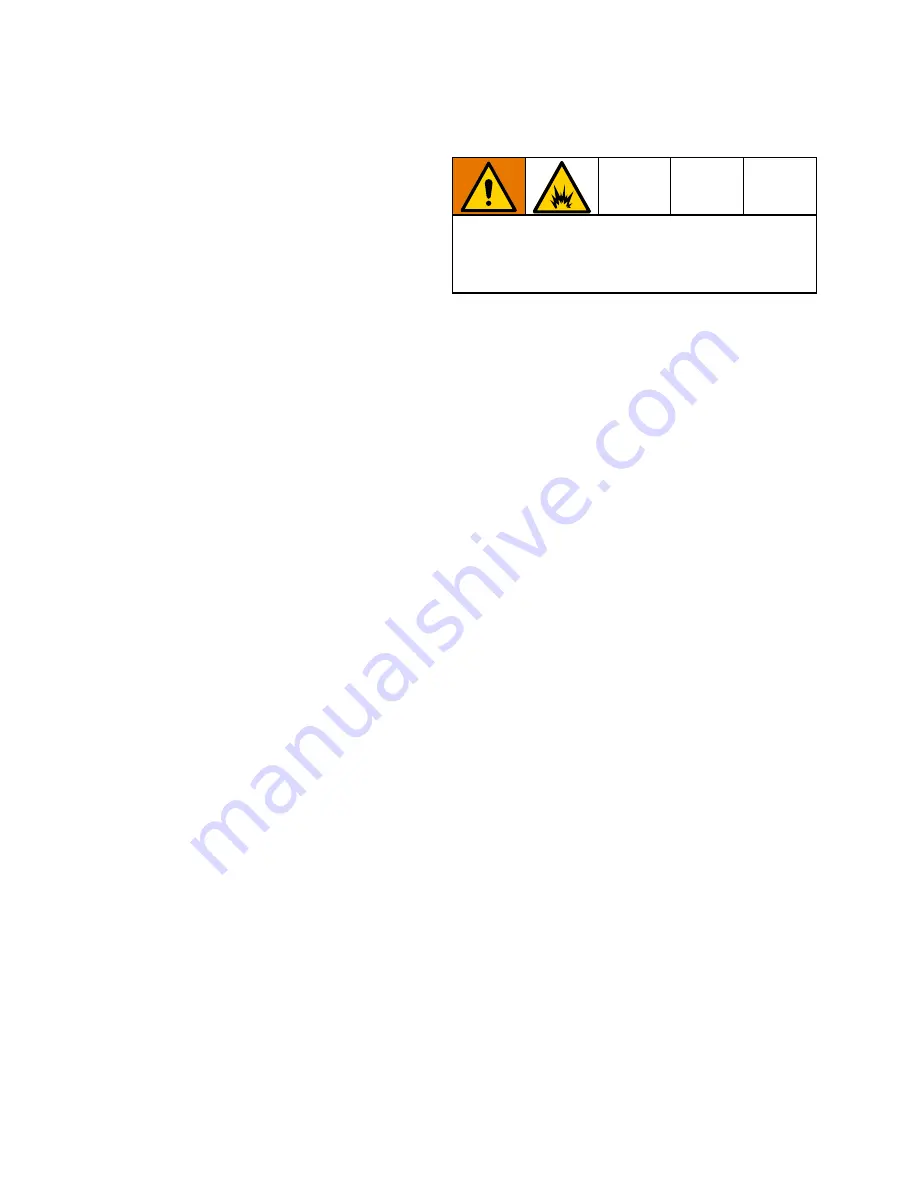
Repair
10
3A5453D
Service
Air Motor
1. Follow the
2. To remove the air motor for service, use a 3/16 hex
to remove the three setscrews (9) on the bung
adapter (4).
3. Lower the adapter (4) on the shaft (2) so coupler (3)
is accessible.
4. Use a 1/8 hex to remove the top two setscrews (8)
on the coupler (3).
5. Lift the air motor (1) straight up off the coupler (3).
•
If the air motor (1) requires more than installation of
a service kit, it is usually quickest and easiest to
send it to the Graco distributor for repair or
replacement.
•
If the air motor blades need replacing or foreign
material is present in the motor chamber, an
experienced mechanic may remove the end plate
opposite the drive shaft end. Do not pry with a
screwdriver. It will dent the surface of the plate and
body, causing leaks. Use a puller tool, which will
remove the end plate while maintaining the position
of the shaft.
Shaft and Agitator Blades
1. Remove the shaft (2) from the drum. Clean with a
compatible solvent and inspect the shaft (2) and
blades (6, 7) for wear or damage.
2. If parts need replacing, follow steps 1-4 under
3. Use the 1/8 hex to remove the other two setscrews
(8) on the coupler.
4. Slide the shaft off (2).
5. If needed, use a 3 mm (1/8 in.) hex to remove the
setscrew (8) on the hub assembly (6 or 7). Slide the
hub/blade assembly off of the shaft.
6. To install a new hub/blade assembly, slide it onto
the shaft. The setscrew must always remain on the
top, with the blades hanging down, so the blades
will pass into and out of the bung hole.
NOTE:
Air Motor Repair Kits are available. Order part
224954 for Model 26C150 (high viscosity) or part
207335 for Model 26C818 (low viscosity).
Reassembly
1. Slide the shaft (2) into the coupler (3). Use a 1/8 hex
to tighten the setscrews (8). Torque to 65 in-lb
(7.3 N•m).
2. Raise the bung adapter (4) on the shaft (2) to
reconnect to the air motor. Use a 3/16 hex to tighten
the three setscrews (9) on the bung adapter. Torque
to 80 in-lb (9 N•m).
To prevent fire and explosions from sparks due to
contact, clean only using non-flammable material or
materials having a flash point lower than 140° F
(60° C).