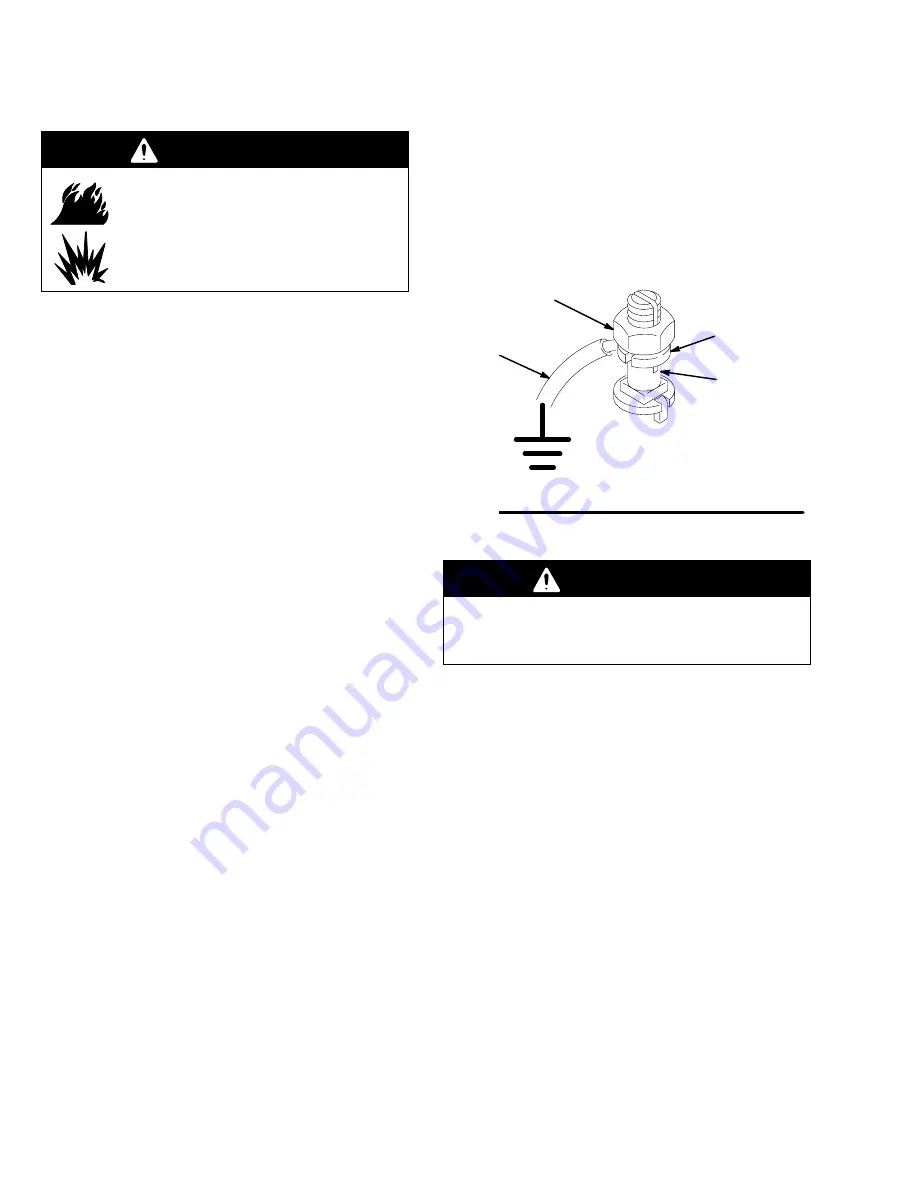
4
307013
Installation
Grounding
WARNING
FIRE AND EXPLOSION HAZARD
Before operating, ground the system as
explained below. Also read the section
FIRE AND EXPLOSION HAZARD on
page 3.
To reduce the risk of static sparking, ground the pump
and all other components used or located in the spray/
dispensing area. Check your local electrical code for
detailed instructions for your area and type of equip-
ment and be sure to ground all of these components.
D
Pump: loosen the grounding lug locknut (W) and
washer (X). Insert one end of a 12 ga (1.5 mm
2
)
minimum ground wire (Y) into the slot in lug (Z) and
tighten the locknut securely. See Fig. 1. Connect
the other end of the wire to a true earth ground.
Order Part No. 237569 Ground Wire and Clamp.
D
Air and Fluid Hoses: Use only electrically conduc-
tive hoses with a maximum of 500 feet (150 m)
combined hose length to ensure grounding continu-
ity.
D
Air Compressor: follow the air compressor
manufacturer’s recommendations
D
Spray gun/dispensing valve: obtain grounding
through connection to a properly grounded fluid
hose and pump.
D
Fluid supply container: according to local code.
D
Object being sprayed: according to local code.
D
All solvent pails used when flushing, according to
local code. Use only metal pails, which are conduc-
tive. Do not place the pail on a non-conductive
surface, such as paper or cardboard, which inter-
rupts grounding continuity.
D
To maintain grounding continuity when flushing or
relieving pressure, always hold a metal part of the
gun firmly to the side of a grounded metal pail, then
trigger the gun.
Fig. 1
W
X
Y
Z
0864
Flushing Safety
WARNING
To reduce the risk of serious injury whenever you
are instructed to relieve pressure, always follow the
Pressure Relief Procedure on page 7.
Before flushing, be sure the entire system and flushing
pails are properly grounded. Refer to Grounding at
left. Follow the Pressure Relief Procedure on page
7, and remove the spray tip/nozzle from the gun/dis-
pensing valve. Always use the lowest possible fluid
pressure, and maintain firm metal-to-metal contact
between the gun/dispensing valve and the pail during
flushing to reduce the risk of fluid injection injury, static
sparking, and splashing.
Summary of Contents for Ratio King 224434
Page 13: ...13 307013 Notes ...