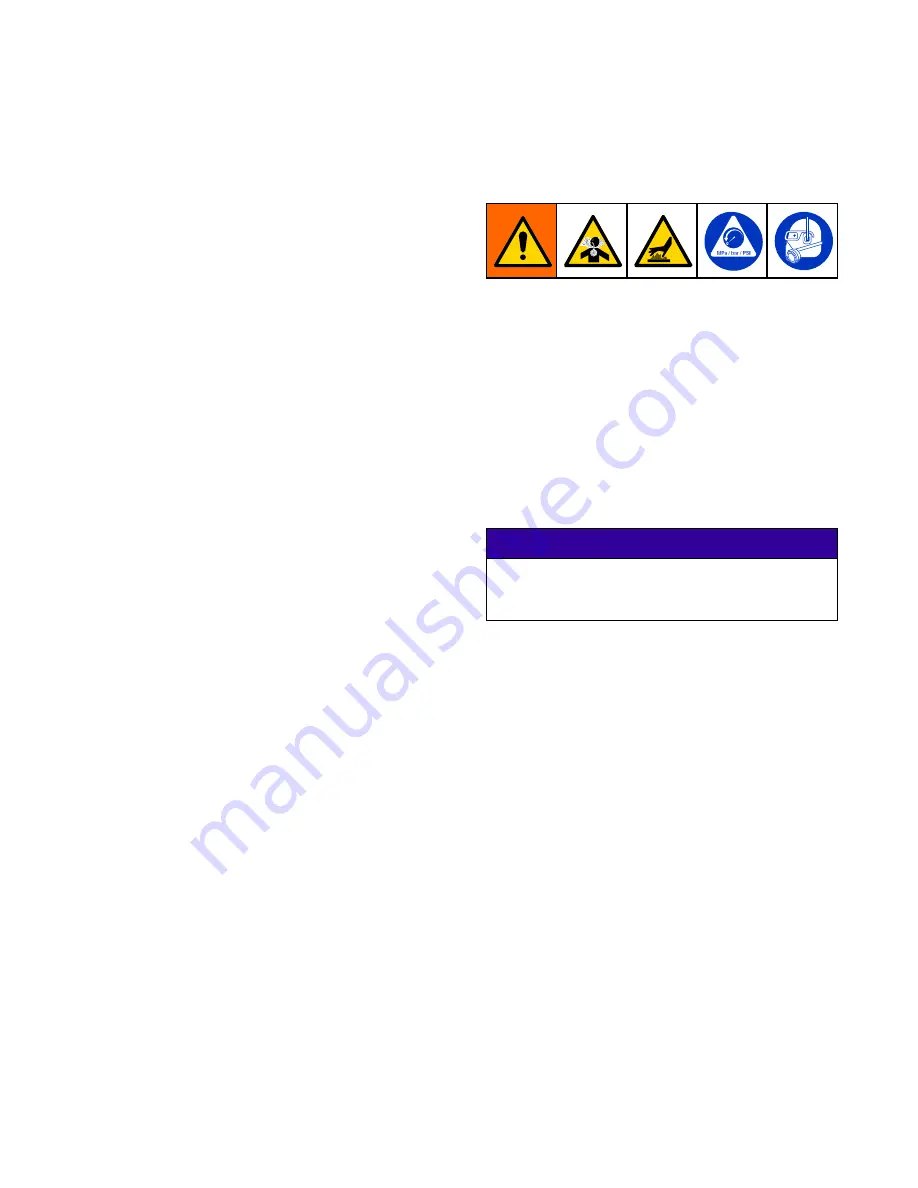
Maintenance
Maintenance
Maintenance
Maintenance
Maintenance
Maintenance Schedule
Schedule
Schedule
Establish a preventive maintenance schedule
based on the pump’s service history. Scheduled
maintenance is especially important to prevent spills
or leakage due to diaphragm failure. A clogged
muffler may restrict pump performance. Inspect
air lines and muffler media regularly to maintain
performance.
Lubrication
Lubrication
Lubrication
The pump is lubricated at the factory. It is designed
to require no further lubrication for the life of the
packings. There is no need to add an inline lubricator
under normal operating conditions.
Tighten
Tighten
Tighten Threaded
Threaded
Threaded Connections
Connections
Connections
Before each use, check all hoses for wear or damage
and replace as necessary. Check to be sure all
threaded connections are tight and leak-free. Check
mounting bolts. Check bolts. Tighten or retorque as
necessary. Although pump use varies, a general
guideline is to retorque bolts every two months. See
Flushing
Flushing
Flushing and
and
and Storage
Storage
Storage
• Flush before fluid can dry in the equipment, at the
end of the day, before storing, and before repairing
equipment.
• Flush at the lowest pressure possible. Check
connectors for leaks and tighten as necessary.
• Use solvent that is compatible with the equipment
wetted parts and the material being dispensed.
• Always flush the pump and relieve the pressure
before storing it for any length of time.
NOTICE
NOTICE
NOTICE
Flush the pump often enough to prevent the fluid
you are pumping from drying or freezing in the
pump and damaging it.
Storage:
Storage:
Storage: Pumps must be stored in an environment
where they are clean, dry, and protected from
extreme temperatures, UV radiation, and vibration.
Graco recommends an ambient temperature range of
60°F-80°F (15°C-25°C), with a humidity level below
65%.
334793A
15