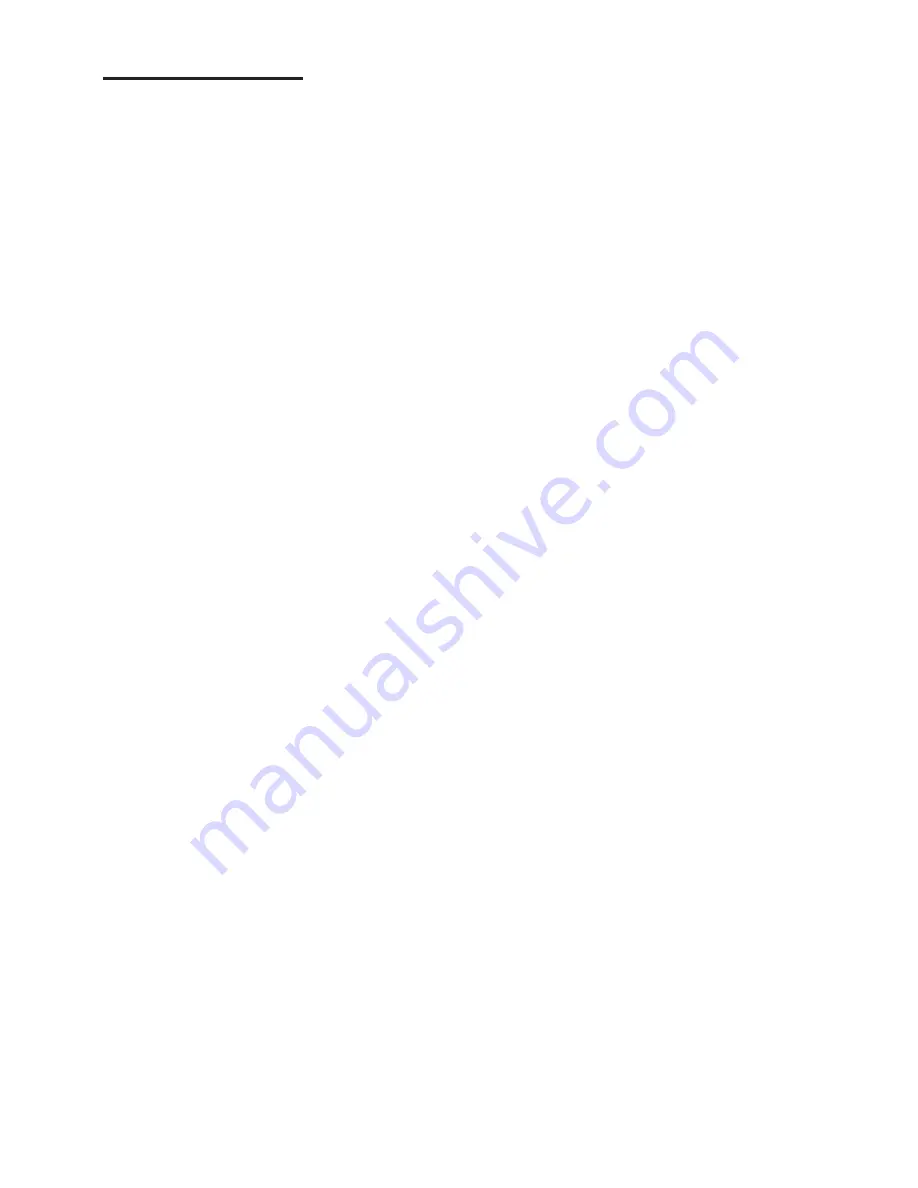
1. Technical data
6
Weight
.................................................................... 685 kg filled machine
Tank volume
........................................................ 165 litres
Granule amount
................................................ 16 kg
Wash power
......................................................... 10 % granule concentration
Wash water temperature
............................. 65 °C
Rinse water temperature
.............................. 85 °C
Rinse water volume
......................................... 14 litres/wash programme. To obtain 3600 HUE according to ANSI/NSF
(3, 2001), 14 litres is necessary. In other cases the volume can be reduced to 5 litres.
Wash programmes
........................................... short 2 min 40 s., normal 4 min 40 s., long 6 min 40 s.
Programmes without granules are 1 minute shorter.
Time for steam reduction
............................. 1 minute
Models
.................................................................... GD 900 Compact with pull-out cassette,
GD 900 Flow System with 1 trolley and 2 removable cassettes
GD 900 Freeflow System with 2 trolleys and 2 removable cassettes
Loading volume
.................................................. 450 litres
Capacity
................................................................. 8 GN 1/1, 200 mm deep containers, or 16 GN 1/2, 200 mm deep containers or
the equivalent in other items to be washed
Max capacity/h (washing with granules)
.... GD 900 Compact/ Flow System/ Freeflow System
115/ 122/ 144 GN 1/1
Normal capacity/h (washing with granules)
.. 78/ 81/ 90 GN 1/1
Voltage**
............................................................... 400 V (normal), 3-phase, earth,
230, 415, 440 and 575 V (option), 3-phase, earth
Fuse**
..................................................................... 400 V: 40 A, 25 A for steam model
415 V: 40 A, 20 A for steam model
440 V: 40 A, 20 A for steam model
230 V: 63 A, 35 A for steam model
575 V: 25 A, 16 A for steam model
Frequency
............................................................. 50 Hz or 60 Hz
Maximum power
............................................... 21 kW
Wash tank heater element*
........................ 16 kW
Rinse tank heater element*
......................... 16 kW
Pump motors, x 2
.............................................. 2.2 kW/motor
Rinse pump
.......................................................... 0.37 kW
Encapsulation class
........................................... IP 55
Hot water
............................................................. 1/2” (DN15), 55 - 65 °C, 3-7 °dH,
Note: Reverse osmosis water and distilled water must not be used.
Water pressure / flow h.w.
............................ 1-6 bar with solenoid valve open / 28 litres/minute
Cold water
............................................................ 1/2” (DN15), 3-7 °dH (refers to steam reduction)
Water pressure / flow c.w.
............................ 1-6 bar with solenoid valve open / 15 litres/minute
Detergent and rinse agent
............................ 24 and 230 VAC signals are available in separate terminal box
Recommended ventilation capacity
........ Machine without steam reduction unit: 700 m³/h
Machine with steam reduction unit: 200 m³/h
Outflow
.................................................................. Pipe Ø32 mm
Drain
....................................................................... Required capacity 100 litres/minute.
The machine should not be placed directly over a drain.
* Not activated simultaneously.
** For specific data for this machine, please see rating plate.
• GD 900 can also be supplied for steam heating or cold water connection.
• The machine is supplied with a 2.5-metre long electrical cable which is connected to the main switch on the wall. The main
switch is not included in the delivery.
Summary of Contents for GD 900
Page 5: ...7 ...
Page 17: ...Notes ...