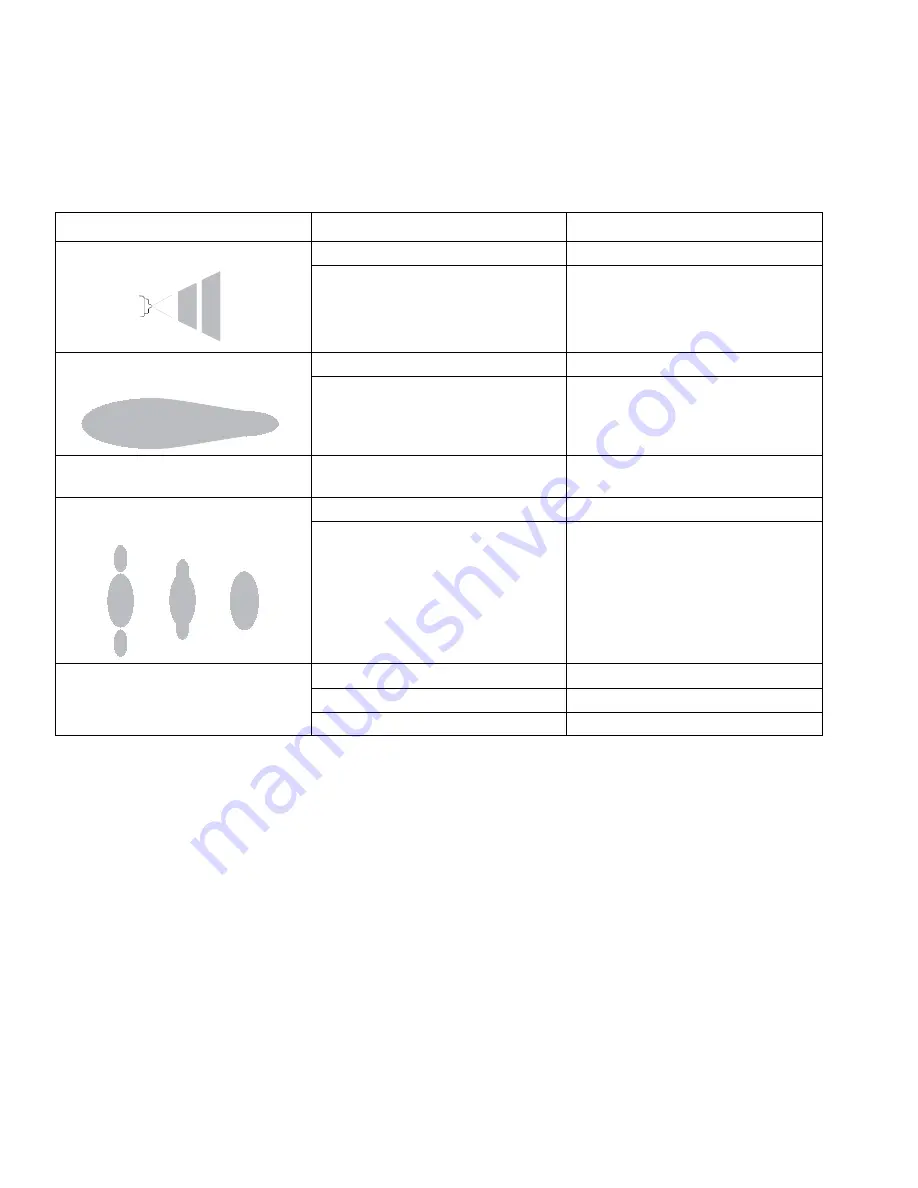
Troubleshooting
34
333013B
Spray Pattern Troubleshooting
NOTE:
Some spray pattern problems are caused by the improper balance between air and fluid.
Problem
Cause
Solution
Fluttering or spitting spray.
No fluid.
Refill supply.
Air in fluid supply.
Check fluid source. Refill.
Irregular pattern.
Fluid buildup; partially plugged tip.
Clean. See page 27.
Worn/damaged tip or air cap holes.
Clean or replace.
Pattern pushed to one side; air cap
gets dirty.
Air cap holes plugged.
Clean. See page 27.
Tails in pattern.
Atomization air pressure too low.
Increase atomization air pressure.
Fluid pressure too low.
Increase.
Fluid buildup on air cap/tip guard.
Atomization air pressure too high.
Decrease.
Fluid pressure too low.
Increase.
Plugged or damaged air cap hole
Clean, see page 27.