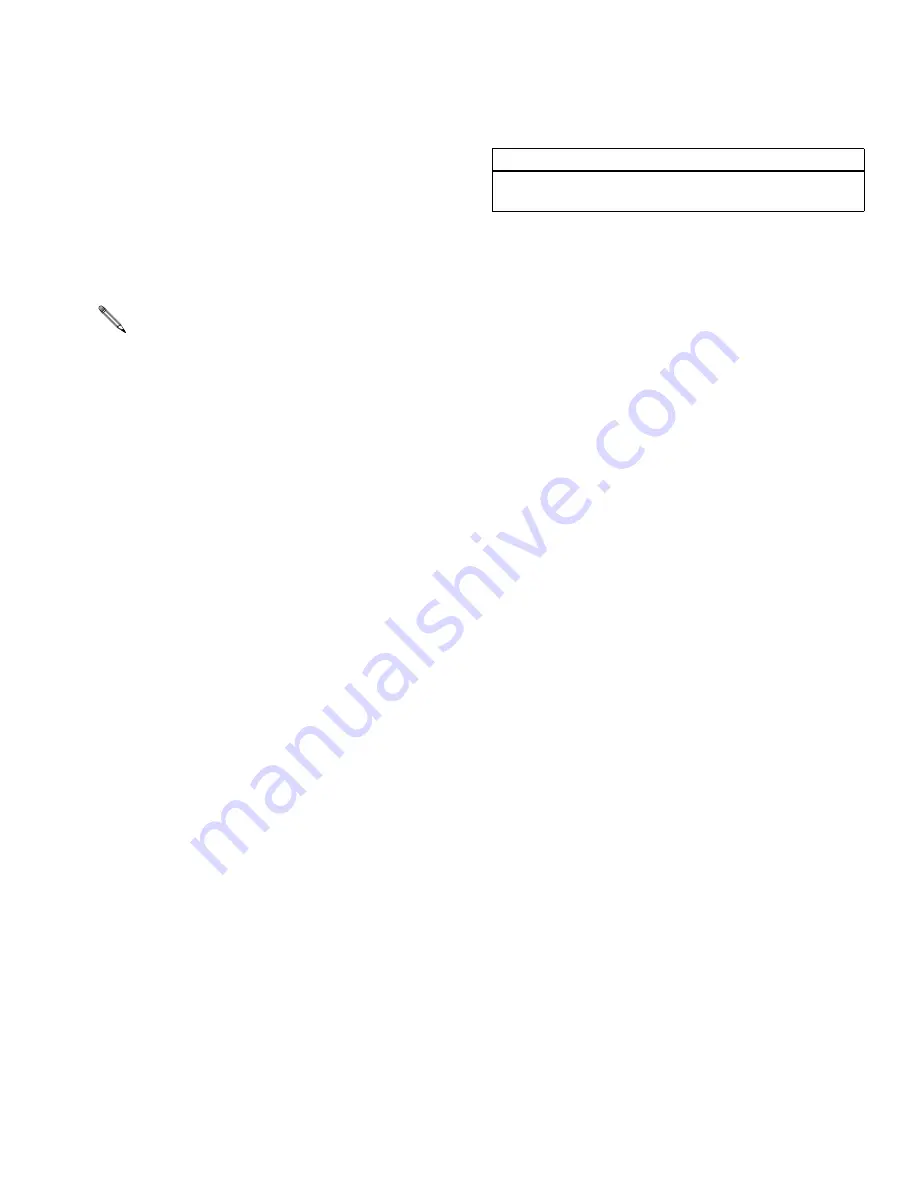
Installation
309403R
7
Install Orbital Dispenser
To attach the tool mounted orbital dispenser, perform
the following steps:
1. Align the dispenser with the alignment pins in the
robot arm.
2. Tighten the two M5 x 0.8 screws securing the dis-
penser to the robot arm.
3. Attach the dispense valve to the orbital dispenser by
tightening the 3/4-16 37° SAE swivel union.
4. Make sure the coupling is tight to avoid material
leakage.
For detailed specifications, refer to the information pro-
vided in
Cable Assemblies
Connect Motor Control Cable
Motor control cables are supplied in four lengths, 6 ft
(1.8 m), 9 ft (2.7 m), 15 ft (4.6 m), and 55 ft (16.8). The
55 ft cable may be used by itself. The 6 ft, 9 ft, and 15 ft
cable must be used with the 55 ft cable.
To connect the motor cable between the control assem-
bly and the orbital dispenser, do the following:
1. Locate the receptacle for your system:
•
PrecisionSwirl 918616:
Use the MOTOR
CABLE receptacle on the bottom of the control
assembly.
•
PrecisionFlo XL:
Use the SW-1 or SW-2 recep-
tacle on the control box.
•
PCF, PrecisionSwirl 16K601-16K610, or Expan-
sion Swirl Enclosure 16M350-16M351:
Use the
receptacle located on the right side of the enclo-
sure.
2. Connect the orbital dispenser cable (55 ft) to the
receptacle located in the previous step.
3. Check the connections to ensure the cable is con-
nected correctly.
4. Route the motor control cable and conform to the
following cable routing requirements:
•
Avoid a bend radius of less than 5 in. (12.7 cm).
•
Avoid pinch points.
•
Avoid cable pulling or stretching.
•
Keep cables from rubbing against other compo-
nents or machinery.
•
If a lot of robot wrist motion is required, leave
sufficient cable length to allow for the motion,
avoiding any cable droops that may interfere
with the machinery or substrate.
•
Route and secure the 7 in. motor cable to mini-
mize any movement. The 7 in. motor cable is
not intended to handle severe flexing motions.
•
Cable ties should only be used to loosely bun-
dle hoses together. Do not tighten cable ties to
the point where cable movement is restricted.
The dispense valve must also be supported by
additional bracketing. The swivel union is not
intended to support the weight of the dispense
valve.
CAUTION
Always make connections to the control assembly
with power turned off.