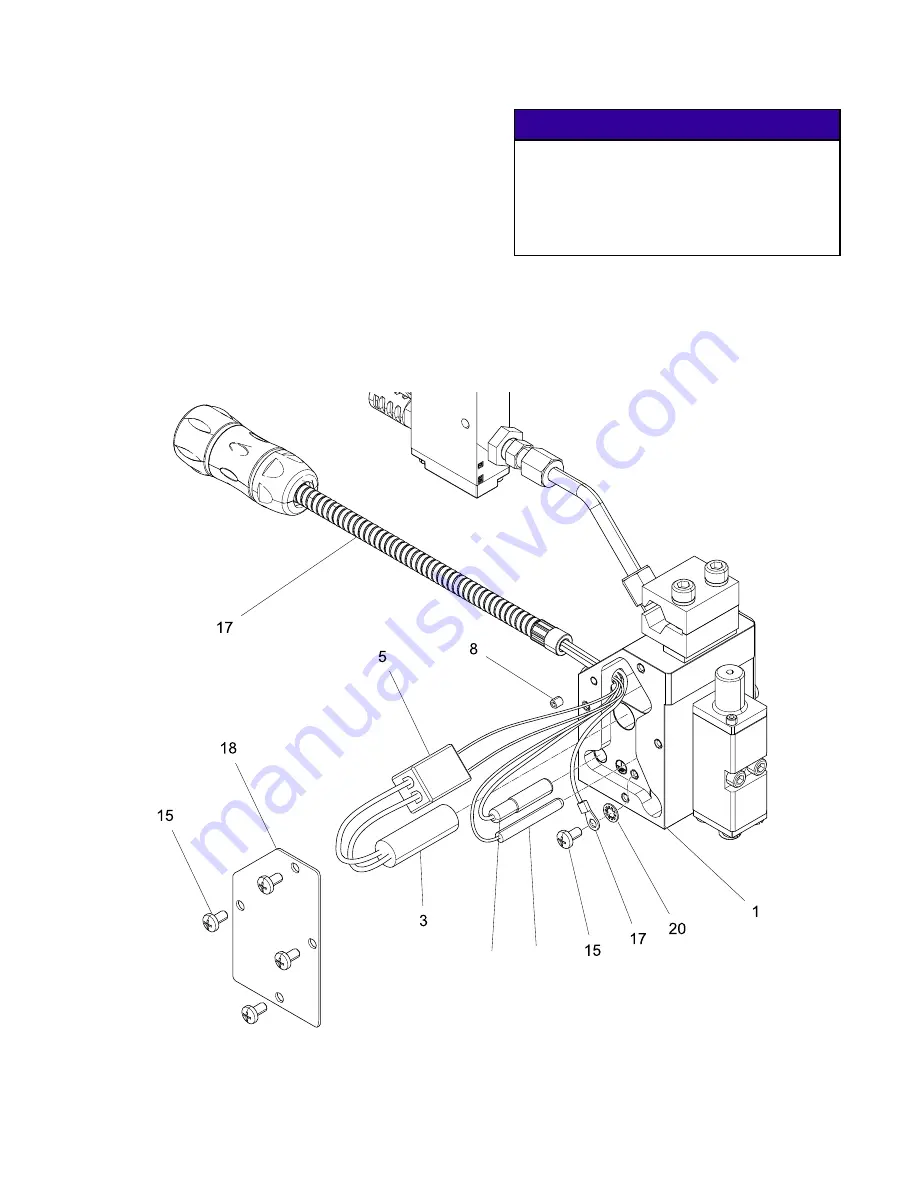
Repair
12. Reinstall the ground lead onto the manifold (1).
Note
Ensure the star washer (20) is placed
below the ground ring terminal.
13. Insert the RTD and thermal cutoff into the
manifold.
Note
Do not apply grease on the RTD.
14. Insert the terminal block (5) and heater cartridges
(3) in the manifold (1).
NOTICE
Do not pinch any wires when inserting the
terminal block in the manifold to prevent
removing wire insulation or disconnecting
wires. If wire insulation is removed, the RTD
or heaters could short out and need to be
replaced.
15. Reinstall the manifold cover plate (189).
16. Reconnect the cordset (17) to the heated hose.
17. Reconnect the solenoid valve power plug
housing to the solenoid valve.
R
T
Figure 14 Repair Parts
3A2805B
19
Summary of Contents for InvisiPac GS35 Plug-Free
Page 21: ...Notes Notes 3A2805B 21 ...