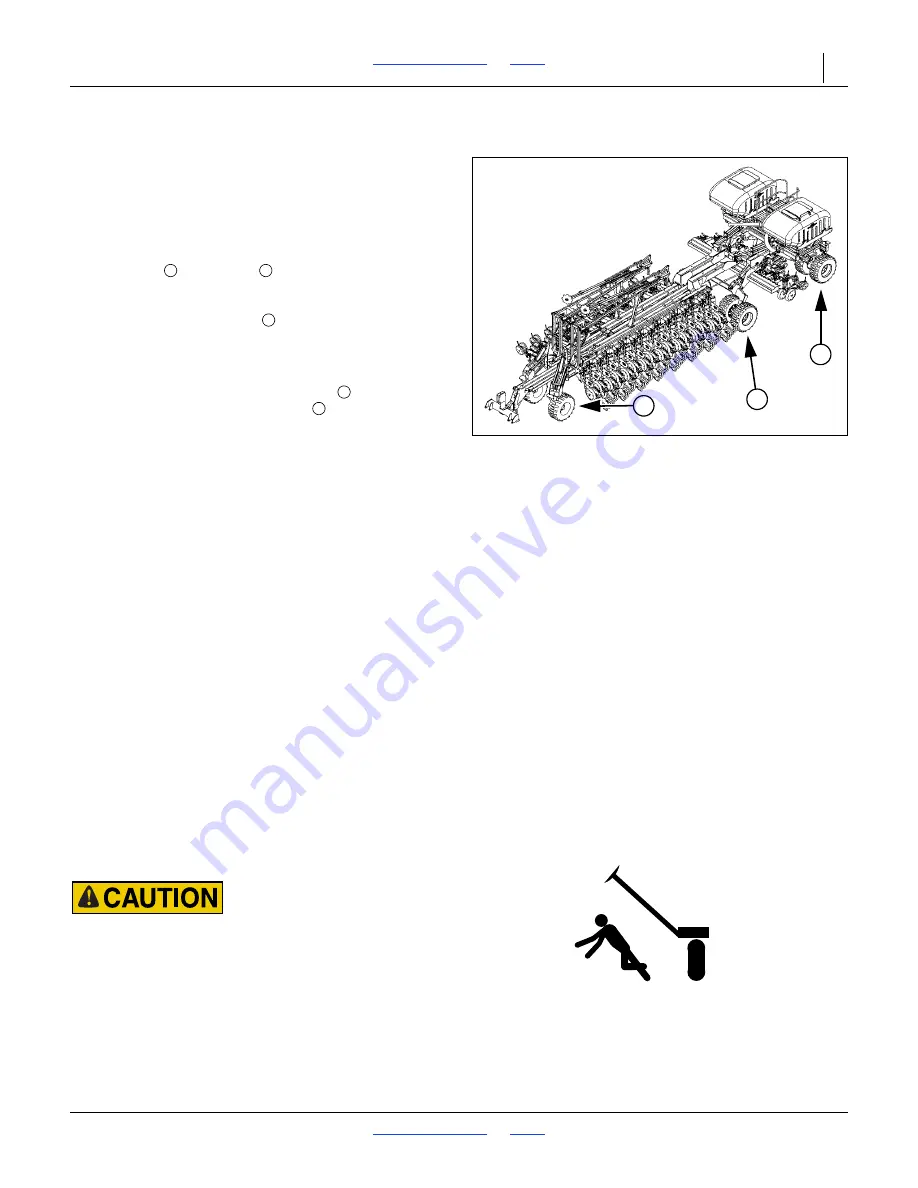
YP2425 and YP2425F
Adjustments
53
2016-11-16
401-406M
Gauge/Transport Wheel Adjustments
The gauge/transport wheels serve two functions:
1.
When the planter is lowered, the wheels establish
the heights of their respective sections, nominally a
tool bar height of 26 inches (66 cm) above the
planting surface.
The main
and trailing
wheels are not adjustable
in height.
The wing gauge wheels
may be slightly raised or
lowered by adjusting a nut on the cylinder rod. See
“
2.
When the planter is raised, all of these are the
transport wheels. The main wheels
are rigid, and
aid steering. The trailing wheels
are full castering.
The gauge wheels are usually adjusted only to bring all
sections to level.
Marker Adjustments
There are six adjustments for markers:
•
Disk Angle
Even if your row spacing rarely changes, you may
need to adjust disk angle for soil conditions and
planting speed.
•
Marker Extension
Once set for a specific row spacing, this only needs
periodic checking to ensure the clamp is secure.
•
Marker Support Wheels
Three bolt holes are available for adjusting height.
•
Shear Bolt Replacement
If a marker hangs up on an obstruction, a bolt at the
fold is designed to fail.
•
Chain Length
This needs to be set if the chain is replaced. It may
also need adjustment for unusual terrain.
•
Marker Speed
Once initially set by your dealer, this rarely needs
modification.
Sharp Overhead Object Hazard:
You may be injured if hit by a folding or unfolding marker.
Markers may fall quickly and unexpectedly if the hydraulics
fail. Never allow anyone near the planter when folding or
unfolding the markers.
Figure 58
Gauge Wheels
25205
3
1
2
Summary of Contents for YP2425
Page 2: ...Table of Contents Index Table of Contents Index...
Page 164: ...2016 11 16 Table of Contents Index 401 406M YP2425 and YP2425F Table of Contents Index 160...
Page 165: ...Table of Contents Index Table of Contents Index...
Page 166: ...Great Plains Mfg 1525 E North St P O Box 5060 Salina KS 67402...