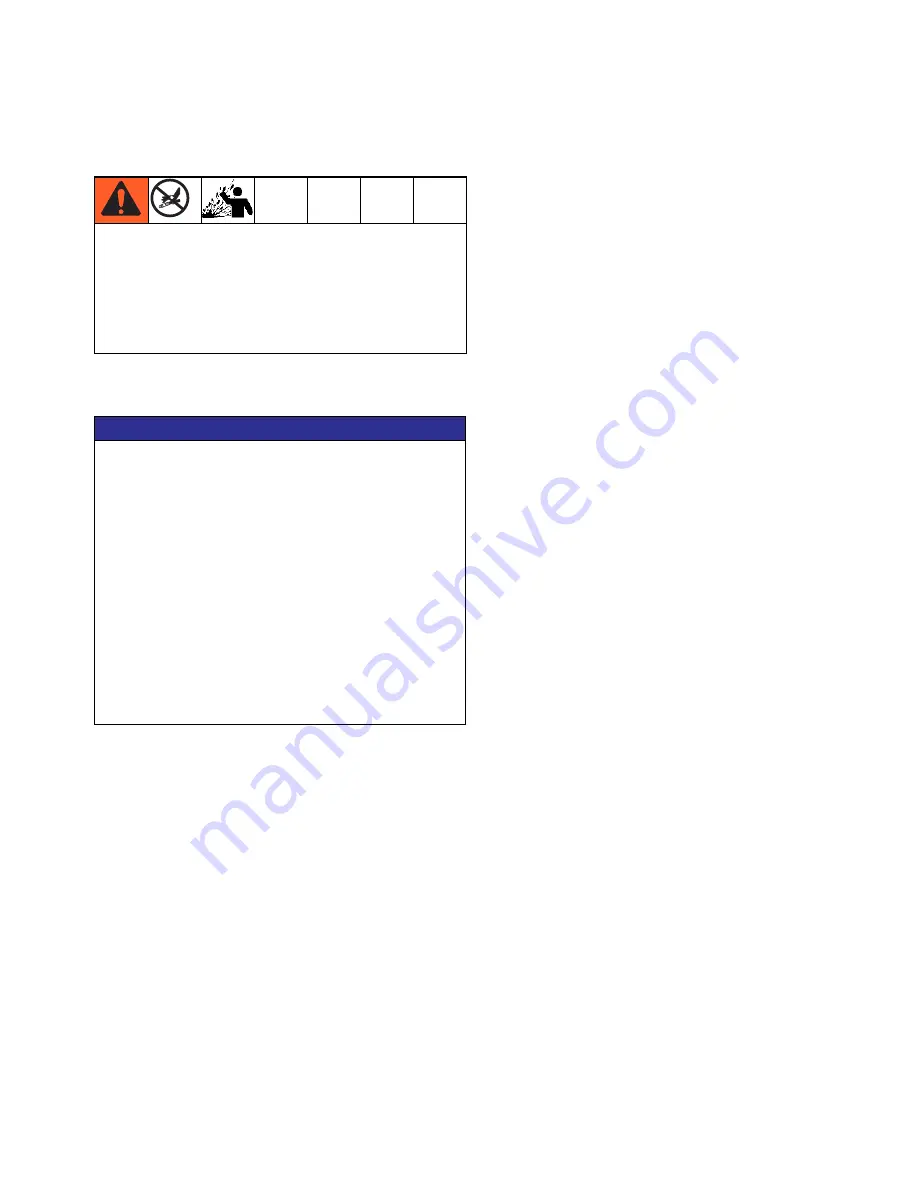
Warnings
3A2988C
5
Keep Components A and B
Separate
Changing Materials
Cross-contamination can result in cured material in
fluid lines which could cause serious injury or damage
equipment. To prevent cross-contamination:
•
Never
interchange component A and component
B wetted parts.
•
Never use solvent on one side if it has been con-
taminated from the other side.
NOTICE
Changing the material types used in your equipment
requires special attention to avoid equipment damage
and downtime.
• When changing materials, flush the equipment
multiple times to ensure it is thoroughly clean.
• Always clean any fluid inlet strainers after
flushing.
• Check with your material manufacturer for
chemical compatibility.
• When changing between epoxies and urethanes
or polyureas, disassemble and clean all fluid
components and change hoses. Epoxies often
have amines on the B (hardener) side. Polyureas
often have amines on the B (resin) side.
Summary of Contents for 262893
Page 20: ...Parts 20 3A2988C...