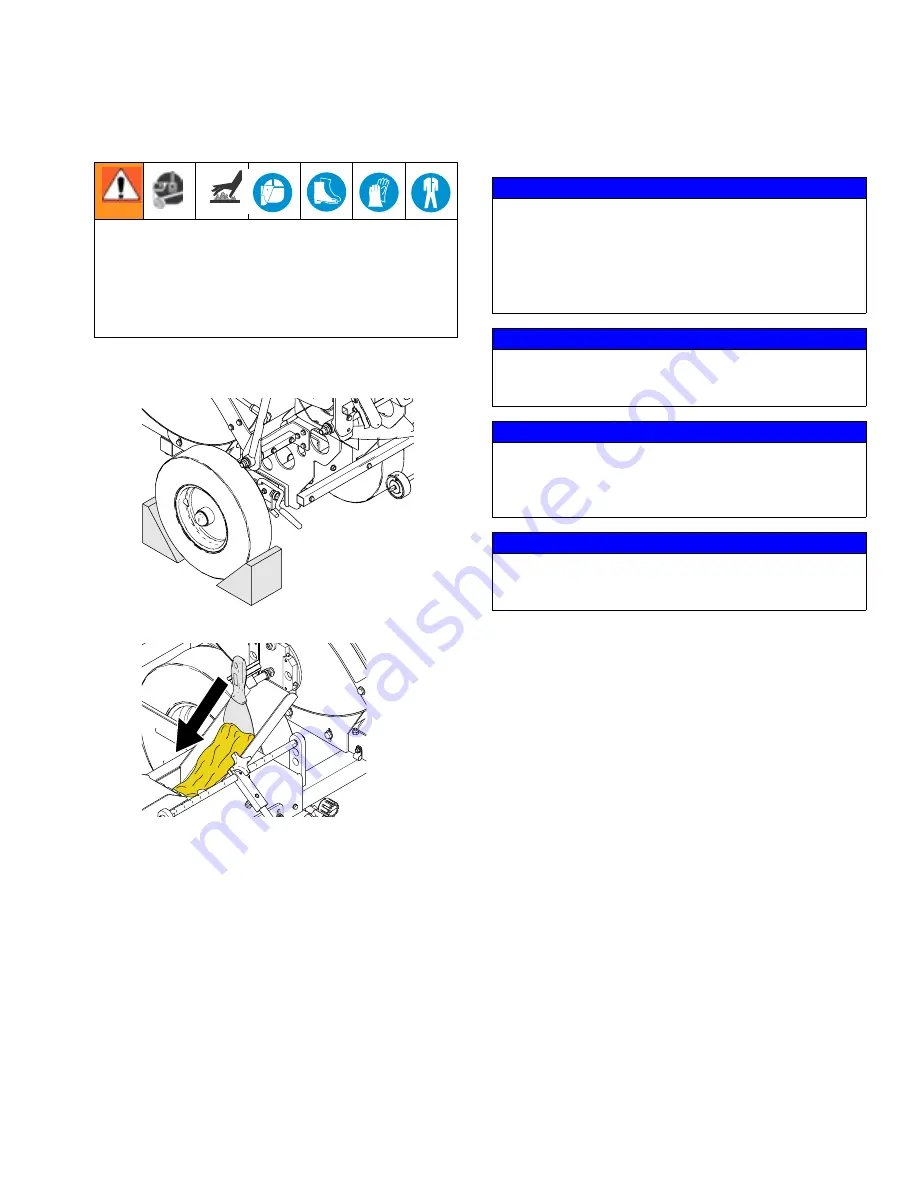
Clean-Up
313787C
19
Clean-Up
1.
Secure ThermoLazer
™
by chocking wheels.
2.
Use scraper to clean out trough and screed box.
Transporting
Remove LP-Gas supply cylinder from ThermoLazer
™
before transporting. Secure in an approved location and
method as authorized by local, state, federal, national,
and international agencies.
Always use the designated mounted lifting lugs when
lifting the Thermolazer
™
. When lifting the Thermolazer
™
only use ANSI approved slings and equipment rated for
a minimum of 2000 lb. Always use ANSI approved
equipment for securing ThermoLazer to transporting
equipment.
Never scoop out remaining melted thermoplastic from
kettle. Remaining thermoplastic can be left to harden
inside the kettle and can be remelted at a later date.
Always secure ThermoLazer
™
by chocking wheels
when adding thermoplastic.
ti14603a
ti14529a
NOTICE
Be sure to thoroughly clean all material on BlackMax
™
Screed Die bar of screed box and any open areas to
prevent material from freezing moving parts of screed
box. Always run all material out of each die before
removing. Scrape out all remaining material before it
sets within the die.
NOTICE
To prevent material from hardening and blocking flow,
scrape all excess material off of external surfaces after
each use, including the material trough.
NOTICE
When using hand torch to loosen material from screed
box, do not allow flames to come in contact with screed
box springs. Screed box springs will lose their temper
from flames and will not properly close screed box.
NOTICE
Remove any remaining beads in the bead hopper and
bead dispenser to prevent beads from clogging hopper
and dispenser.
Summary of Contents for ThermoLazer 257500
Page 23: ...Notes 313787C 23 Notes...