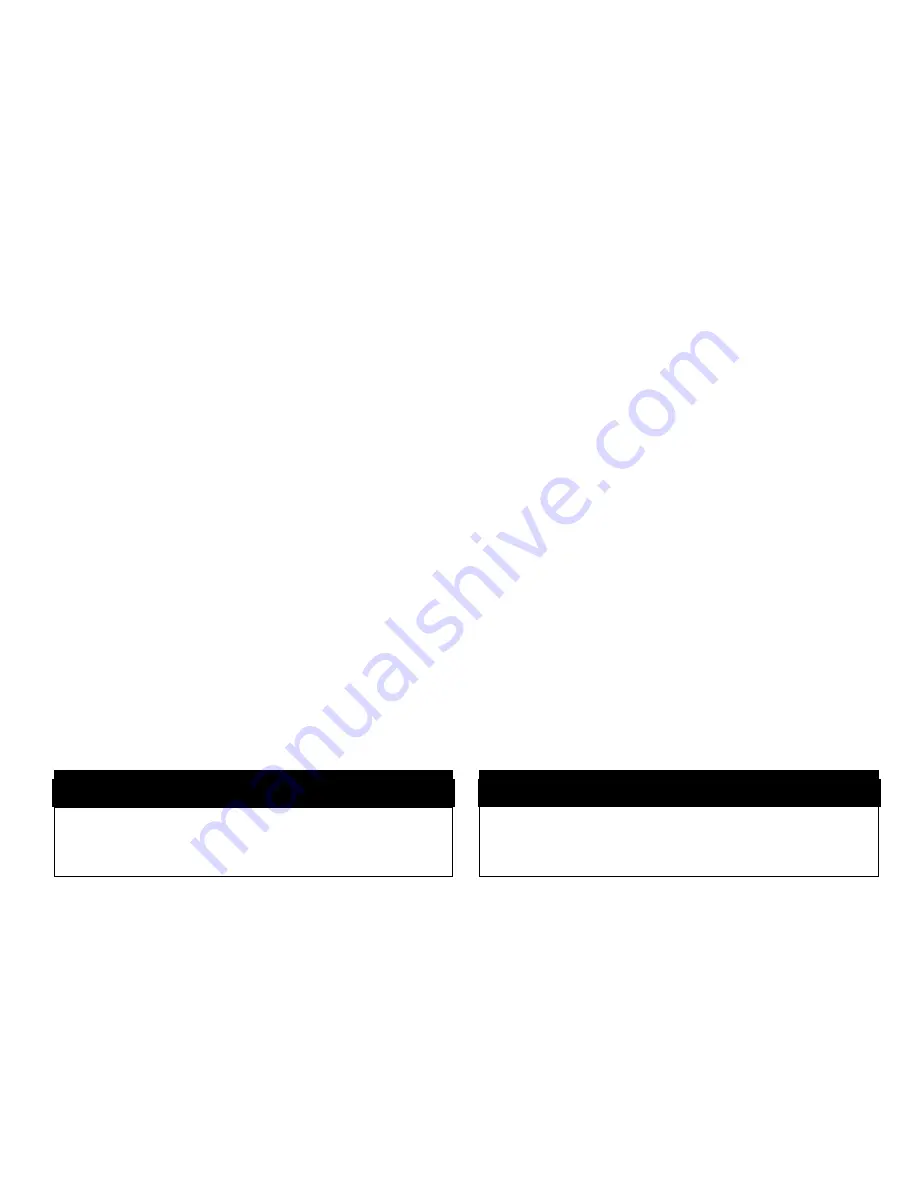
12
684025
Checking the Ratio
Note: The mix ratio must be checked at the normal
operating fluid pressure of the pump. Most mixer
manifolds provide a means for checking mix ratio
that includes needle valves for adjusting the fluid
pressure during the test. The following procedure is
an example of how to properly check the mix ratio.
1. Open the mixer manifold and trigger your spray gun.
2. Set your operating pressure. After determining the
operating pressure, release the spray gun trigger and
engage the safety latch.
3. Close the mixer manifold inlet valves.
4. Slightly open the sampling valve on the secondary
pump side. Slightly open the sampling valve on the
primary pump side. This will prevent pressure from
building up on the secondary pump, causing the relief
valve to open.
5. Place a grounded waste container under the sampling
valve.
6. Open the mixer manifold. Use the sampling valves to
adjust the pressures to your
normal operating
pressures.
7. Close the mixer manifold. Put the sampling
containers under the sampling valves.
8. Open the mixer manifold. Check the ratio; make sure
the pressure is within 20% of your normal operating
pressure. Close the mixer manifold when enough
fluid has been dispensed into the sampling
containers.
NOTE:
If the pressure readings are not within 20% of
your normal operating pressure, follow the
flushing procedure on page 11, then take a
sample again. If your sample ratio is incorrect,
there is a problem with the sampling valves, ratio
setting, or pump operation. Check the ratio
setting or service the sampling valves or pump.
Maintenance
Pump Lubrication
Wet Cups
Each of the fluid cylinders has a wet cup (18) at the top
that must be kept lubricated. See figure 6. The wet cups
should be inspected and filled on a weekly basis, or
more frequently if found to be dry. To inspect the wet
cups, follow the pressure relief procedure on page 11.
Bearings
Many of the bearing surfaces on the proportioner are
permanently lubricated or are self lubricating. There are
four main bearings (21) on the lever arm
that must be
lubricated
on a regular interval. The lubrication interval
is every six months in single shift operation. To lubricate
the bearings, follow the pressure relief procedure on
page 11.
WARNING
WARNING
To reduce the risk of serious injury whenever you are
instructed to relieve pressure, always follow the
Pressure
Relief Procedure
on page 11.
To reduce the risk of serious injury whenever you are
instructed to relieve pressure, always follow the
Pressure
Relief Procedure
on page 11.
With the bleeder type main air valve (1) turned off,
remove the thumb screws (14) and the two guards (15)
from the sides of the proportioner. The wet cups (18)
should be filled to 1/3
full with Graco Throat Seal Liquid
(TSL) or compatible solvent.
The packing nuts (19) are torqued at the factory and are
ready for operation. If one becomes loose and there is
leaking from the throat packings,
relieve the pressure,
then torque the nut to 136–149 N.m (100–110 ft-lb)
using the supplied wrench (20). Do this whenever
necessary. Do not over tighten the packing nut.
With the bleeder type main air valve turned off, remove
the twenty hex bolts (16) with a 13mm wrench or socket
and then remove the four sheet metal covers (17) from
the front and back of the proportioner.
The left rear cover may contain a sensor attached to a
cable. Do not remove the sensor, but carefully set the
cover to the side without straining or damaging the
sensor or cable. The four main bearings (21) are now
exposed. Use the adapter (205532) provided to grease all
four bearings. One or two squirts (2-3 cc) will be
sufficient.
Summary of Contents for Hydra-Cat H.P. King
Page 20: ...20 684025 NOTES ...