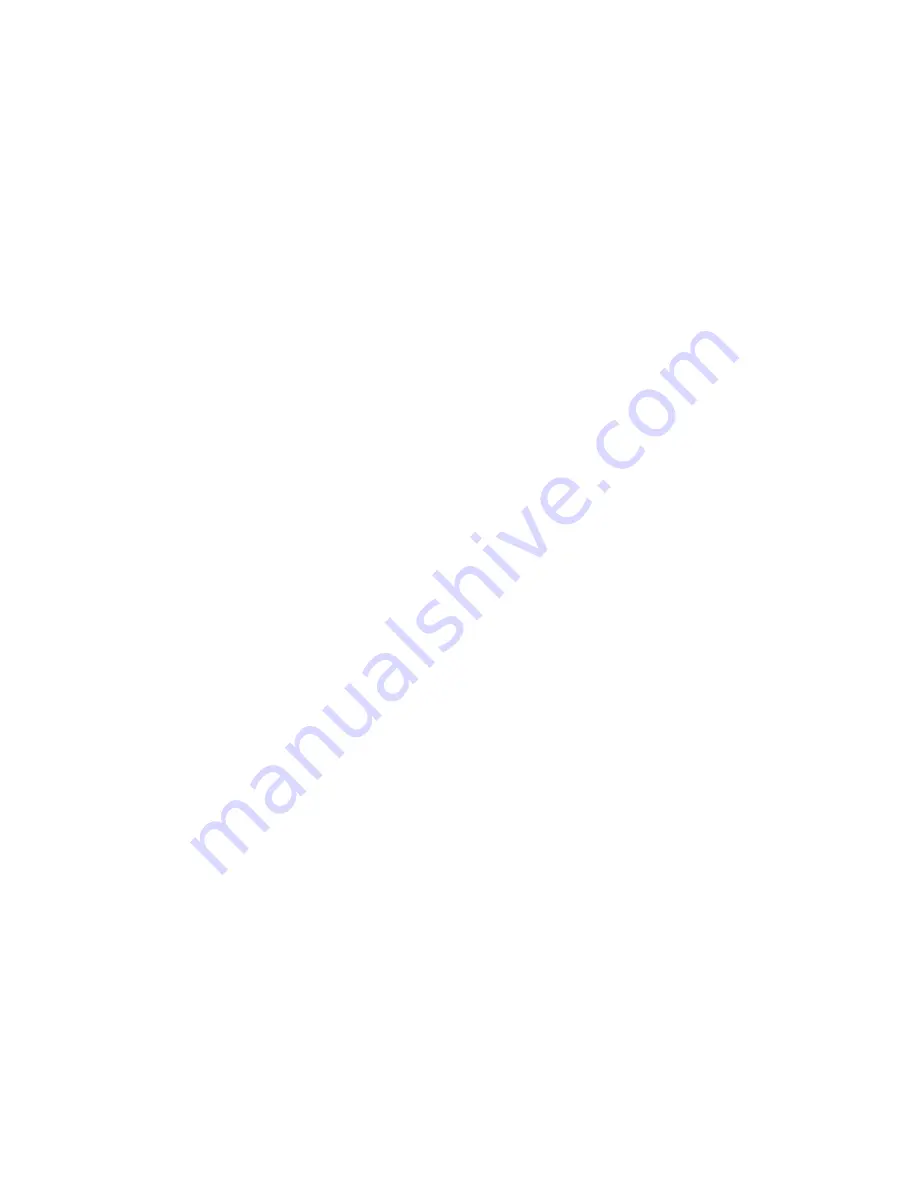
16
308-360
Service
Reassembly
1.
If it was necessary to remove the piston ball hous-
ing (10) from the displacement rod (1), clean the
threads of the rod and the ball housing. Screw the
ball housing onto the rod, hand tight. Place the
flats of the piston ball housing in a vise and torque
the rod to 386–407 N.m (285–300 ft-lb). See Fig.
7.
2.
For standard displacement pump 237–514, place
the piston packings on the piston seat housing (16)
in the following order,
with the lips of the v-pack-
ings facing up: the female gland (15*), one Teflon
v-packing (14*), four leather
v-packings (12*), and the male gland (13*). See
the Piston Packing Stack Detail in Fig. 7.
NOTE: If your pump uses an optional packing configu-
ration, or you want to convert the pump to a different
packing material, see page 20.
3.
Place the flats of the piston seat housing (16) in a
vise. Place the ball (11*) on the housing. Screw the
piston ball housing (10) onto the piston seat hous-
ing hand tight, then torque to 386–407 N.m
(285–300 ft-lb). See Fig. 6.
4.
For standard displacement pump 237–514, lubri-
cate the throat packings and place them in the out-
let housing (7) in the following order,
with the lips
of the v-packings facing down: the male gland
(6*), four leather v-packings (3*), one Teflon v-
packing (5*), and the female gland (4*). See the
Throat Packing Stack Detail in Fig. 7.
NOTE: If your pump uses an optional packing configu-
ration, or you want to convert the pump to a different
packing material, see page 20.
5.
Install the packing nut (2) loosely into the outlet
housing (7).
6.
Lubricate the piston packings. Slide the displace-
ment rod (1) and piston assembly down into the
cylinder (9). The cylinder is symmetrical, so either
end may face up. Use a rubber mallet to drive the
rod into the cylinder, until the piston seat housing
(16) is near the bottom of the cylinder.
7.
Install the seal (8*) on the top of the cylinder (9).
Lubricate the seal and the top threads of the cylin-
der.
8.
Place the outlet housing (7) in a vise, as shown in
Fig. 5. Slide the displacement rod (1) up into the
outlet housing, then screw the cylinder (9) into the
outlet housing handtight. The threads will engage
easily until the seal (8*) contacts the sealing sur-
face of the outlet housing. The top of the rod will
protrude from the packing nut (2).
9.
Install the seal (8*) on the bottom of the cylinder
(9). Lubricate the seal and the threads of the cylin-
der.
With the beveled ball stop surfaces (S) fac-
ing down (see Fig. 7), screw the intake housing
(18) onto the cylinder handtight. The threads will
engage easily until the seal contacts the sealing
surface of the intake housing.
10. Install the seal (8*) on the intake valve (19). Lubri-
cate the seal and the threads of the intake valve.
Place the intake ball (17*) in the intake housing
(18), then screw the intake valve into the intake
housing handtight. The threads will engage easily
until the seal contacts the sealing surface of the
intake housing.
11. Using a pipe wrench, torque the intake housing
(18) to 325–353 N.m (240–260 ft-lb). This will
torque both cylinder joints (A and B). See Fig. 5.
12. Using a pipe wrench, torque the intake valve (19)
to 190–217 N.m (140–150 ft-lb). See Fig. 5.
13. Torque the packing nut (2) to 136–149 N.m
(100–110 ft-lb).
14. Reconnect the displacement pump to the air motor
as explained on page 12.