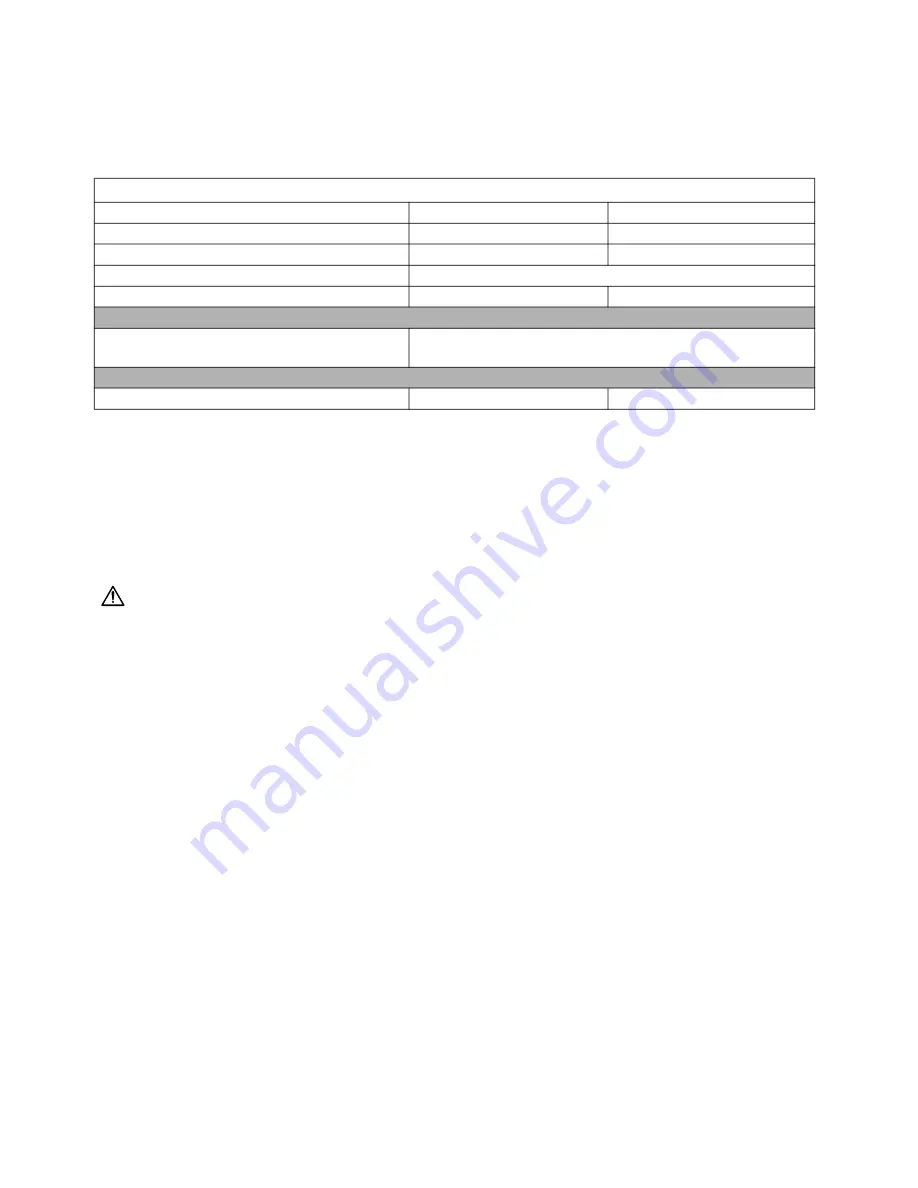
Technical Specifications
3A8563B
27
Technical Specifications
California Proposition 65
Z-Series Chemical Pumps High Wear
US
Metric
Maximum working pressure
3500 psi
24 MPa, 241 bar
Maximum operating temperature
180°F
82°C
Maximum cycle rate
65 cycles per minute
Minimum feed pressure at inlet
50 psi
0.35 MPa, 3.5 bar
Materials of Construction
Wetted materials on all models
SST, tungsten carbide, PEEK, PTFE, UHMWPE, silicon
nitride
Weight
All models
30 lbs
13.6 kg
CALIFORNIA RESIDENTS
WARNING:
Cancer and reproductive harm – www.P65warnings.ca.gov.