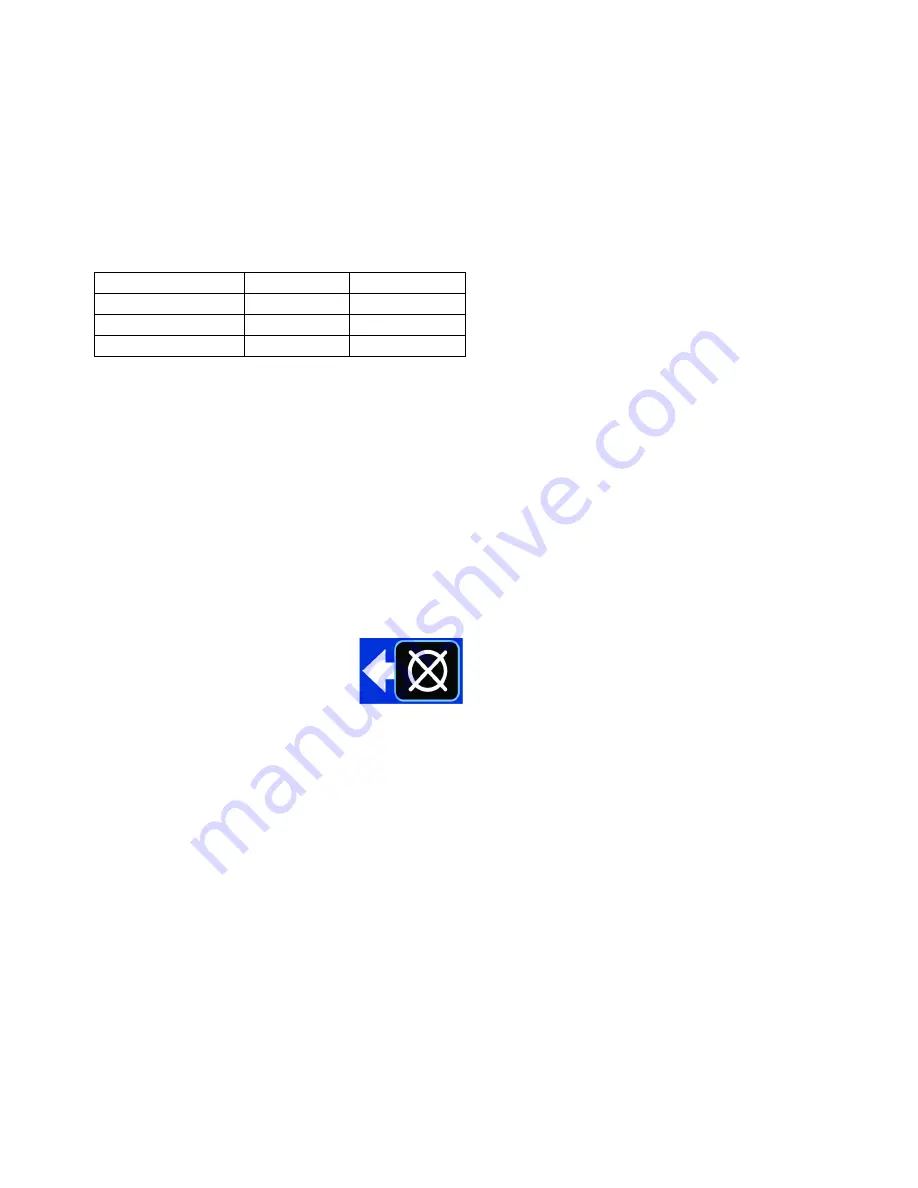
Operation
3A7031A
17
Test Mode
On the main screen press and hold both the LEFT and
RIGHT ARROWS simultaneously for 3 seconds to enter
TEST MODE.
While in TEST MODE the controller:
TEST MODE ends after 10 lubrication events. TEST
MODE is canceled by pressing the LEFT ARROW
button.
Alarms
During an alarm:
•
Pump operation is immediately disabled
•
The system LED flashes red
•
An alarm screen displays
•
An audible alarm sounds
•
Output 2 turns on
Press the reset button (LEFT ARROW
button) once to clear the buzzer. Press
and hold the reset button for 3
seconds to clear the alarm and switch
the controller to idle.
Low Level Alert State
•
Run mode continues
•
Low level LED is on (B, F
. 1)
•
System LED is on (A, F
•
Output 2 in ON
Low Level Alarm State
•
Pump operation is immediately disabled
•
Low level LED is on (B, F
. 1)
•
System LED flashes red (A, F
•
Output 2 is ON
•
Audible alarm
•
Screen shows alarm information
Clear Alarm Buzzer
Press reset (LEFT ARROW button) to silence the
buzzer.
The buzzer sounds again after 4 hours if the low level
condition is not resolved. The buzzer also sounds again
when power is cycled.
Clear Low Level Alarm
Filling the reservoir resolves a low level sensor and low
level switch condition, and the level sensor and level
switch will self-clear.
Hold the reset button for at least 5 seconds to remove
the low level alarm from the controller.
For more details regarding a specific alarm, see
, page 18 and
, page 21.
End Configuration
ON time (min) OFF time (min)
Pressure System
7
1
Timer System
2
1
Cycle System
2
1