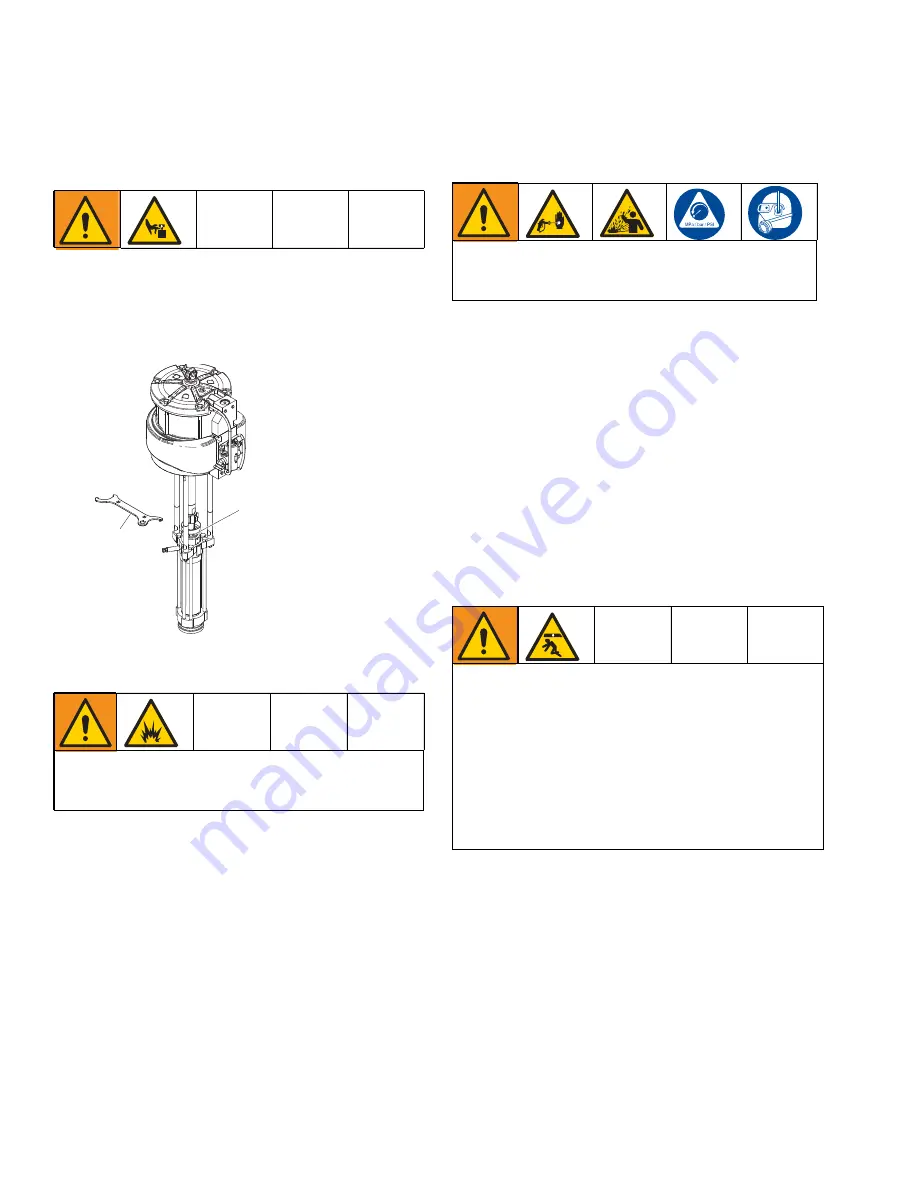
Maintenance
10
3A4100D
Maintenance
Packing Nut / Wet-Cup
1. Fill the packing nut/wet cup (P) 1/3 full with Graco
Throat Seal Liquid (TSL).
2. Use the supplied wrench (Q) to adjust the packing
nut weekly so that it is just snug. Do NOT
over-tighten.
Flushing the Pump
The pump is tested with lightweight oil, which is left in to
protect the pump parts. If the fluid you are using may be
contaminated by the oil, flush it out with a compatible
flush material before using the pump.
•
Flush at the lowest pressure possible. check
connectors for leaks and tighten as necessary.
•
Flush with a fluid that is compatible with the fluid
being dispensed and the equipment wetted
parts.
1. Perform the
Pressure Relief Procedure
2. Set pump to lowest possible fluid pressure, and then
start the pump.
3. Dispense fluid into a grounded metal pail.
Disconnecting the Displacement
Pump
1. Flush the pump if you are using flushable material.
2. Stop the pump at the bottom of its stroke.
3. Perform the
Pressure Relief Procedure
4. Disconnect the air or the hydraulic hose. Plug all
hydraulic hoses immediately to prevent the contami-
nation of the hydraulic system. Hold the fluid outlet
fitting with a wrench to keep it from being loosened
while you disconnect the fluid hose.
5. Disconnect the displacement pump (G) from the
motor (F) as follows. Make sure to note the relative
position of the pump fluid outlet to the air or hydrau-
lic inlet of the motor due to orientation restrictions on
the system. If the motor does not require servicing,
leave it attached to its mounting.
6. Using adjustable wrenches to unscrew the coupling
nut (J) from the coupling adapter (H). Remove the
coupling collars (K). Take care not to lose or drop
the collars.
7. Hold the tie rod (L) flats with a wrench to keep the
rods from turning. Unscrew the hex nuts (N) from
the tie rods extensions. Carefully remove the dis-
placement pump (G) from the motor (F).
To reduce the risk of serious injury, do not flush pump
with group 1 fluids as defined by Directive 2014/68/EU
(Pressure Equipment Directive).
WLD
4
3
To reduce the risk of serious injury whenever you are
instructed to relieve pressure, always follow the
Pres-
sure Relief Procedure
Be sure to use at least two people when lifting, moving,
or disconnecting the pump. This pump is too heavy for
one person. If you are disconnecting the displacement
pump from a motor which is still mounted (for example,
on a wall bracket), be sure to support the displacement
pump while it is being disconnected. Failure to do so
may result in the pump falling and causing injury or
property damage. Do this by securely bracing the
pump, or by having at least two people hold the pump
while another person disconnects it.