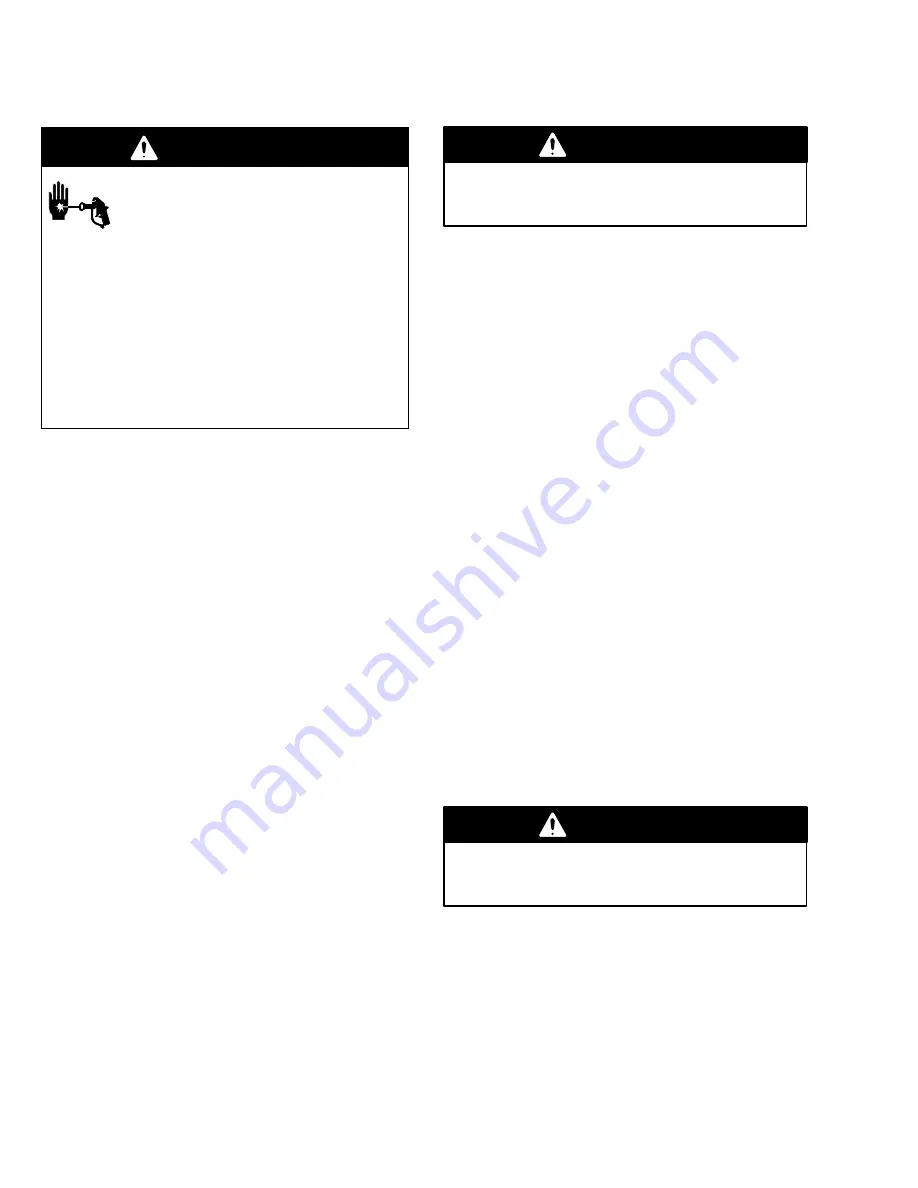
8
308738
Operation
Pressure Relief Procedure
WARNING
INJECTION HAZARD
The system pressure must be manually
relieved to prevent the system from
starting or spraying accidentally. Fluid
under high pressure can be injected through the
skin and cause serious injury. To reduce the risk of
an injury from injection, splashing fluid, or moving
parts, follow the
Pressure Relief Procedure
whenever you:
D
are instructed to relieve the pressure,
D
stop spraying,
D
check or service any of the system equipment,
D
or install or clean the spray tip.
1.
Lock the gun trigger safety.
2.
Shut off the air supply to the pump.
3.
Close the bleed-type master air valve (required in
your system).
4.
Unlock the gun/valve trigger safety.
5.
Hold a metal part of the gun/valve firmly to the side
of a grounded metal pail, and trigger the gun/valve
to relieve pressure.
6.
Lock the gun/valve trigger safety.
7.
Open the drain valve (required in your system),
and have a container ready to catch the drainage.
8.
Leave the drain valve open until you are ready to
spray again.
If you suspect that the spray tip/nozzle or hose is
completely clogged, or that pressure has not been fully
relieved after following the steps above,
very slowly
loosen the tip guard retaining nut or hose end coupling
and relieve pressure gradually, then loosen it
completely. Then clear the tip/nozzle or hose.
Flush the Pump Before First Use
The pump is tested with lightweight oil, which is left in
to protect the pump parts. If the fluid you are using
may be contaminated by the oil, flush it out with a
compatible solvent before using the pump. If the pump
is being used to supply a circulating system, allow the
solvent to circulate until the pump is thoroughly
flushed. See
Flushing the Pump
on page 9.
Packing Nut/Wet-Cup
WARNING
To reduce the risk of serious injury whenever you
are instructed to relieve pressure, always follow the
Pressure Relief Procedure
at left.
Keep the packing nut/wet-cup (S) filled with Graco
Throat Seal Liquid (TSL) or compatible solvent to help
prolong the packing life. Check the tightness of the
packing nut weekly; tighten just enough to prevent
leakage; do not overtighten it. See Fig. 3 on page 11.
Relieve the pressure before adjusting the packing nut
or adding TSL.
Starting and Adjusting the Pump
Begin these steps
before
you install the spray
tip/nozzle.
1.
Ensure that the air regulator (E) and bleed-type
master air valve (D) are closed. See Fig. 2 on
page 6.
2.
Hold a metal part of the gun/valve firmly to the side
of a grounded metal pail and hold the trigger open.
3.
Open the pump’s bleed-type master air valve (D).
4.
Slowly open the air regulator (E) until the pump
starts; approximately 2.8 bar (0.28 MPa, 40 psi).
5.
Cycle the pump slowly until all the air is pushed
out and the pump and hoses are fully primed.
6.
Release the gun/valve trigger and lock the trigger
safety. The pump should stall against pressure
when you release the trigger.
WARNING
To reduce the risk of serious injury whenever you
are instructed to relieve pressure, always follow the
Pressure Relief Procedure
at left.
7.
Relieve the pressure
.
8.
Install the spray tip/nozzle in the gun/valve.