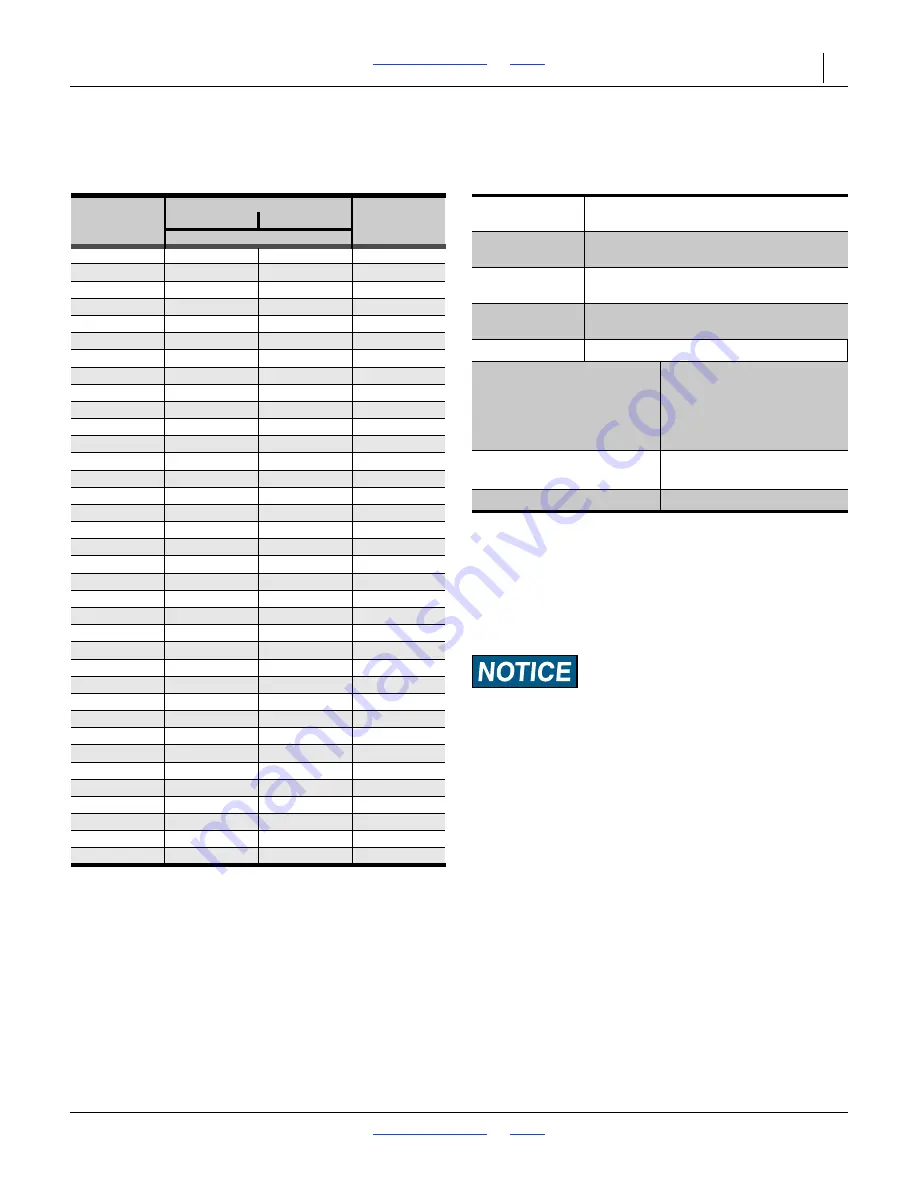
2018-10-10
407-313M
NP30L or NP40L
Adjustments
84
Nutri-Pro
®
NP40L-15R30 Fertilizer Rate
Use the slide chart or internet calculator for more precise
rate setting.
NP40L-15R30 JohnBlue Reference Data
Use the data below with the CDS-John Blue 115797-01
slide chart or with the CDS-John Blue internet calculator.
Equipment Damage Risk:
Plant at or below 9 mph (14.4 kph) with the 47T Driving
sprocket installed. The pump is rated for 450 rpm maximum,
which is exceeded at and above 9 mph (14.4 kph).
Drivin
g
S
procket
15
47
Dial
S
ettin
g
4
2.5
3
7
5
3
.1
47
6
3
.7
56
7
4.4
65
8
5.0
75
9
5.6
8
4
10
6.2
2.0
94
11
6.9
2.2
10
3
12
7.5
2.4
112
1
3
8
.1
2.6
122
14
8
.7
2.
8
1
3
1
15
9.4
3
.0
140
16
10.0
3
.2
150
17
3
.4
159
1
8
3
.6
16
8
19
3
.
8
17
8
20
4.0
1
8
7
21
4.2
196
22
4.4
206
2
3
4.6
215
24
4.
8
224
25
5.0
2
3
4
26
5.2
24
3
27
5.4
25
3
2
8
5.6
262
29
5.
8
271
3
0
6.0
2
8
1
3
1
6.2
290
3
2
6.4
299
33
6.6
3
09
3
4
6.
8
3
1
8
3
5
7.0
3
27
3
6
7.2
33
7
3
7
7.4
3
46
38
7.6
3
55
3
9
7.
8
3
65
3
1657d
Gallon
s
per
Acre
Liter
s
per
Hectare
Pump Type
(•) Piston Pump
NGP-7050 Series
Data
Preference
(•) <user-specified>
Application
Rate
<user-specified>
Drive
System
(•) Ground Drive
Loaded Radius: 17.55 in. (44.58 cm)
Swath Width
450 inches (1143 cm)
Drive
(Required):
(Optional):
(Optional):
(Optional):
25
15 or 47
__
__
Driven
(Required):
(Optional):
(Optional):
(Optional):
15
15
__
__
Sprocket Ratio
(for slide chart)
Driving 15T:
Driving 47T:
1.67
a
5.22
b
a. For easier scale readings (but same net ratio), use:
Loaded Radius: 20
Sprocket Ratio: 1.9
b. For easier scale readings (but same net ratio), use:
Loaded Radius: 10
Sprocket Ratio: 3.0
Ground Speed
5 mph
c
/ 8 kph
c. Gallons per acre is independent of speed between 2 mph
and 9 mph (3-14 kph). See advisory below.
Summary of Contents for Nutri-Pro NP30L
Page 2: ...Table of Contents Index Table of Contents Index ...
Page 154: ...NP30L or NP40L Cover Table of Contents 150 2018 10 10 Cover Table of Contents 407 313M ...
Page 155: ...Table of Contents Index Table of Contents Index ...
Page 156: ...Great Plains Mfg 1525 E North St P O Box 5060 Salina KS 67402 ...