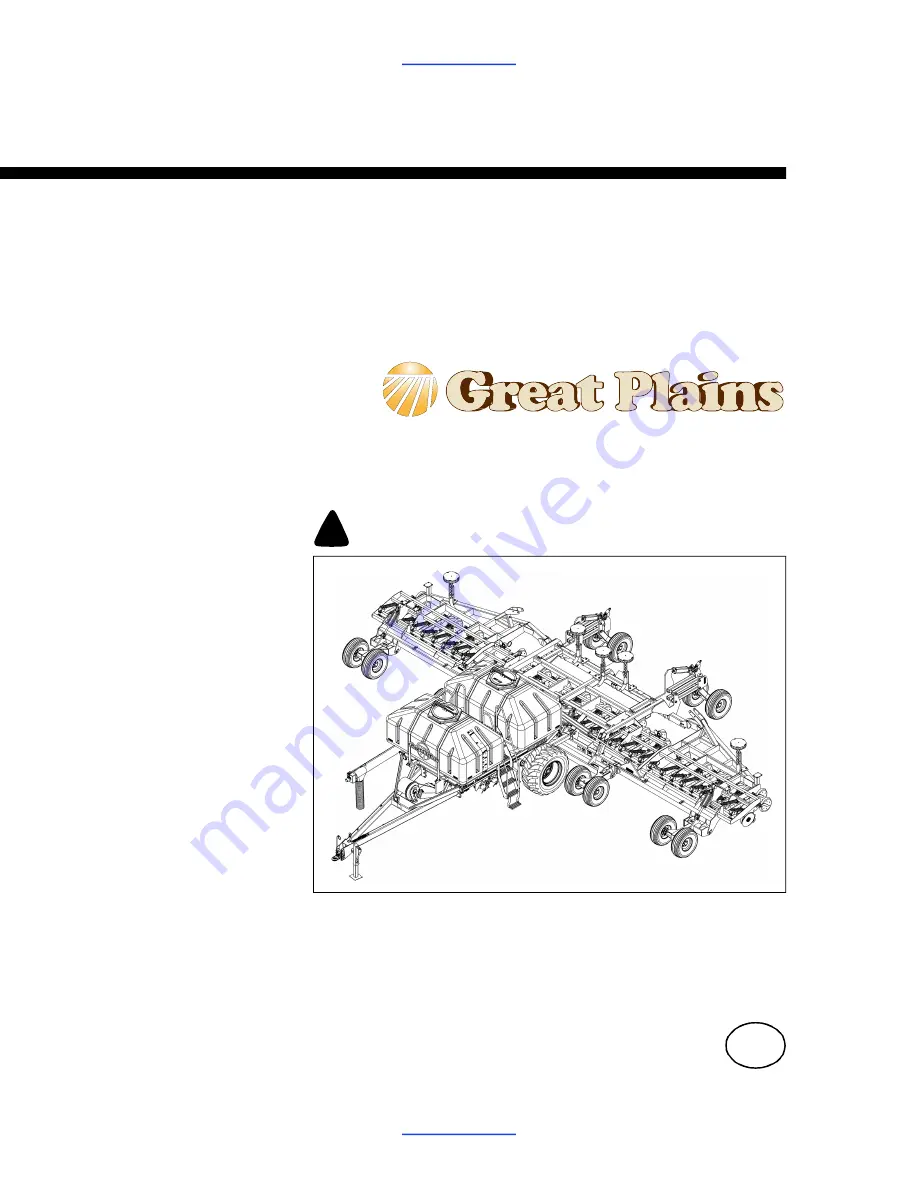
Manufacturing, Inc.
www.greatplainsmfg.com
© Copyright 2022
Printed 04/14/2022
160-220M
EN
ORIGINAL INSTRUCTIONS
Pre-Delivery Manual
NTA3010, NTA3510 and ADC
No-Till Air Drill
and Air Drill Cart
Read the pre-delivery manual entirely. When you see this symbol, the
subsequent instructions and warnings are serious
-
follow without exception.
Your life and the lives of others depend on it!
Cover illustration may show optional equipment not supplied with standard
units.
!
28450