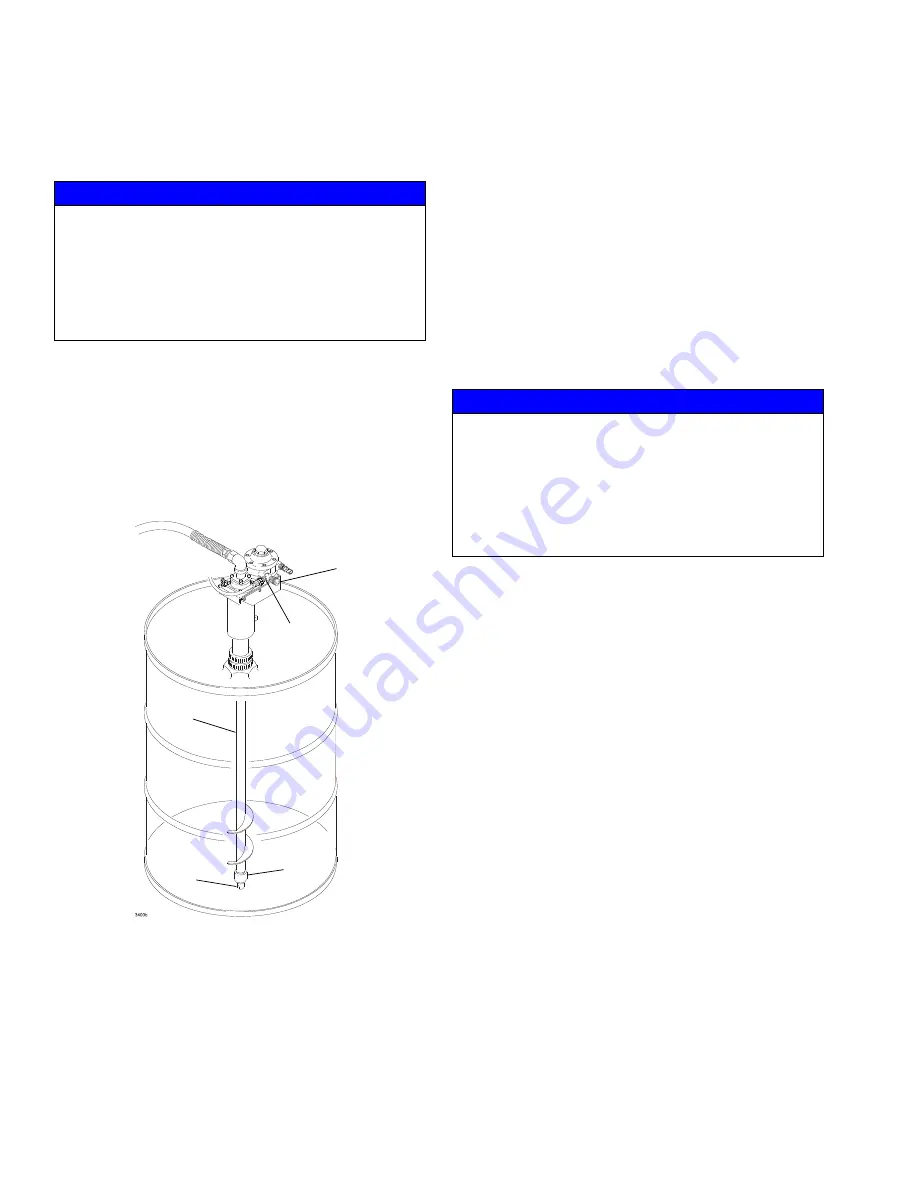
Operation
10
308345T
kit, to help prevent thick sediment from being forced into
the siphon inlet.
NOTE: If you install an air shutoff valve, the same
agitator speed is set each time it is turned on without
requiring repeated needle valve adjustments.
You can also use an air line quick-disconnect (F) as a
shutoff. See F
. 6. See Air Line Quick-Disconnect,
F
IG
. 7: Operate the Agitator
Shutdown Procedure
1.
To stop the agitator, close the needle valve (18), or
disconnect the quick-disconnect (F), or close the air
valve in the air supply line.
2.
Follow the Pressure Relief Procedure, page 9.
3.
If you remove the agitator from the drum, remove
the bearing nut (8), and hang or tilt the agitator
upright over a container to allow it to drain. Order
part number 189658, accessory handle, so you can
connect a lift hook to raise and lower the agitator or
hang the agitator to store it.
Do not let fluid dry in the fluid tubes. See Clean the
Fluid Tubes, page 12.
NOTICE
Do not operate the agitator at a high speed for a long
period of time. Excessive agitator speed can cause the
fluid to foam and can cause vibration and increased
wear on parts and damage to the drum bung. Only
agitate the fluid fast enough to maintain even mixing.
You can view fluid movement through the 0.75-in. port
on the drum cover.
Model 236629 shown
18
F
7
8
4
NOTICE
Keep the agitator upright. Do not lay it on its side or
upside down, because fluid might flow into the beltdrive
area causing damage.
If you use the accessory agitator handle, make sure the
agitator is loosened from the drum before you raise it
with a lift. The handle will not support the weight of the
drum.