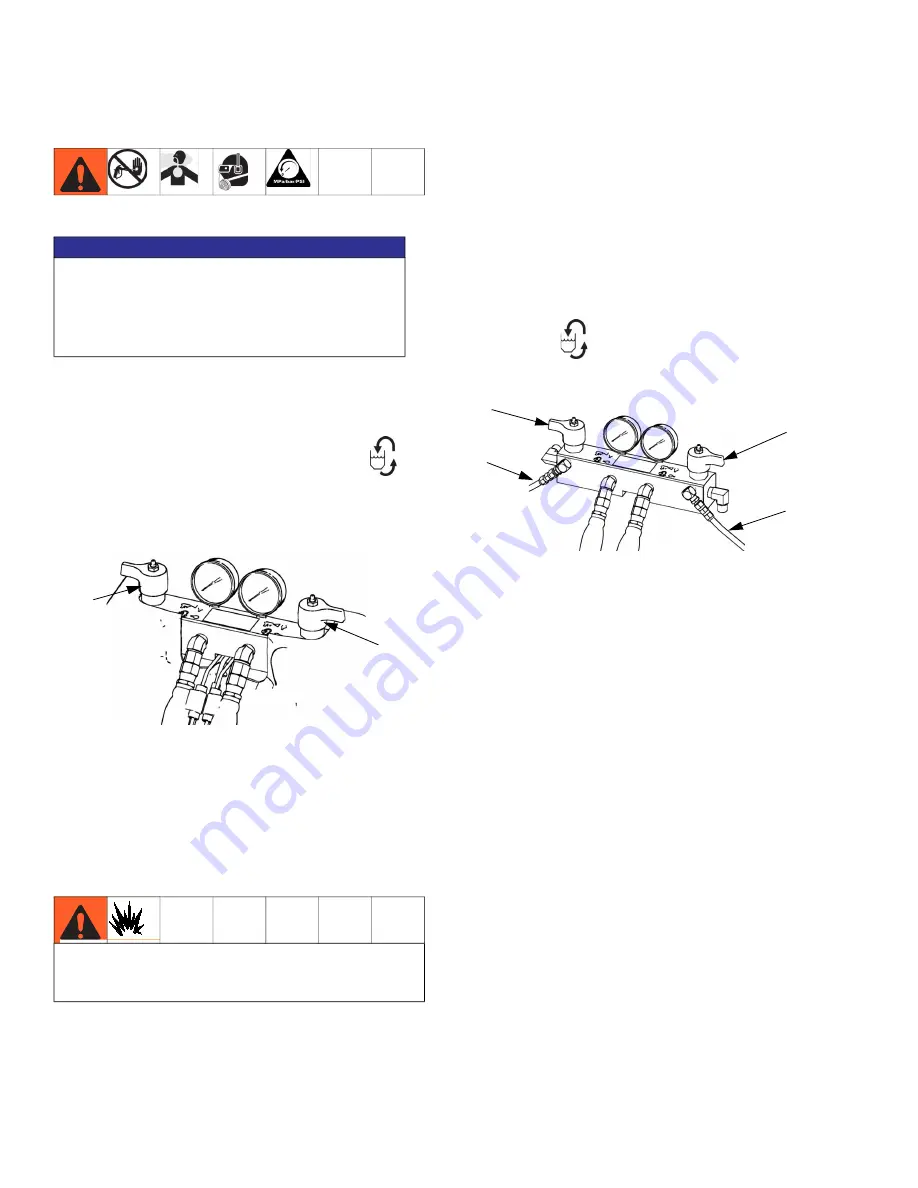
Operation
40
3A2175Z
Pressure Relief Procedure
1. Shut off feed pumps and agitator, if used.
2. Turn PRESSURE RELIEF/DISPENSE valves (SA,
SB) to PRESSURE RELIEF/CIRCULATION
.
Route fluid to waste containers or supply tanks.
Ensure gauges drop to 0.
3.
For models with an dispense valve with a safety
lock,
engage gun safety lock.
4. Relieve pressure in dispense valve. See dispense
valve manual.
Flushing
• Flush out old fluid with new fluid, or flush out old
fluid with a compatible solvent before introducing
new fluid.
• Use the lowest possible pressure when flushing.
• All fluid components are compatible with common
solvents. Use only moisture-free solvents. See
on page 136 for list of wetted compo
-
nents to verify compatibility of solvent with wetted
materials. See solvent manufacturers information
for material compatibility.
• To flush feed hoses, pumps, and heaters separately
from heated hoses, set PRESSURE RELIEF/DIS
-
PENSE valves (SA, SB) to PRESSURE RELIEF/CIR
-
CULATION
. Flush through bleed lines (N).
• To flush entire system, circulate through gun fluid
manifold (with manifold removed from gun).
• To prevent moisture from reacting with isocyanate,
always leave the system dry or filled with a mois
-
ture-free plasticizer or oil. Do not use water. See
Important Two-Component Material Information
on page 14.
•
Solvent pails used when flushing
: follow your local
code. Use only metal pails, which are conductive,
placed on a grounded surface. Do not place pail on
a nonconductive surface, such as paper or card
-
board, which interrupts grounding continuity.
•
To maintain grounding continuity when flushing or
relieving pressure,
hold a metal part of dispense
gun firmly to the side of a grounded
metal
pail, then
trigger gun.
NOTICE
The fittings on the pressure relief hoses are zinc
plated carbon steel. The hoses are cured with sul
-
fur. Check your materials for compatibility with zinc
plating and sulfur before reusing any material that
passed through them, as it may inhibit curing.
Flush equipment only in a well-ventilated area. Do not
dispense flammable fluids. Do not turn on heaters
while flushing with flammable solvents.
ti9879a1
SA
SB
SA
SB
ti9880a1
N
N
Summary of Contents for HFRL
Page 13: ...Warnings 3A2175Z 13...
Page 137: ...Accessories 3A2175Z 137...