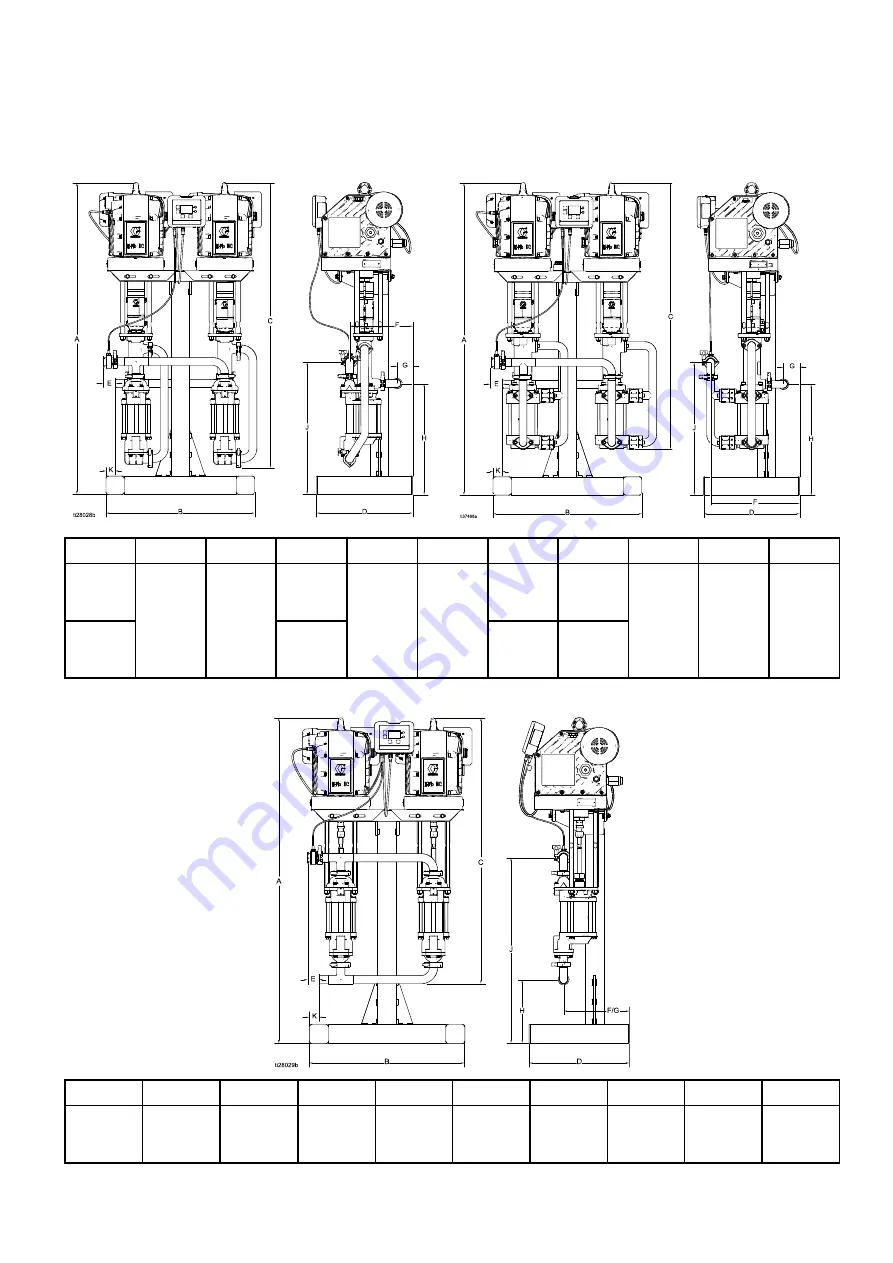
Dimensions
Dimensions
Dimensions
Pump
Pump
Pump with
with
with Sealed
Sealed
Sealed 4–Ball
4–Ball
4–Ball Lower
Lower
Lower
Pump
Pump
Pump with
with
with Sealed
Sealed
Sealed 4–Ball
4–Ball
4–Ball Plus
Plus
Plus Lower
Lower
Lower
Pumps
Pumps
Pumps
A
A
A
B
B
B
C
C
C
D
D
D
E
E
E
F
F
F
G
G
G
H
H
H
JJ
J
K
K
K
DC
4-Ball
54.5 in.
(138.4
cm)
12.1 in.
(30.7
cm)
3.0 in.
(7.6 cm)
Sealed
4-Ball
Plus
59.7 in.
(151.6
cm)
28.5 in.
(72.4
cm)
51.0 in.
(129.5
cm)
18.4 in.
(46.7
cm)
2.1 in.
(5.3 cm)
17.1 in
(43.4
cm)
3.1 in.
(7.9 cm)
21.2 in.
(53.8
cm)
25.4 in.
(64.5
cm)
1.8 in.
(3.8 cm)
Pump
Pump
Pump with
with
with Open
Open
Open Wet
Wet
Wet Cup
Cup
Cup Lower
Lower
Lower
A
A
A
B
B
B
C
C
C
D
D
D
E
E
E
F
F
F
G
G
G
H
H
H
JJ
J
K
K
K
59.7 in.
(151.6
cm)
28.5 in.
(72.4 cm)
45.5 in.
(115.6
cm)
18.4 in.
(46.7
mm)
2.1 in.
(5.3 cm)
12.1 in.
(30.7 cm)
12.1 in.
(30.7 cm)
11.7 in.
(29.7
mm)
34.1 in.
(86.6 cm)
1.75 in.
(4.4 cm)
58
3A3453H