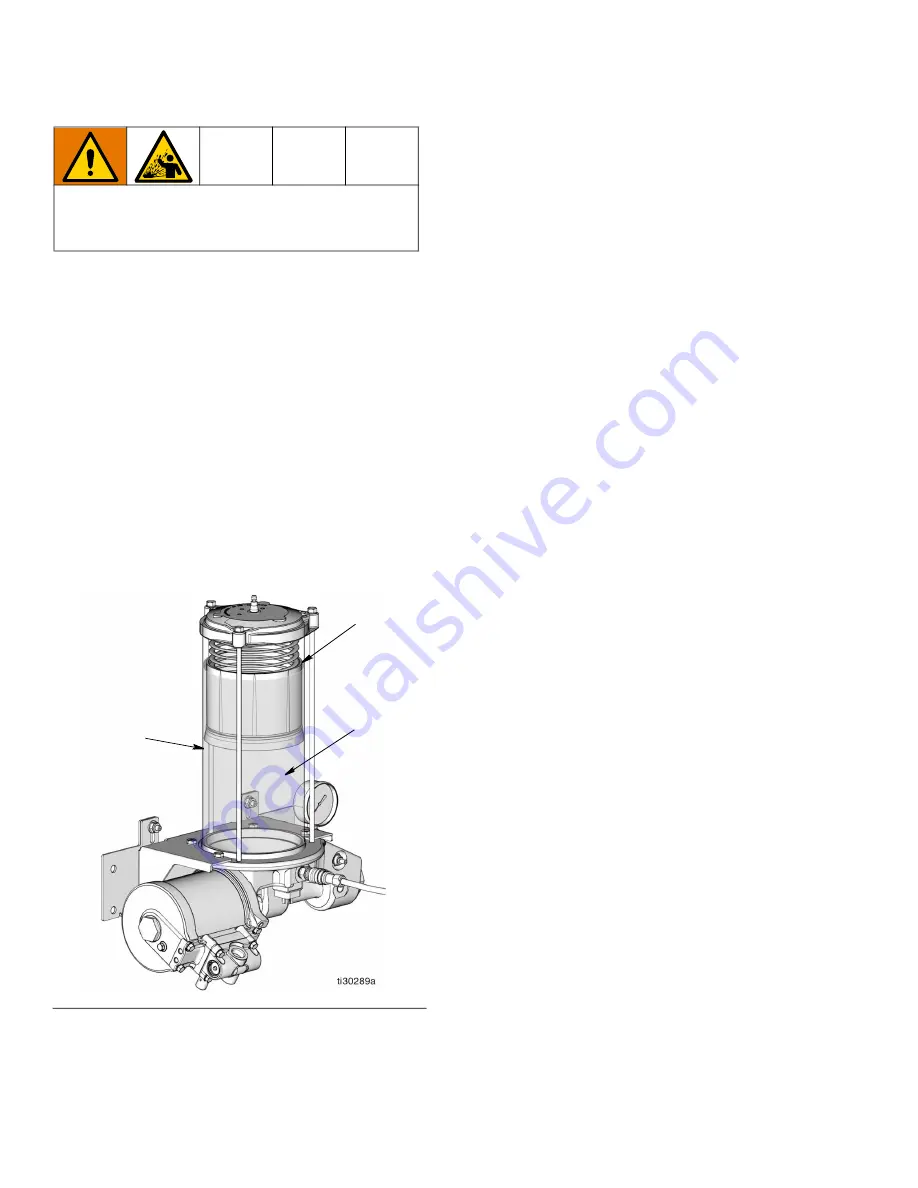
Installation
10
3A5266G
3. Slowly dispense grease from the fill pump into the
reservoir until the grease in the reservoir lifts the fol
-
lower plate (45) above the reservoir vent hole (vh)
and air is expended from under the follower plate
. 9). A small amount of grease may come out of
the vent hole at this time.
Care must be taken not to overfill the reservoir. An
over filled reservoir will vent the excess grease out
of the vent hole (vh) until enough grease is expelled
for the follower plate (45) to block the vent hole.
Overfilling the reservoir could also cause the reser
-
voir to rupture due to over-pressurization.
NOTE:
The vent hole (
vh
)
is located toward the back
right side of the reservoir and cannot be seen in F
. 9.
The approximate location of the vent hole is identified
as
vh
in the illustration.
4. Disconnect the fill pump from the fill stud (26, F
8).
5. Secure dust cap (42) over fill stud (26) (F
. 8).
Priming
Refer to F
. 2, pages 5 and 6, for the follow
-
ing instructions.
NOTE:
• Prime the pump before connecting the outlet to
supply line (G).
• Before priming the pump, the reservoir must be
filled with lubricant (see Fill Reservoir instructions,
page 8).
Run the pump until lubricant, free of air, comes out of
the pump outlet (E). It may take up to 20 pump strokes
to expel the air from the pump and deliver a continuous
flow of lubricant. This will depend on the viscosity of the
lubricant and temperature.
Supply Lines
1. Run the pump until the oil (
ol
), free of air, comes out
of the pump outlet (E). Connect the supply line (G)
to the pump outlet (E).
2. If there are multiple pumps on the air line, close the
air regulators and bleed-type master air valves to all
but one of the pumps. If there is only one pump,
open its air regulator and bleed-type master air
valve.
3. Open the master air valve from the compressor.
4. Set the air pressure to each pump at the lowest
pressure needed to get the desired results.
Feeder Lines
Fill each feeder line with lubricant prior to connecting
feeder lines to the injector outlet or divider valve.
Injectors
1. Check each injector for proper operation. The injec
-
tor stem should move when lubricant is discharged.
2. Adjust the injector output if needed to ensure that
the output volume discharged is sufficient.
Over-pressurization can result in equipment rupture
and serious injury. Fill slowly to avoid over pressuriz
-
ing reservoir.
F
IG
. 9
45
(vh)
(gr)