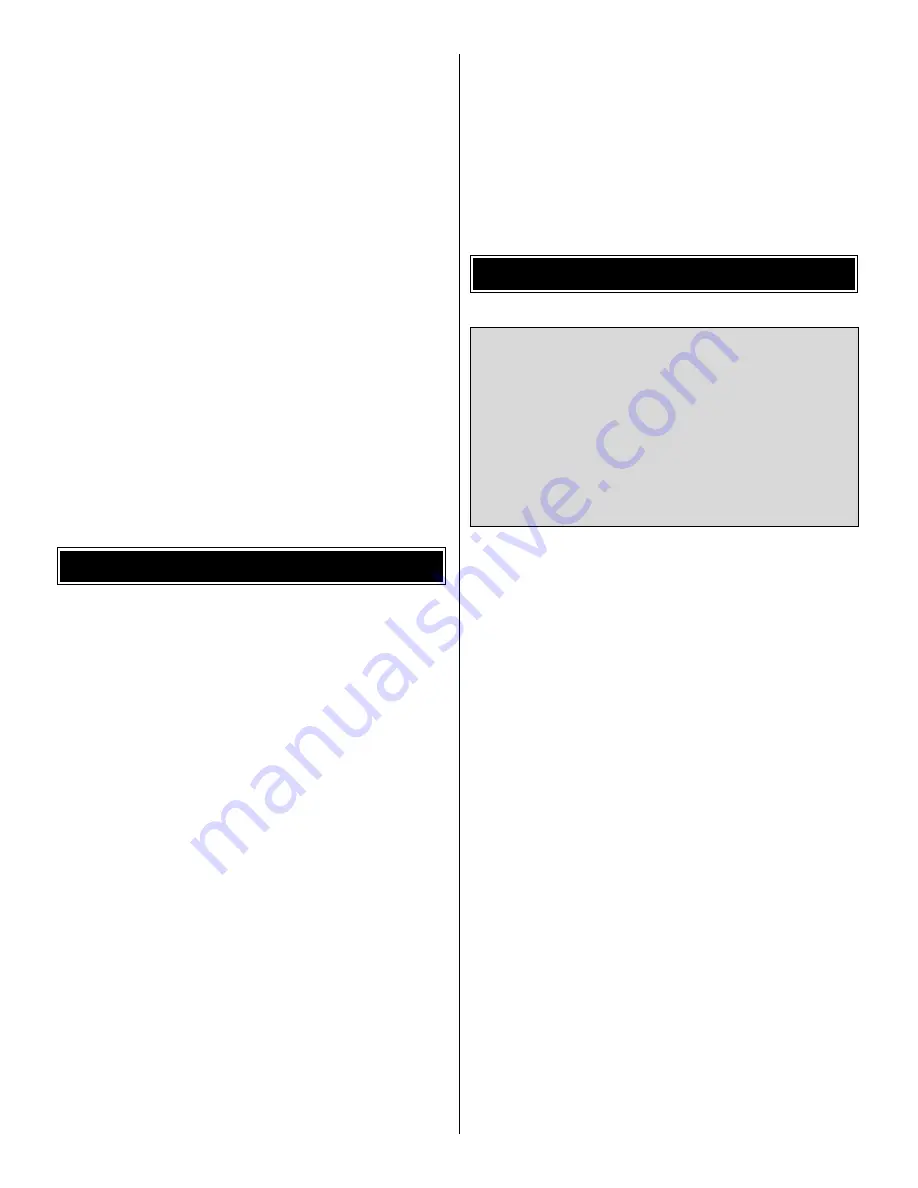
Keep your face and body as well as all spectators away from
the plane of rotation of the propeller as you start and run
the engine.
Keep these items away from the prop: loose clothing, shirt
sleeves, ties, scarves, long hair or loose objects such as
pencils or screwdrivers that may fall out of shirt or jacket
pockets into the prop.
Use a “chicken stick” or electric starter to start the engine.
Do not use your fingers to flip the propeller. Make certain the
glow plug clip or connector is secure so that it will not pop
off or otherwise get into the rotating propeller.
Make all engine adjustments from behind the rotating
propeller.
The engines get hot! Do not touch them during or right after
operation. Make sure fuel lines are in good condition so fuel
will not leak onto a hot engine, causing a fire.
To stop a glow engine, cut off the fuel supply by closing off
the fuel line, if your transmitter has an engine cut switch, set
it to fully close the carburetor barrel, or follow the engine
manufacturer’s recommendations. Do not use hands,
fingers or any other body part to try to stop the engine. Do
not throw anything into the propeller of a running engine.
Read and abide by the following Academy of Model
Aeronautics Official Safety Code:
GENERAL
1. I will not fly my model aircraft in sanctioned events, air
shows, or model flying demonstrations until it has been
proven to be airworthy by having been previously
successfully flight tested.
2. I will not fly my model aircraft higher than approximately
400 feet within 3 miles of an airport without notifying the
airport operator. I will give right of way to, and avoid flying in
the proximity of full-scale aircraft. Where necessary an
observer shall be used to supervise flying to avoid having
models fly in the proximity of full-scale aircraft.
3. Where established, I will abide by the safety rules for the
flying site I use, and I will not willfully and deliberately fly my
models in a careless, reckless and/or dangerous manner.
7. I will not fly my model unless it is identified with my name
and address or AMA number, on or in the model.
9. I will not operate models with pyrotechnics (any device
that explodes, burns, or propels a projectile of any kind).
RADIO CONTROL
1. I will have completed a successful radio equipment ground
check before the first flight of a new or repaired model.
2. I will not fly my model aircraft in the presence of
spectators until I become a qualified flier, unless assisted by
an experienced helper.
3. I will perform my initial turn after takeoff away from the pit
or spectator areas, and I will not thereafter fly over pit or
spectator areas, unless beyond my control.
4. I will operate my model using only radio control
frequencies currently allowed by the Federal Communications
Commission.
❏
1.
Fuelproof all areas exposed to fuel or exhaust
residue such as the engine mounts.
❏
2.
Check the C.G. according to the measurements
provided in the manual.
❏
3
Be certain the battery and receiver are securely
mounted in the canopy. Simply stuffing them into
place with foam rubber is not sufficient.
❏
4.
Extend your receiver antenna and make sure it has
a strain relief inside the canopy to keep tension off
the solder joint inside the receiver.
❏
5.
Balance your model
laterally as explained in the
instructions.
❏
6.
Use thread locking compound to secure critical
fasteners such as the set screws that hold the
wheel collars, screws that hold the carburetor arm
(if applicable), engine mounting screws, throttle
linkage, etc.
❏
7.
Add a drop of oil to the axles so the wheels will turn freely.
❏
8.
Make sure all hinges are securely glued in place.
❏
9.
Reinforce holes for wood screws with thin CA where
appropriate (servo mounting screws, canopy mounting
screws, etc.).
❏
10.
Confirm that all controls operate in the correct direction
and the throws are set up according to the manual.
❏
11. Make sure there are silicone retainers on all the
clevises and that all servo arms are secured to the
servos with the screws included with your radio.
❏
12. Secure connections between servo wires and
Y-connectors or servo extensions, and the
connection between your battery pack and the
on/off switch with vinyl tape, heat shrink tubing or
special clips suitable for that purpose.
During the last few moments of preparation your mind
may be elsewhere anticipating the excitement of the first
flight. Because of this, you may be more likely to overlook
certain checks and procedures that should be performed
before the model is flown. To help avoid this, a check list
is provided to make sure these important areas are not
overlooked. Many are covered in the instruction manual,
so where appropriate, refer to the manual for complete
instructions. Be sure to check the items off as they are
completed (that’s why it’s called a
check list!).
CHECK LIST
AMA SAFETY CODE (excerpt)
44
Summary of Contents for Profile 38
Page 7: ...7 DIE CUT DRAWINGS ...
Page 48: ...TWO VIEW DRAWING Use copies of this page to plan your trim scheme ...
Page 49: ...C B ...
Page 50: ...D A ...