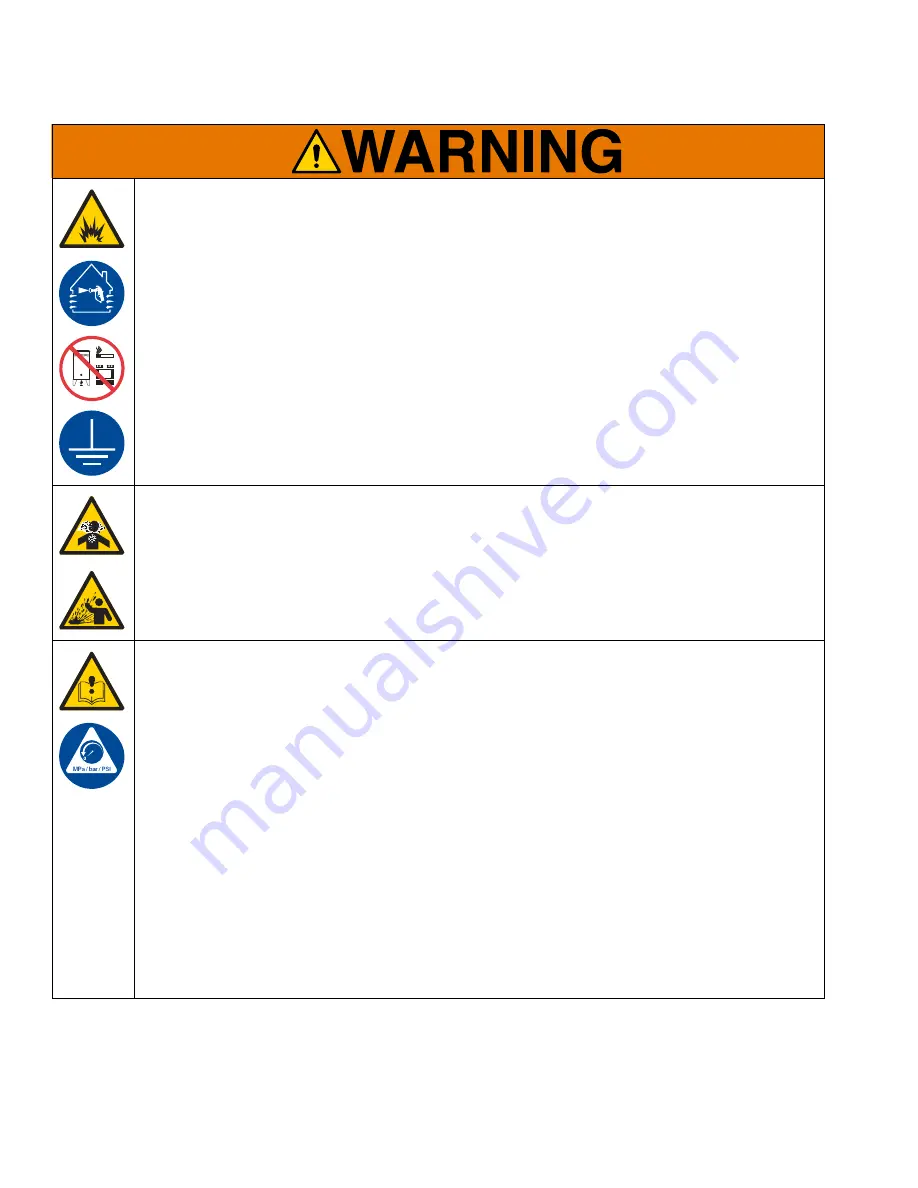
Warnings
4
3A7931B
FIRE AND EXPLOSION HAZARD
Flammable fumes, such as solvent and paint fumes, in
work area
can ignite or explode. Paint or sol-
vent flowing through the equipment can cause static sparking. To help prevent fire and explosion:
•
Use equipment only in well ventilated area.
•
Eliminate all ignition sources; such as pilot lights, cigarettes, portable electric lamps, and plastic drop
cloths (potential static sparking).
•
Ground all equipment in the work area. See
instructions.
•
Never spray or flush solvent at high pressure.
•
Keep work area free of debris, including solvent, rags and gasoline.
•
Do not plug or unplug power cords, or turn power or light switches on or off when flammable fumes
are present.
•
Use only grounded hoses.
•
Hold dispensing device/gun firmly to side of grounded pail when triggering into pail. Do not use pail
liners unless they are anti-static or conductive.
•
Stop operation immediately
if static sparking occurs or you feel a shock
.
Do not use equipment until
you identify and correct the problem.
•
Keep a working fire extinguisher in the work area.
TOXIC FLUID OR FUMES HAZARD
Toxic fluids or fumes can cause serious injury or death if splashed in the eyes or on skin, inhaled, or
swallowed.
•
Read Safety Data Sheet (SDS) to know the specific hazards of the fluids you are using.
•
Store hazardous fluid in approved containers, and dispose of it according to applicable guidelines.
EQUIPMENT MISUSE HAZARD
Misuse can cause death or serious injury.
•
Do not operate the unit when fatigued or under the influence of drugs or alcohol.
•
Do not exceed the maximum working pressure or temperature rating of the lowest rated system com-
ponent. See
in all equipment manuals.
•
Use fluids and solvents that are compatible with equipment wetted parts. See
in all equipment manuals. Read fluid and solvent manufacturer’s warnings. For complete infor-
mation about your material, request Safety Data Sheet (SDS) from distributor or retailer.
•
Do not leave the work area while equipment is energized or under pressure.
•
Turn off all equipment and follow the
when equipment is not in use.
•
Check equipment daily. Repair or replace worn or damaged parts immediately with genuine manu-
facturer’s replacement parts only.
•
Do not alter or modify equipment. Alterations or modifications may void agency approvals and create
safety hazards.
•
Make sure all equipment is rated and approved for the environment in which you are using it.
•
Use equipment only for its intended purpose. Call your distributor for information.
•
Route hoses and cables away from traffic areas, sharp edges, moving parts, and hot surfaces.
•
Do not kink or over bend hoses or use hoses to pull equipment.
•
Keep children and animals away from work area.
•
Comply with all applicable safety regulations.