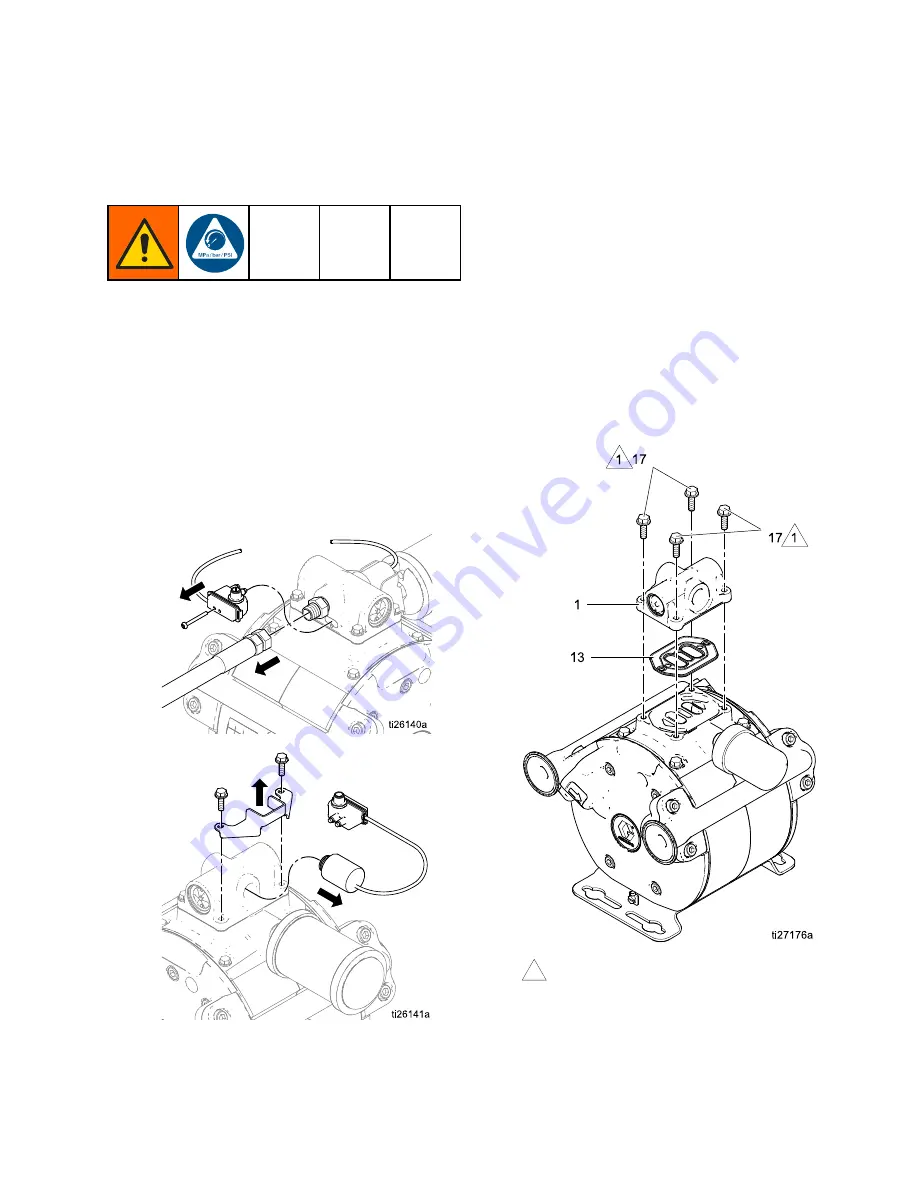
Repair/Service
Repair or Replace the Air Valve
Replace Complete Air Valve
1. Stop the pump. Follow the
Pressure Relief Procedure, page 13
.
2. Disconnect the air line.
3. For models with DataTrak:
Remove the screw to disconnect the reed switch
assembly from the air valve. Then, remove
two screws and the solenoid bracket. Pull the
solenoid out of the air valve.
4. Remove screws (17). Remove the air valve (1)
and the gasket (13).
5. To repair the air valve, go to
Replace Seals or Rebuild Air Valve, page 18
, in
next section.
6. Align the new air valve gasket (13) on the
manifold, then attach the new or repaired air
valve. See
.
7. For models with DataTrak:
Remember to reattach the solenoid bracket and
the solenoid. Then, use the screw to attach
the reed switch assembly to the new air valve.
Reconnect cable.
8. Reconnect the air line.
1
Torque to 100–120 in-lb (11–14 N•m).
333015E
17
Summary of Contents for Endura-Flo 4D150
Page 9: ...Installation Notes 333015E 9...
Page 30: ...Parts Parts 30 333015E...