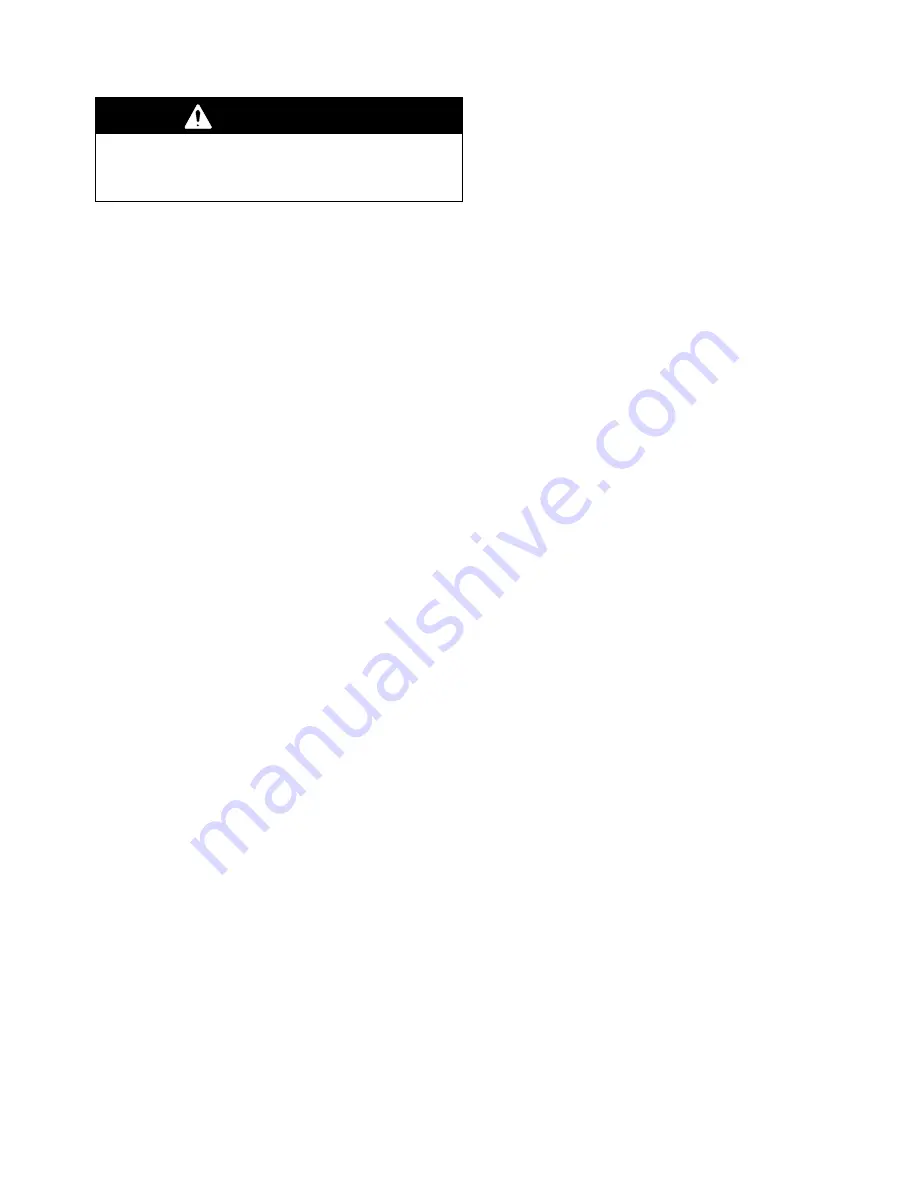
306674U 11
Displacement Pump Service
WARNING
To reduce the risk of serious injury whenever you
are instructed to relieve pressure, always follow the
Pressure Relief Procedure on page 7.
Before you start:
D
To reduce down time, be sure you have all neces-
sary repair parts available. Recommended spare
parts are listed in the parts list with a check mark,
for example ( 80
n
)
D
The balls (59) in the intake and piston valves can-
not be reseated on the hardened seats (68).
D
Repair Kit 239320 is available. If you have a repair
kit, use all the new parts for the best results. Throat
seal parts included in the kit are marked with a
dagger (
{
) and pump lower parts are marked with a
double dagger (
}
).
D
Whenever you replace the packings, also replace
the glands and bearing.
D
When cleaning parts, use a compatible solvent.
Inspect parts for wear or damage and replace as
necessary. Scoring or irregular surfaces on the
priming tube (72) or polished inner wall of the riser
tube (79) causes premature packing wear and
leaking. Check these parts by rubbing a finger on
the surface and by holding the parts up to the light
at a slight angle.
Use light, waterproof grease wherever grease is
mentioned.
Disassembly
1.
Flush the pump if possible. Follow the Pressure
Relief Procedure on page 7. Disconnect all air
and fluid hoses.
2.
Clamp the motor base in a vise. Unscrew the
priming cylinder (78).
3.
Hold the priming tube (72) with a 1/4 in (6mm)
diameter rod through the holes in the tube. Grip
the flats of the priming piston (71) with a wrench,
and unscrew the piston.
4.
Loosen the packing housing (70). Unscrew the
riser tube (79) from the air motor.
5.
Remove the packing housing (70) from the riser
tube (79), and remove the packings from the
housing.
6.
Hold the intake valve housing (67) with a wrench,
and unscrew the priming tube (72) by inserting a
1/4 in (6 mm) diameter rod through the holes in the
tube. Handle the tube carefully to avoid marring
the surface. Remove the ball, seat, and gasket.
7.
Unscrew the intake valve housing (67) from the
piston valve housing (64). Remove the ball and
packings.
8.
Clean all parts thoroughly. Grease all parts except
threads when reassembling.
Reassembly
1.
One at a time, place the female gland (74
}
), five
leather v-packings (66
}
) with the lips of the pack-
ings facing up, and the male gland (65
}
) on the
intake housing (67). Place the gasket (62
}
),
seat (68), and ball (59
}
) on the housing (67).
2.
If the pins (80) were removed from the piston valve
housing (64), replace them. Hold the piston valve
housing with a wrench and screw in the intake
valve housing.
3.
Place a gasket (62
}
), seat (68), and ball (59
}
) on
the priming tube (72). Holding the piston valve
housing (67) with a wrench, screw the priming tube
into it, using a 1/4 in. diameter rod through the
tube for leverage.
4.
Guide the riser tube (79) over the priming tube and
screw it into the motor base, making sure the
gasket (63) is in place. Torque to 50 to 70 ft-lb
(68 to 95 N-m).
5.
One at a time, place the female gland (76
}
), five
leather v-packings (73
}
) with lips of packings
facing up, a male gland (75
}
), and a bearing (69
}
)
in the packing housing (70). Screw the housing
firmly into the riser tube (79).
6.
Screw the priming piston (71) firmly onto the
priming tube (72). Screw the intake cylinder (78)
firmly onto the riser tube.
7.
Reconnect the ground wire if it was disconnected
during repair.
Summary of Contents for Fire-Ball 425 205394
Page 9: ...306674U 9 Notes...