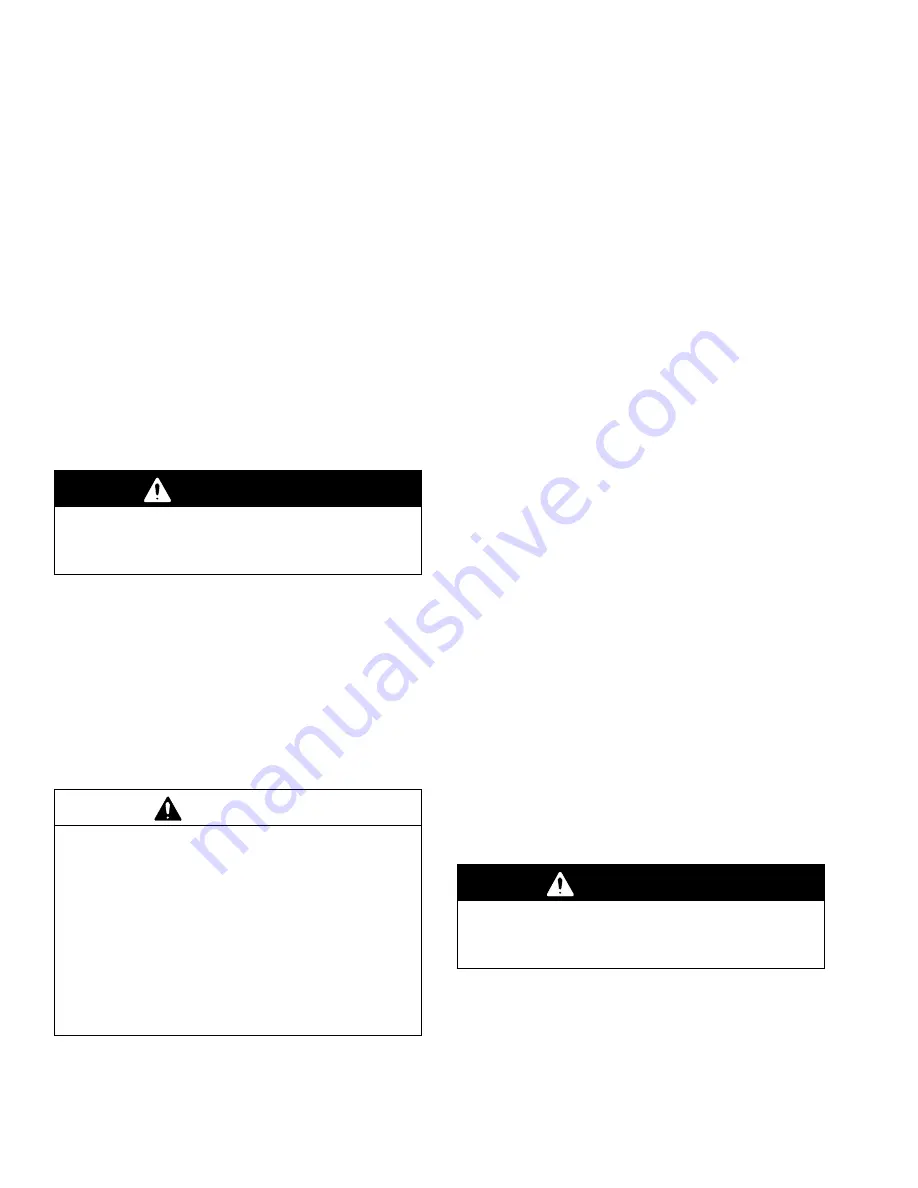
14
308350
Service
Required Tools
D
Set of adjustable wrenches
D
Large pipe wrench
D
2–3/4 in. socket wrench
D
Torque wrench
D
Rubber mallet
D
O-ring pick
D
Large vise
D
Plastic or wooden block, approximately
6 in. square x 1 in. thick
D
Thread lubricant
D
Thread sealant
Disconnecting the Displacement Pump
1.
Flush the pump, if possible. Stop the pump at the
bottom of its stroke.
WARNING
To reduce the risk of serious injury whenever you
are instructed to relieve pressure, always follow the
Pressure Relief Procedure
on page 10.
2.
Relieve the pressure.
3.
Disconnect the air hose and fluid hose.
4.
Disconnect the displacement pump (109) from the
motor (101) as follows. Note the relative position of
the pump’s fluid outlet (U) to the air inlet (V) of the
motor. If the motor does not require servicing,
leave it attached to its mounting.
CAUTION
Be sure to use two people when lifting, moving, or
disconnecting the entire pump. This pump is too
heavy for one person. If you are disconnecting the
displacement pump from a motor which is still
mounted (for example, on a wall bracket), only one
person is required. The displacement pump weighs
approximately 13 kg (29 lb).
If the pump is mounted on a cart, slowly tip the cart
backward until the handle rests on the ground, then
disconnect the displacement pump.
5.
Using an adjustable wrench (or hammer and
punch), unscrew the coupling nut (106) from the
motor shaft (W). Do not lose or drop the coupling
collars (107). See Fig. 4.
6.
Hold the tie rod flats with a wrench to keep the
rods from turning. Unscrew the nuts (108) from the
tie rods (105). Carefully remove the displacement
pump (109) from the motor (101).
7.
Refer to page 16 for displacement pump service.
To service the air motor, refer to the separate
motor manual, supplied.
Reconnecting the Displacement Pump
1.
Make sure the coupling nut (106) and the coupling
collars (107) are in place on the displacement
rod (1). See Fig. 4.
2.
Have one person hold the displacement pump
while another reconnects it to the motor (see the
CAUTION
at left). Orient the pump’s fluid
outlet (U) to the air inlet (V) as was noted in step 4
under
Disconnecting the Displacement Pump.
Position the displacement pump (109) on the tie
rods (105).
3.
Screw the nuts (108) onto the tie rods (105) and
torque to 68–81 N
S
m (50–60 ft-lb).
4.
Screw the coupling nut onto the motor shaft (W)
loosely. Hold the motor shaft flats with a wrench to
keep it from turning. Use an adjustable wrench to
tighten the coupling nut. Torque to 195–210 N
S
m
(145–155 ft-lb).
5.
Reconnect all hoses. Reconnect the ground wire if
it was disconnected. Fill the packing nut (8) 1/3 full
of Graco Throat Seal Liquid or compatible solvent.
6.
Turn on the air supply. Run the pump slowly to
ensure proper operation.
WARNING
To reduce the risk of serious injury whenever you
are instructed to relieve pressure, always follow the
Pressure Relief Procedure
on page 10.
7.
Before returning the pump to production, relieve
the pressure and retorque the packing nut (8)
to 61–75 N
S
m (45–55 ft-lb).
Summary of Contents for Dura-Flo 237634
Page 6: ...6 308350 Notes...