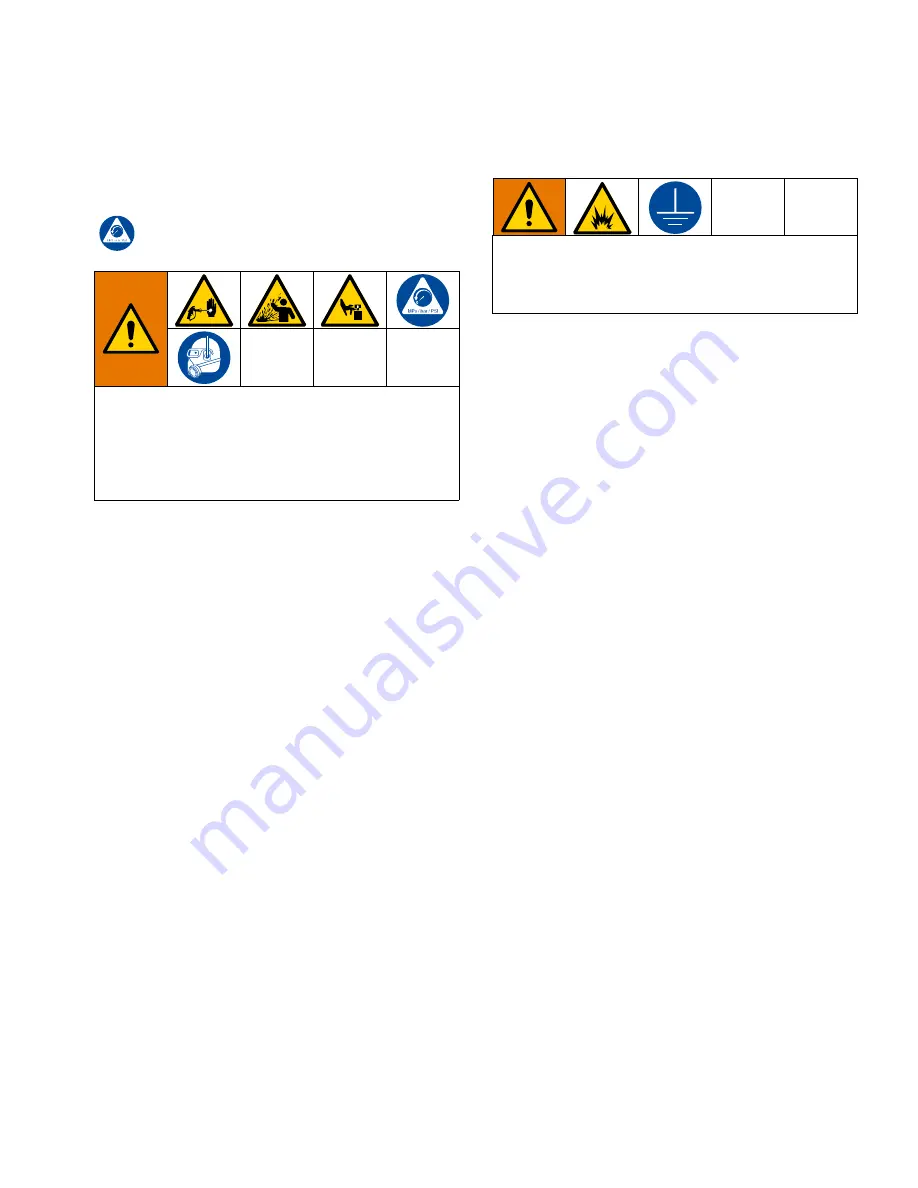
Pressure Relief Procedure
6
312145K
Pressure Relief
Procedure
Follow the Pressure Relief Procedure whenever
you see this symbol.
1.
Engage the trigger lock.
2.
Shut off the pump.
3.
Disengage the trigger lock.
4.
Hold a metal part of the gun firmly to a grounded
metal pail. Trigger the gun to relieve pressure.
5.
Engage the trigger lock.
6.
Open the fluid drain valve over a waste container
(see
System Requirements
, page 7). Leave drain
valve open.
If pressure is not fully relieved:
•
Spray tip is clogged. For RAC tip, see
Cleaning
Tips/Clearing Clogs
, page 9. For flat tip, slowly
loosen tip guard retaining nut to relieve pressure.
Remove and clean the tip.
•
Hose is clogged. Slowly loosen hose end coupling
to relieve pressure. Clean the hose obstruction.
Grounding
Check your local electrical code and pump or sprayer
manual for detailed grounding instructions.
Spray gun:
ground through connection to a properly
grounded fluid hose and pump.
Fluid hose:
use only electrically conductive hoses with
a maximum of 500 ft. (150 m) combined hose length to
ensure grounding continuity. Check electrical resistance
of hoses. If total resistance to ground exceeds 29
megohms, replace hose immediately.
Fluid supply container:
follow local code.
Object being sprayed:
follow local code.
Solvent pails used when flushing:
follow local code.
Use only conductive metal pails, placed on a grounded
surface. Do not place the pail on a nonconductive
surface, such as paper or cardboard, which interrupts
grounding continuity.
To maintain grounding continuity when flushing or
relieving pressure:
hold metal part of the spray
gun/dispense valve firmly to the side of a grounded
metal pail, then trigger the gun/valve.
This equipment stays pressurized until pressure is
manually relieved. To help prevent serious injury from
pressurized fluid, such as skin injection, splashing
fluid and moving parts, follow the Pressure Relief
Procedure when you stop spraying and before
cleaning, checking, or servicing the equipment.
The equipment must be grounded to reduce the risk
of static sparking. Static sparking can cause fumes to
ignite or explode. Grounding provides an escape wire
for the electric current.
Summary of Contents for XTR 5
Page 13: ...Repair 312145K 13 ...
Page 16: ...Parts 16 312145K XTR7 ...