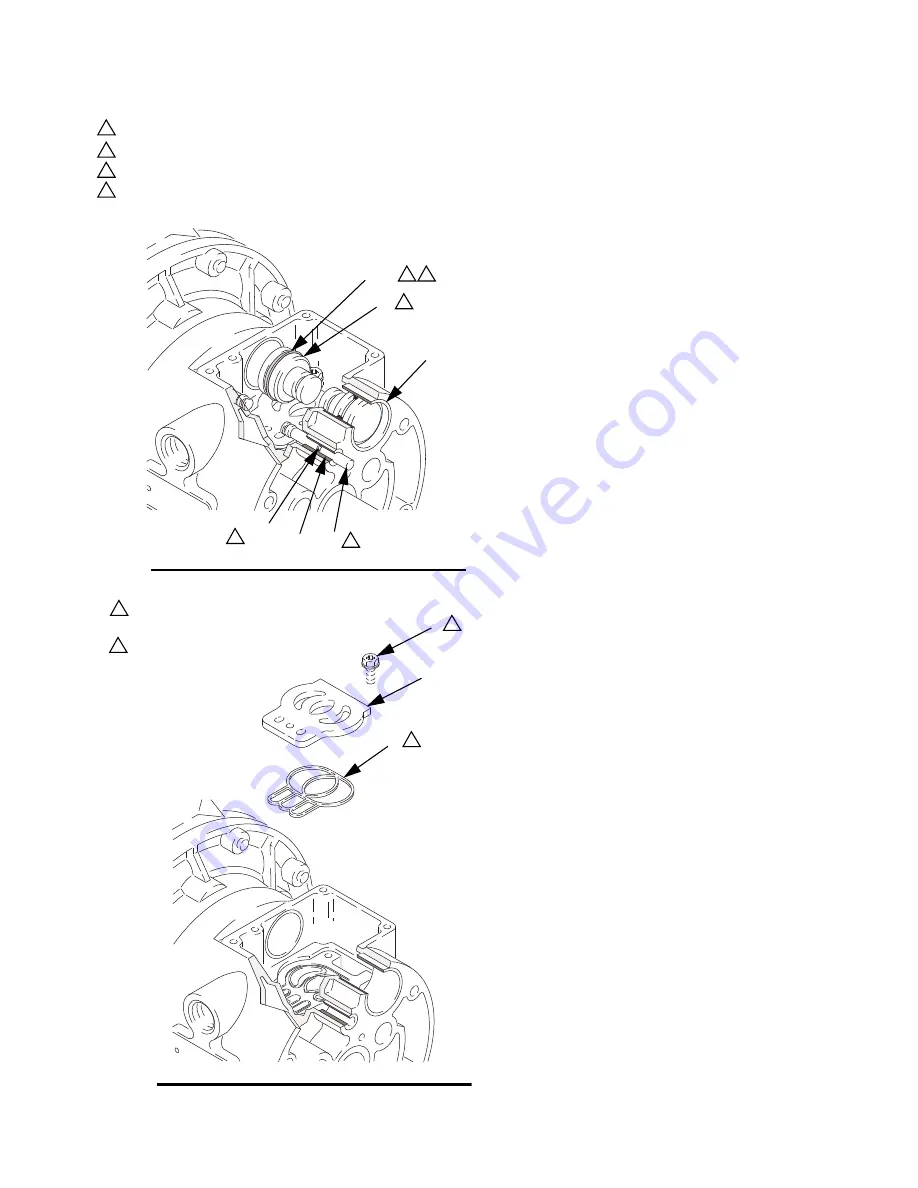
308443
17
Service
Insert narrow end first.
1
Grease.
2
Install with lips facing narrow end of piston (11).
3
Insert wide end first.
4
10
2 3
11
4
16
1
2
15
17
12
04159
Rounded side must face down (aluminum
center housing models only).
1
Tighten screws until they
bottom out on the housing.
2
9
8
3
1
2
04160
Fig. 9
Fig. 10
Reassembly
1.
If you removed the bearings (12, 15)
, reinstall as
explained on page 23. Reassemble the fluid
section.
2. On aluminum center housing models, install the
valve plate seal (9
) into the groove at the bottom of
the valve cavity. The rounded side of the seal
must
face down
into the groove. See Fig. 10.
3. Install the valve plate (8
) in the cavity. On
aluminum center housing models, the plate is
reversible, so either side can face up. Install the
three screws (3), using a Torx (T20) screwdriver or
7 mm (9/32”) socket wrench. Tighten until the
screws bottom out on the housing. See Fig. 10.
4. Install an o-ring (17
) on each pilot pin (16).
Grease the pins and o-rings. Insert the pins into the
bearings (15),
narrow
end first. See Fig. 9.
5. Install a u-cup packing (10
) on each actuator
piston (11), so the lips of the packings face the
narrow
end of the pistons. See Fig. 9.
6. Lubricate the u-cup packings (10
) and actuator
pistons (11). Insert the actuator pistons in the
bearings (12),
wide
end first. Leave the narrow end
of the pistons exposed. See Fig. 9.
7. Grease the lower face of the pilot block (18
) and
install so its tabs snap into the grooves on the ends
of the pilot pins (16). See Fig. 8.
8. Grease the o-ring (6
) and install it in the valve
block (7
). Push the block onto the valve carriage
(5). Grease the lower face of the valve block.
See
Fig. 8.
9. Install the valve carriage (5) so its tabs slip into the
grooves on the narrow end of the actuator pistons
(11). See Fig. 8.
10. Align the valve gasket (4
) and cover (2) with the
six holes in the center housing (1). Secure with six
screws (3), using a Torx (T20) screwdriver or 7 mm
(9/32”) socket wrench. Torque to 28 to 33 in-lb (3.2
to 3.7 N-m). See Fig. 7.
Summary of Contents for Husky 1040
Page 25: ...308443 25 Notes ...