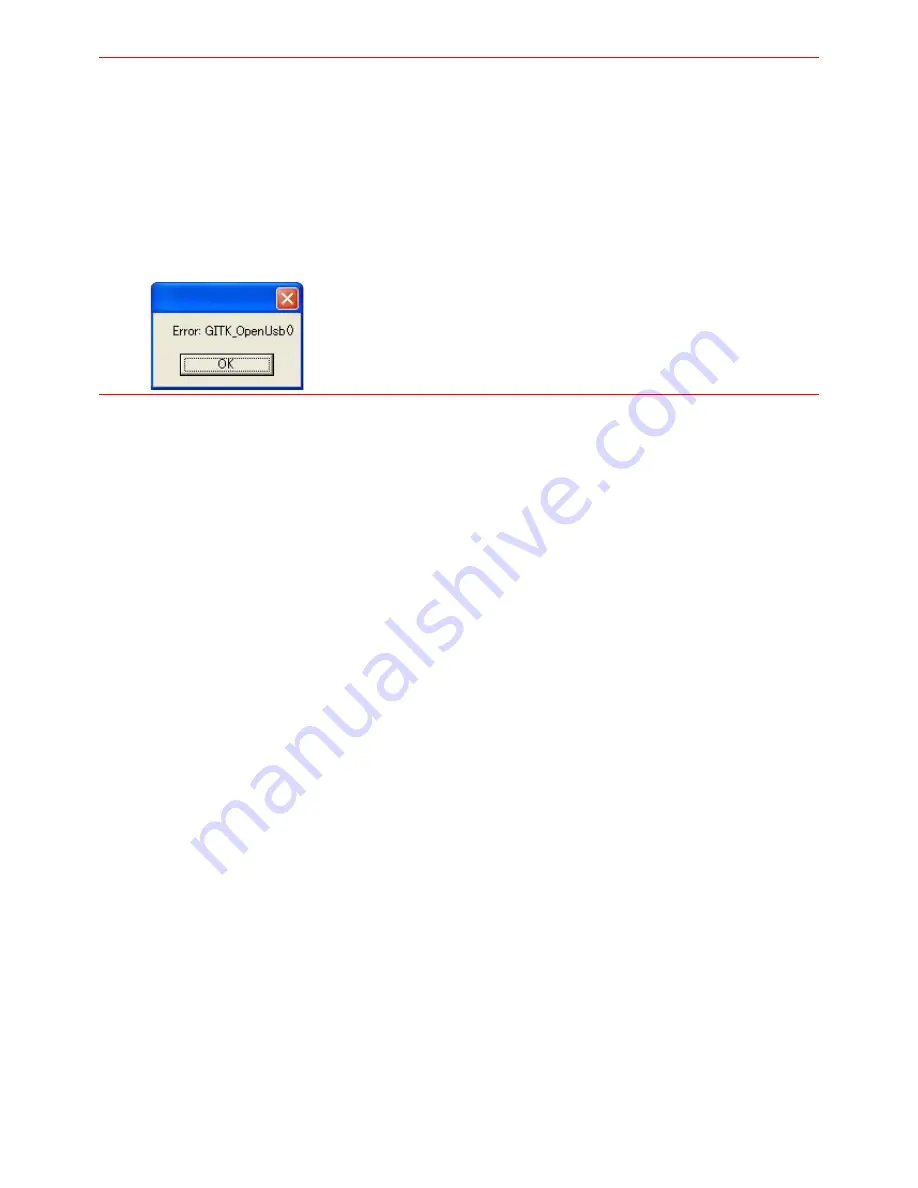
5-5
5 ELECTRICAL ADJUSTMENTS
CC100-UM-251-9370
Note 1: Do not turn off the standby switch while adjusting the CC100-20. If you do so, the CC100-20 will not
receive any commands from the adjustment software. If you turn off the standby switch while adjusting the
CC100-20, perform the following procedure.
(1) Click the Cancel button to exit the adjustment software.
(2) Connect the power cable to the CC100-20.
(3) Turn on the standby switch of the CC100-20.
(4) Execute OptionSetEnglish.exe again.
Note 2: The OptionSetEnglish.exe software will not start if the standby switch is off or the power is off. The
OptionSetEnglish.exe software displays the menu shown below at this time.