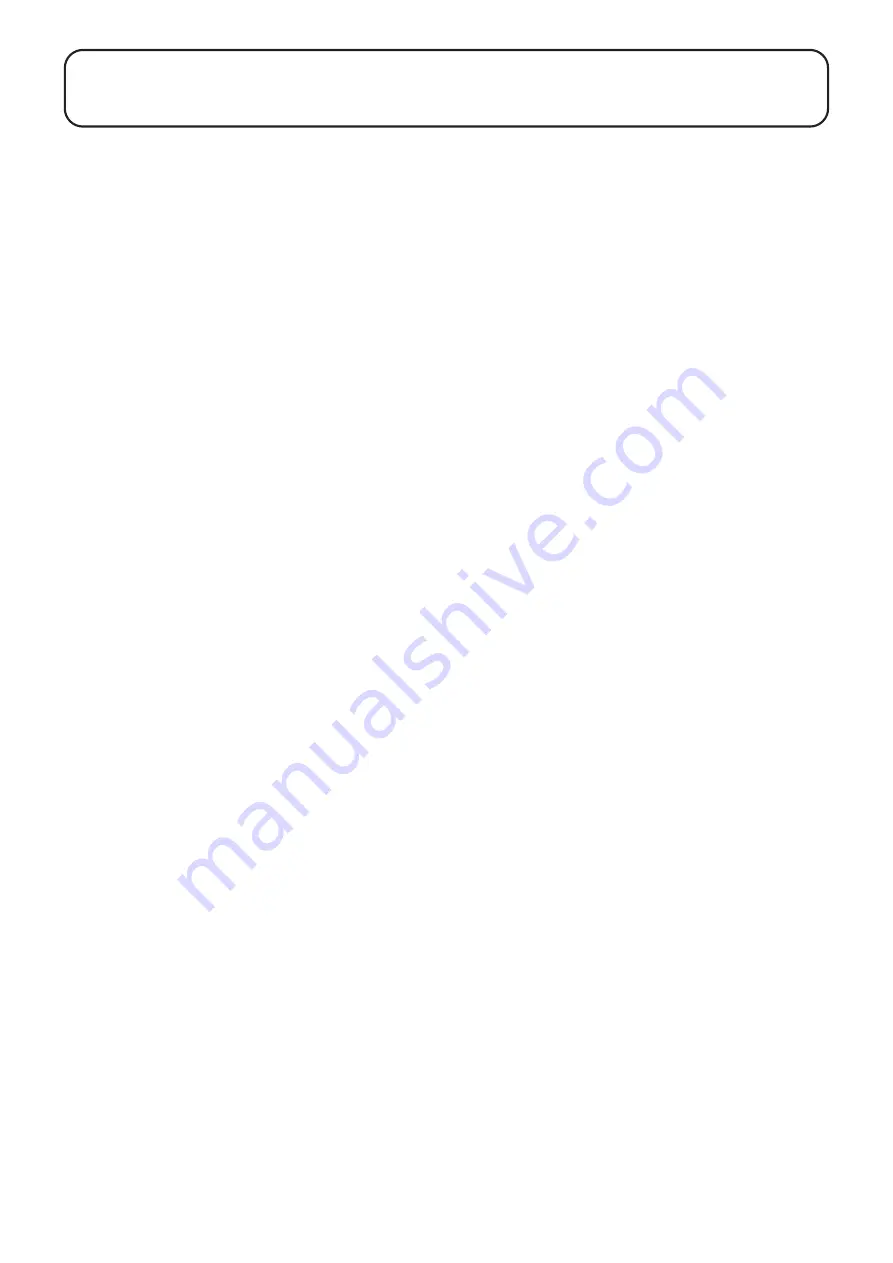
Page 31
Section 13: Guarantee
You are now the proud owner of a cylinder from Grant
Engineering (UK) Limited, which has been designed to give you
years of reliable, trouble free operation.
Grant Engineering (UK) Limited guarantees the manufacture of
the cylinder including all electrical and mechanical components
for a period of
twelve months from the date of installation
4
,
provided that the cylinder has been installed in full accordance
with the installation and servicing instructions issued.
This will be extended to a total period of
two years
if the cylinder
is registered with Grant Engineering (UK) Limited
within thirty
days of installation
4
and is serviced at twelve monthly intervals
3
.
See main Terms and Conditions below.
In addition, the stainless steel (shell) used in the manufacture of
the cylinder is guaranteed for a period of
twenty five years
from
the date of installation
4
.
Registering the product with Grant Engineering (UK) Limited
Please register your cylinder with Grant Engineering UK Limited
within thirty days of installation
. To do so visit www.grantuk.
com and follow the links to the ‘Homeowners Zone’, where you
can register your cylinder for a further
twelve months
guarantee
(giving
two years
from the date of installation
4
). This does not
affect your statutory rights
1
.
If a fault or defect occurs within the manufacturer’s
guarantee period
If your cylinder should fail within the guarantee period, you must
contact Grant Engineering (UK) Limited who will arrange for
the repair under the terms of the guarantee, providing that the
cylinder has been correctly installed, commissioned and serviced
(if the appliance has been installed for more than twelve months)
by a competent person and the fault is not due to tampering,
misuse or the failure of any external components not supplied by
Grant Engineering (UK) Limited, e.g. pipework, etc.
This two year guarantee only applies if the cylinder is
registered with Grant Engineering (UK) Limited within thirty
days of installation
4
and is serviced after twelve months
3
.
In the first instance
Contact your installer or commissioning engineer to ensure
that the fault does not lie with the system components or any
incorrect setting of the system controls that falls outside of the
manufacturer’s guarantee otherwise a service charge could result.
Grant Engineering (UK) Limited will not be liable for any charges
arising from this process.
If a fault covered by the manufacturer’s guarantee is found
Ask your installer to contact Grant Engineering (UK) Limited
Service Department on +44 (0)1380 736920 who will arrange for
a competent service engineer to rectify the fault.
Remember - before you contact Grant Engineering (UK)
Limited:
•
Ensure the cylinder has been installed, commissioned and
serviced by a competent person in accordance with the
installation and servicing instructions.
•
Ensure the problem is not being caused by the heating
system, its controls or any system connected to it.
Free of charge repairs
During the
two year
guarantee period no charge for parts
or labour will be made, provided that the cylinder has been
installed and commissioned correctly in accordance with the
manufacturer’s installation and servicing instructions, it was
registered with Grant Engineering (UK) Limited within thirty days
of installation and
4
, for cylinders over twelve months old, details of
annual service is available
3
.
The following documents must be made available to Grant
Engineering (UK) Limited on request:
•
Proof of purchase
•
Benchmark ‘Installation, Commissioning and Service Record
Log Book
Chargeable repairs
A charge may be made (if necessary following testing of parts) if
the breakdown is due to any fault(s) caused by the plumbing or
heating system, external electrics and external components. See
‘Extent of manufacturer’s guarantee’ below.
Extent of the manufacturer’s guarantee:
The manufacturer’s guarantee does not cover the following:
•
If the cylinder has been installed for over
two years
•
If the cylinder has not been installed, commissioned, or
serviced by a competent person in accordance with the
installation and servicing instructions.
•
The serial number has been removed or made illegible.
•
Fault(s) due to accidental damage, tampering, unauthorised
adjustment, neglect, misuse or operating the cylinder
contrary to the manufacturer’s installation and servicing
instructions.
•
Damage due to external causes such as bad weather
conditions (flood, storms, lightning, frost, snow or ice), fire,
explosion, accident or theft.
•
Fault(s) due to incorrectly sized expansion vessel(s),
incorrect vessel charge pressure or inadequate expansion on
the system.
•
Fault(s) caused by external electrics and external
components not supplied by Grant Engineering (UK) Limited.
•
Cylinder servicing, de-scaling or flushing.
•
Checking and replenishing system pressure.
•
Pipework, electrical cables and plugs and external controls
not supplied by Grant Engineering (UK) Limited.
•
Heating system components, such as radiators, pipes,
fittings, pumps and valves not supplied by Grant Engineering
(UK) Limited.
•
Instances where the cylinder has been un-installed and re-
installed in another location.
•
Use of spare parts not authorised by Grant Engineering (UK)
Limited.
13 GUARANTEE
Summary of Contents for QR Range
Page 43: ...NOTES Page 43 Notes ...